****
In the world of manufacturing, the demand for efficiency, precision, and quality has never been higher. This is particularly true in industries that rely on tubing and piping systems, where the functionality and performance of components are critical. As businesses strive to meet stringent specifications and customer expectations, innovative equipment has become an essential part of the manufacturing landscape. Among the most significant advancements in this realm is the development of advanced tube making machinery. This article explores the various aspects of this technology, examining its benefits, applications, and impact on the industry.
**What is Advanced Tube Making Machinery?**
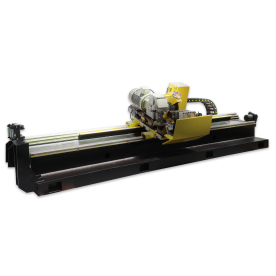
Revolutionizing the Manufacturing Process: The Role and Importance of Advanced Tube Making Machinery in Modern Production
At its core, advanced tube making machinery refers to a range of high-tech equipment utilized for producing tubes and pipes from various materials, including metals, plastics, and composites. These machines incorporate cutting-edge technologies such as precision engineering, automation, and real-time monitoring systems to enhance production efficiency and product quality. From simple tube bending machines to complex multi-process systems capable of automatic feeding, cutting, welding, and finishing, advanced tube making machinery embodies capabilities that modern manufacturers desire.
**Key Features and Technologies**
1. **Automation and Control Systems**: Modern tube making machinery often features highly automated processes, reducing the need for manual labor and minimizing human error. Advanced control systems allow for real-time monitoring and adjustments, ensuring that production remains consistent and within tolerance levels.
2. **Precision Engineering**: Accuracy is paramount in tube production. Advanced machinery utilizes high-precision components and cutting-edge technologies, such as CNC (Computer Numerical Control) systems, which enhance the feasibility of detailed designs and ensure that every tube produced meets rigorous specifications.
3. **Versatility**: Advanced tube making machinery can handle a diverse array of materials and products, from thin-walled tubing used in intricate applications to thick-walled pipes designed to withstand high pressures. This versatility makes these machines invaluable across various industries, including automotive, aerospace, medical, and construction.
4. **Rapid Prototyping and Customization**: With advanced design software and machinery capable of adjusting production on-the-fly, manufacturers can easily produce customized tubes for specific applications. This capability is particularly beneficial in industries where bespoke solutions are necessary, allowing firms to respond swiftly to market needs.
5. **Sustainability and Efficiency**: Environmental concerns have prompted manufacturers to seek ways to reduce waste and lower energy consumption. Advanced tube making machinery often incorporates technologies that optimize material usage and energy efficiency, aligning production processes with sustainability goals.
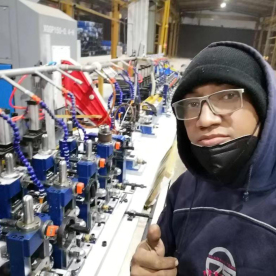
Revolutionizing the Manufacturing Process: The Role and Importance of Advanced Tube Making Machinery in Modern Production
**Applications Across Industries**
The relevance of advanced tube making machinery spans many industries. In the automotive sector, tubing is essential for fuel lines, exhaust systems, and structural components. Aerospace manufacturers rely on precision tubing for hydraulic systems and airframes, demanding the utmost accuracy and reliability from their suppliers. The medical industry, on the other hand, uses specialized tubing for applications such as catheters and stents, where sterility and precision are non-negotiable.
Additionally, construction projects increasingly leverage advanced tube making machinery for piping solutions and structural elements, ensuring that products can be produced quickly and efficiently. As industries move toward more interconnected solutions, the role of advanced tube making machinery becomes even more pronounced, driving innovation and improvement in tubular applications.
**Impact on Productivity and Quality**
The integration of advanced tube making machinery into manufacturing facilities has demonstrated transformative effects on productivity and quality metrics. By automating repetitive tasks and enhancing precision, companies can significantly reduce lead times while ensuring consistent product standards. As a result, firms can better meet customer deadlines and expectations, driving customer loyalty and repeat business.
Moreover, the introduction of monitoring and diagnostic technologies enables manufacturers to quickly identify and rectify issues in the production process. This proactive approach not only mitigates the risk of defects but also contributes to overall operational efficiency by minimizing downtime.
**Conclusion**
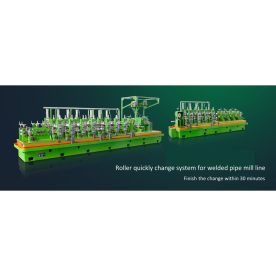
Revolutionizing the Manufacturing Process: The Role and Importance of Advanced Tube Making Machinery in Modern Production
In today’s fast-paced manufacturing environment, advanced tube making machinery represents an essential investment for companies seeking to enhance their capabilities and remain competitive. With a focus on precision, efficiency, and customization, these machines enable manufacturers to produce high-quality tubes that meet the demands of various industries. As technology continues to evolve, the future of tube production looks promising, with advanced machinery paving the way for innovative and sustainable manufacturing practices.Pipe mill production line