****
In the ever-evolving landscape of manufacturing, the demand for precision, efficiency, and quality is paramount. Among various production processes, tube manufacturing plays a critical role in industries such as automotive, aerospace, construction, and furniture. The advent of advanced tube making machinery has revolutionized this sector, offering enhanced capabilities and optimization that were unimaginable decades ago. This article delves into the latest advancements in tube making equipment, the technology driving these improvements, and the benefits they provide to modern manufacturers.
The Evolution of Tube Making Machinery
Traditionally, tube manufacturing involved labor-intensive processes that required significant manual intervention. Basic machinery had limited functionalities and often struggled to meet the rising demand for customized tube dimensions and grades. As technology progressed, manufacturers began to adopt machinery equipped with computer numerical control (CNC), automation, and advanced robotics. This transformation has paved the way for advanced tube making machinery that offers high flexibility, accuracy, and speed.
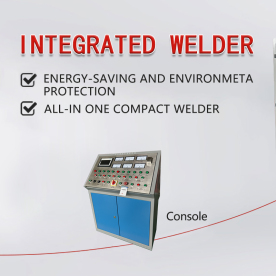
Exploring the Latest Innovations and Efficiency Improvements in Advanced Tube Making Machinery for the Modern Manufacturing Landscape
Innovations in Technology
One of the most significant technological advancements in the realm of tube making machinery is the introduction of high-speed laser cutting systems. These systems enable manufacturers to cut tubes with exceptional precision and minimal waste. Laser technology not only reduces the overall production time but also significantly lowers the costs associated with traditional cutting methods. Furthermore, modern tube making machines may include features such as multi-axis bending capabilities, allowing for complex shapes and designs to be produced without the need for extensive secondary operations.
Additionally, the integration of Industry 4.0 capabilities into tube making machinery has fundamentally changed operational efficiency. These machines often come equipped with sensors and IoT technology, enabling real-time monitoring and data collection during the manufacturing process. This connectivity allows manufacturers to conduct predictive maintenance, minimize downtime, and improve overall production quality by making data-driven decisions.
Versatility in Production
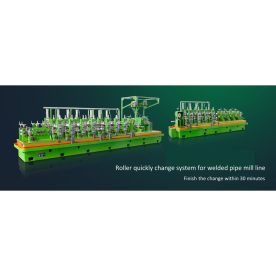
Exploring the Latest Innovations and Efficiency Improvements in Advanced Tube Making Machinery for the Modern Manufacturing Landscape
Advanced tube making machinery has also increased versatility in the production process. Today’s machines can work with a wide range of materials, including stainless steel, aluminum, and various alloys, making them suitable for a multitude of applications. Advanced tube forming technologies, like hydroforming and roll forming, can create complex geometries that were once deemed too challenging or expensive. This versatility not only opens up new possibilities for product design but also enables manufacturers to adapt quickly to changing market demands.
With the rise of custom solutions and small batch production, advanced tube making machinery is also capable of producing short runs of products without sacrificing quality. Manufacturers can quickly retool their machines for different specifications, allowing them to respond nimbly to customer needs and market trends.
Sustainability and Environmental Considerations
In today’s manufacturing environment, sustainability is a crucial consideration. Advanced tube making machinery has been designed with energy efficiency in mind, utilizing smart technology to minimize power consumption. Furthermore, the precision of modern equipment reduces material waste during production, significantly contributing to a lower environmental footprint. Many manufacturers are also investing in machines that utilize recyclable materials, further aligning their production processes with global sustainability goals.

Exploring the Latest Innovations and Efficiency Improvements in Advanced Tube Making Machinery for the Modern Manufacturing Landscape
Conclusion
As industries continue to demand higher quality, faster production times, and greater customization, advanced tube making machinery stands at the forefront of innovation. From laser cutting and CNC technology to the integration of IoT and Industry 4.0 principles, these machines are transforming how tubes are produced. The versatility and efficiency of modern tube making systems not only streamline production processes but also enable manufacturers to meet the dynamic needs of various sectors. Investing in advanced tube making machinery is not merely an option for manufacturers seeking to remain competitive; it has become a necessity in today’s fast-paced market. As technology continues to evolve, we can expect even more groundbreaking advancements in the realm of tube manufacturing that will push the boundaries of what’s possible.Specialized Spare Parts for Solid State HF Welder Maintenance