In the world of metal processing, efficiency and precision are paramount. As industries evolve and demand for high-quality metal products increases, manufacturers are continually seeking innovative solutions to enhance their production capabilities. One such revolutionary tool is the All-in-One High Frequency Welder, a versatile piece of equipment designed to streamline the welding process while ensuring superior quality in metal fabrication. This article explores the numerous benefits of using an All-in-One High Frequency Welder, its applications, and its impact on the future of metal processing.
Understanding High Frequency Welding
High Frequency Welding (HFW) is a process that utilizes electromagnetic energy to create welds between metal components. This method is known for its ability to deliver strong and durable welds with minimal distortion to the materials involved. The All-in-One High Frequency Welder is a multifunctional machine that combines various welding techniques into a single unit, making it an indispensable tool for metal processing companies looking to optimize their operations.
Versatility of the All-in-One High Frequency Welder
One of the most notable features of the All-in-One High Frequency Welder is its versatility. The machine is capable of performing multiple welding tasks, including but not limited to:
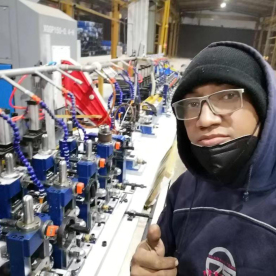
Transform Your Metal Processing Operations with an All-in-One High Frequency Welder: The Ultimate Solution for Efficiency and Precision
1. **Spot Welding:** Ideal for applications requiring localized welds, the All-in-One High Frequency Welder allows for quick and precise spot welding, reducing the need for additional equipment.
2. **Seam Welding:** This feature is especially beneficial for creating continuous welds in metal sheets and tubes, ensuring a strong bond that can withstand the test of time.
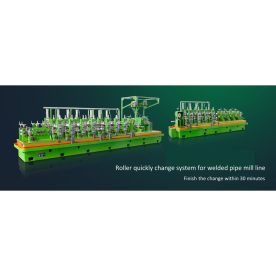
Transform Your Metal Processing Operations with an All-in-One High Frequency Welder: The Ultimate Solution for Efficiency and Precision
3. **Projection Welding:** The welder can also effectively join parts with irregular shapes, providing a reliable solution for complex metal joining applications.
4. **Brazing and Soldering:** Beyond traditional welding, the All-in-One High Frequency Welder can accommodate brazing and soldering processes, broadening its usability across different materials and specifications.
By incorporating these diverse functionalities into one machine, manufacturers can save both time and space, significantly boosting operational efficiency.
Benefits of All-in-One High Frequency Welders
1. **Enhanced Productivity**
The integration of multiple welding capabilities into a single unit allows manufacturers to streamline their operations. Workers no longer need to transition between different machines for various welding tasks, thus minimizing downtime and enhancing overall productivity. Furthermore, the All-in-One High Frequency Welder can process materials at a faster rate than traditional methods, ushering in a new era of efficiency within metal fabrication.

Transform Your Metal Processing Operations with an All-in-One High Frequency Welder: The Ultimate Solution for Efficiency and Precision
2. **Superior Quality of Welds**
With advanced technology at its core, the All-in-One High Frequency Welder delivers exceptional weld quality. The high-frequency welding process minimizes thermal distortion and reduces the heat-affected zone, leading to stronger joints and a cleaner finish. This is particularly advantageous in industries that require precise specifications, such as automotive and aerospace, where weld integrity is a critical factor.
3. **Cost Efficiency**
Integrating various welding functions into a single machine can significantly reduce capital expenditure for businesses. Rather than investing in multiple specific machines, companies can rely on the All-in-One High Frequency Welder to perform several tasks, resulting in substantial savings on both equipment and maintenance costs. Additionally, the efficiency of the welding process translates into lower energy consumption, further driving down overall operational costs.
4. **User-Friendly Operation**
Modern All-in-One High Frequency Welders are designed with user-friendly interfaces and programmable settings, allowing for easy operation and quick setup adjustments. This feature is particularly beneficial for businesses that may need to train new employees frequently, ensuring that they can quickly learn to operate the machine with minimal hassle.
Applications in the Industry
The All-in-One High Frequency Welder is versatile enough to cater to various industries, including automotive, construction, electronics, and more. From creating robust automotive components to assembling intricate electronic devices, this welding technology is poised to revolutionize how metal parts are processed. Its applicability extends to both mass production and specialized projects, making it an essential tool for any manufacturing facility.
Conclusion
In conclusion, the All-in-One High Frequency Welder presents a transformative solution for metal processing operations. With its ability to enhance productivity, improve weld quality, and reduce costs, it stands as a testament to technological advancement in the welding industry. As manufacturers seek to meet growing demands for high-quality metal products, investing in an All-in-One High Frequency Welder could be the key to achieving operational excellence and staying ahead of the competition. Embracing this innovation not only paves the way for increased efficiency but also sets the stage for a future where metal processing can be performed with unmatched precision and effectiveness.Precision Flying Saw Machine