In the rapidly evolving landscape of manufacturing, technological advancements have become indispensable for enhancing production efficiency and product quality. Among these innovations, advanced tube making machinery has emerged as a significant player in various industries, including automotive, aerospace, construction, and energy. This article delves into the transformative impact of advanced tube making machinery on manufacturing processes, its capabilities, and its benefits, ultimately illustrating why it is becoming a cornerstone of modern production lines.
Historically, tube manufacturing has been a labor-intensive process, often requiring extensive manual labor and time-consuming methods to produce quality tubes. However, the introduction of advanced tube making machinery has completely changed this paradigm. These state-of-the-art machines incorporate the latest technologies in automation, precision engineering, and data analytics, leading to streamlined operations that minimize human error and enhance productivity.
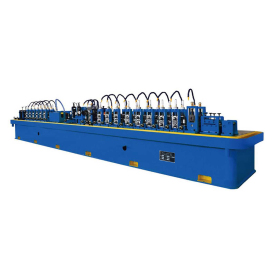
Revolutionizing Manufacturing: The Role of Advanced Tube Making Machinery in Modern Industry
One of the primary advantages of advanced tube making machinery is its ability to produce a wide range of tube sizes and shapes with high precision. Using computer numerical control (CNC) technology, manufacturers can achieve superior dimensional accuracy in the tubes they produce. This capability is crucial for industries such as aerospace and automotive, where even minor discrepancies can lead to significant performance issues or safety hazards. Advanced tube making machinery can quickly switch between different production specifications, facilitating agile manufacturing practices that allow companies to respond to changing market demands swiftly.
Moreover, these advanced machines often come equipped with integrated inspection systems that monitor the quality of the tubes in real time. By utilizing sensors and cameras, the machinery can identify defects or deviations from set standards almost instantly. This level of quality control minimizes waste and rework, leading to substantial cost savings and improved product reliability.
Another vital feature of contemporary tube-making technology is the incorporation of advanced materials and processes. Manufacturers are increasingly turning to lightweight, high-strength materials, such as carbon fiber and advanced alloys, to meet the growing demands for energy efficiency and durability in applications like automotive and aerospace engineering. Advanced tube making machinery is specifically designed to handle these innovative materials, combining sophisticated forming techniques such as extrusion, bending, and welding with adaptive control systems that adjust to the unique characteristics of each material.
The energy efficiency of advanced tube making machinery is another compelling reason for its increasing adoption in the manufacturing sector. With energy costs continually on the rise and an increasing emphasis on sustainability, manufacturers are seeking ways to reduce their environmental impact. Many modern machines are designed to operate more efficiently, using less energy while maintaining high production rates. This not only leads to lower operational costs but also aligns with global initiatives to reduce carbon footprints in manufacturing processes.
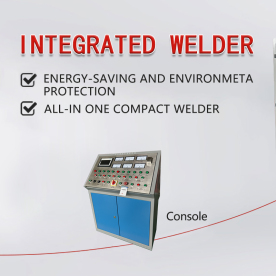
Revolutionizing Manufacturing: The Role of Advanced Tube Making Machinery in Modern Industry
In addition to the tangible benefits related to efficiency, quality, and sustainability, advanced tube making machinery can significantly enhance the overall manufacturing experience. As industries adapt to digitalization, these machines often include connectivity features that enable real-time data analysis and remote monitoring. This capability allows manufacturers to gain insights into their production processes, from machine performance to supply chain logistics. With this information at their fingertips, decision-makers can make informed adjustments, optimizing output and minimizing downtime.
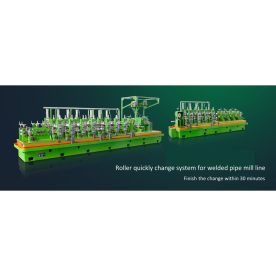
Revolutionizing Manufacturing: The Role of Advanced Tube Making Machinery in Modern Industry
Nevertheless, the transition to advanced tube making machinery is not without challenges. Initial capital investment can be substantial, particularly for smaller manufacturers. However, many industry experts argue that the long-term benefits, including reduced labor costs, improved quality control, and increased output, far outweigh these initial costs. Furthermore, as technology continues to advance, financing options and governmental incentives are becoming more accessible, making it easier for companies to invest in these advanced systems.
In conclusion, advanced tube making machinery represents a significant leap forward in manufacturing technology. By enhancing precision, reducing waste, and improving operational efficiency, these machines not only change how tubes are produced but also reshape the entire manufacturing landscape. As industries continue to evolve, embracing these advancements will be essential for remaining competitive and meeting the ever-increasing demands of the market. As such, investing in advanced tube making machinery is not just an option; it is becoming a necessity for manufacturers wishing to thrive in the modern industrial environment.Spare Parts Kit for Cold Cutting Saw Machine