In the rapidly evolving industrial landscape, the welding sector has been significantly enhanced by advancements in technology. One of the most noteworthy developments is the introduction of the Solid State High-Frequency (HF) Welder with remote control capability. This innovative equipment not only improves efficiency but also elevates the precision and quality of welding operations. In this article, we will delve into the benefits, features, and applications of solid state HF welders with remote controls, and explore how these enhancements are revolutionizing the welding industry.
What is Solid State High-Frequency (HF) Welding?
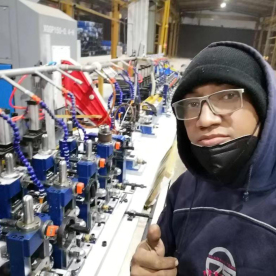
Exploring the Benefits and Innovations of Solid State HF Welder with Remote Control Technology in Modern Welding Applications
Solid state HF welding is a process that utilizes high-frequency electromagnetic fields to fuse metals. Unlike traditional welding techniques that rely on arc welding or resistance, solid state HF welding allows for a cleaner, more efficient joining of materials, especially when dealing with thin and delicate sections of metal. The solid-state aspect refers to the use of semiconductor technology, which aids in energy efficiency and robustness.
Benefits of Solid State HF Welders
1. **Energy Efficiency**: One of the most significant advantages of solid state HF welders is their energy efficiency. By using advanced semiconductor technology, these machines can minimize energy consumption while maximizing output. This efficiency translates into lower operational costs, which is beneficial for manufacturers aiming to reduce expenses.
2. **Improved Precision and Quality**: Operators can achieve improved weld quality with greater control over temperature and power settings. This precision is crucial for applications where even slight deviations can lead to failure in the weld joint. The solid state HF welder produces consistent and uniform heat, resulting in stronger welds with minimal defects.
3. **Compact Design**: Solid state technology enables the construction of more compact, lightweight welding units. Consequently, these machines are easier to incorporate into various work environments, allowing manufacturers to save valuable floor space and improve workflow efficiency.
4. **Automated Control Systems**: The addition of remote control capabilities enhances the usability of solid state HF welders. Operators can monitor and adjust welding parameters from a distance, which is particularly beneficial in large-scale operations or hazardous environments where the operator’s safety might be at risk.
5. **Versatility**: These welders are versatile and can be used for various applications, including but not limited to tube welding, wire bonding, and the joining of dissimilar materials. The flexibility allows manufacturers to adopt a single welding solution for multiple tasks, thus streamlining production processes.
Remote Control Technology in HF Welding
The incorporation of remote control technology in solid state HF welders represents a significant advancement in welding operations. This technology allows operators to:
– **Monitor Welding Parameters**: Real-time monitoring provides insights into welding parameters such as current, voltage, and temperature. Operators can make necessary adjustments quickly without needing to be physically present at the welder, ensuring optimal welding conditions throughout the process.
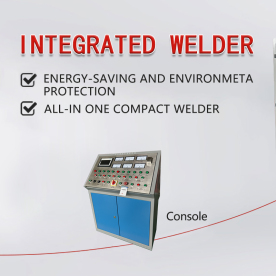
Exploring the Benefits and Innovations of Solid State HF Welder with Remote Control Technology in Modern Welding Applications
– **Enhance Safety**: By controlling the welder remotely, operators can maintain a safe distance from the welding area, especially in high-risk environments where exposure to fumes or heat may pose dangers.
– **Increase Productivity**: Remote control functionality allows for quicker responses to any issues that may arise during the welding process. This immediate access to adjustments minimizes downtime and enhances overall productivity.
Applications of Solid State HF Welders with Remote Control
1. **Automotive Industry**: These welders are increasingly being used in automotive manufacturing for applications like seam welding of body panels and joining complex assemblies.
2. **Aerospace Sector**: The precision offered by solid state HF welders is critical in the aerospace industry, where weight reduction and structural integrity are paramount.

Exploring the Benefits and Innovations of Solid State HF Welder with Remote Control Technology in Modern Welding Applications
3. **Electronics Manufacturing**: In electronics, solid state HF welders are used for wire bonding and creating connections in printed circuit boards (PCBs), where precision is essential.
4. **Medical Device Fabrication**: The medical equipment industry benefits from the capability to weld delicate components without compromising the structural integrity of the materials being welded.
Conclusion
The introduction of solid state HF welders with remote control technology has brought remarkable advancements to the welding industry. These innovative machines not only enhance efficiency and precision but also promote safety and versatility across various applications. As industries continue to seek smarter and more effective solutions, solid state HF welders are poised to become an essential tool in the future of manufacturing, offering a combination of technology and simplicity that is hard to ignore.Spare parts for Cold cutting saw machine