Induction heating has emerged as one of the most efficient ways to transfer energy, providing a solution for businesses across diverse industries. This innovative technology is especially significant in the manufacturing sector, where precision, speed, and energy efficiency are paramount. With globalization driving competition, companies are seeking ways to enhance production capabilities and reduce costs. Advanced induction heating equipment technology stands at the forefront of this evolution, offering solutions that not only streamline operations but also pave the way for enhanced product quality and environmental benefits.
At its core, induction heating involves the use of electromagnetic fields to transfer heat into conductive materials. Unlike traditional heating methods that rely on external heating elements or gas flames, induction heating delivers energy directly to the part being heated. This means that the workpiece heats up quickly while minimizing energy losses and surrounding temperature increases. As a result, induction heating technology boasts several advantages over conventional methods, making it increasingly popular across numerous applications.
One of the most notable features of advanced induction heating equipment is the precision it offers. Modern induction systems can precisely control the heating process, thus enabling manufacturers to achieve exact temperatures and heating profiles corresponding to specific production requirements. This accuracy ensures that materials are exposed to the optimal amount of heat, which enhances machining processes and improves product quality. For example, in metal treatment applications such as hardening, annealing, and forging, the use of induction heating helps achieve uniformity in the heating process, avoiding the risk of defects caused by uneven thermal expansion.
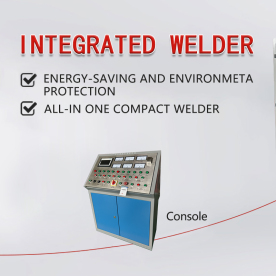
Exploring the Future of Manufacturing: How Advanced Induction Heating Equipment Technology Transforms Industrial Processes and Enhances Efficiency
In addition to precision, advanced induction heating technology is highly efficient. The ability to focus energy directly onto the target workpiece results in reduced energy consumption relative to traditional heating methods. This efficiency translates into lower operational costs for manufacturers, making advanced induction heating systems an attractive investment. Improved energy efficiency directly corresponds to reducing carbon footprints and enhancing sustainability practices, an essential consideration in today’s environmentally-conscious business landscape.
The advancements in induction heating equipment technology have also led to significant enhancements in versatility. Modern systems are designed to cater to various applications, ranging from small components to large industrial parts. Industries such as automotive, aerospace, electronics, and even food processing have recognized the value induction heating brings to their operations. For instance, in the automotive industry, induction heating is utilized for soldering and brazing processes, enabling rapid temperature control without the risk of damaging surrounding components. As manufacturers continue to explore new materials and production methods, flexible induction heating systems that adapt to various specifications will be paramount.
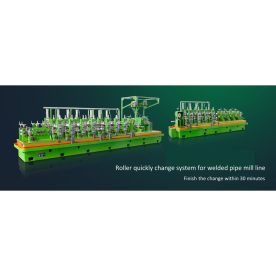
Exploring the Future of Manufacturing: How Advanced Induction Heating Equipment Technology Transforms Industrial Processes and Enhances Efficiency
Moreover, automation in the form of smart induction heating equipment is revolutionizing the manufacturing sector. With the integration of technology such as IoT (Internet of Things), manufacturers can monitor and manage the heating process remotely. Smart systems gather data regarding the performance and efficiency of the heating equipment, allowing for predictive maintenance and minimizing downtime. As manufacturers strive to optimize their supply chains and reduce lead times, having real-time insights into the heating process can significantly enhance productivity.
The future of advanced induction heating equipment technology looks promising. Continuous innovations in materials, inverter technologies, and advanced control systems are driving the development of more sophisticated induction heating solutions. As research evolves, we can expect to see induction heating systems becoming more compact, energy-efficient, and capable of handling increasingly complex heating tasks.

Exploring the Future of Manufacturing: How Advanced Induction Heating Equipment Technology Transforms Industrial Processes and Enhances Efficiency
In conclusion, advanced induction heating equipment technology is redefining manufacturing processes across various industries. Its capability to deliver precision heating, improve energy efficiency, and support diverse applications demonstrates its pivotal role in enhancing productivity and product quality. As manufacturers seek to adapt to the fast-paced changes in market demands and sustainability requirements, embracing advanced induction heating solutions will undoubtedly be a crucial strategy for success. The adoption of this technology heralds a new era in industrial manufacturing, where efficiency and innovation go hand in hand, driving the sector into a sustainable and competitive future.All-in-one High Frequency Welder with Adjustable Power