In the rapidly evolving landscape of modern manufacturing, efficiency and quality are paramount. Companies are consistently on the lookout for innovative solutions that streamline operations, minimize costs, and enhance product integrity. One of the standout solutions that has garnered attention in recent years is the All-in-One High Frequency Welder Machine. This versatile apparatus proves to be a game changer, offering a multitude of advantages across various industries.
At its core, the All-in-One High Frequency Welder Machine employs high-frequency electrical currents to create strong, durable welds in various materials, including plastics, textiles, and metals. Unlike traditional welding methods that often require extensive equipment and prolonged setup times, this machine consolidates multiple welding functions into one unit, effectively simplifying the welding process. Manufacturers can now achieve consistent and reliable welds with minimal effort, leading to higher productivity levels.
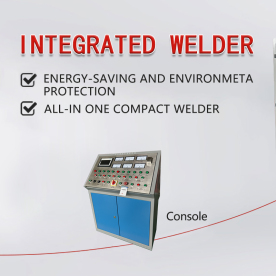
Discover the Benefits and Versatility of the All-in-One High Frequency Welder Machine for Modern Manufacturing Processes
One key benefit of the All-in-One High Frequency Welder Machine is its ability to handle a diverse range of materials. From thin films to thick industrial fabrics, the machine offers unparalleled adaptability. This makes it a valuable asset in industries such as automotive, aerospace, packaging, and textiles, where various materials often need to be joined. With dedicated settings for different types of materials, operators can quickly switch between applications, enhancing workflow efficiency.
Another significant advantage is the machine’s high-speed welding capability. The high frequency technology utilized allows for faster welding processes compared to conventional welding. This speed does not compromise quality; instead, it results in clean and precise welds. As a result, manufacturers can meet tight production deadlines without sacrificing the integrity of their products.
Moreover, the All-in-One High Frequency Welder Machine promotes energy efficiency. Traditional welding processes can be energy-intensive, resulting in increased operational costs. However, high-frequency welding consumes less energy while providing superior results. This not only reduces the carbon footprint of the manufacturing process but also contributes to significant cost savings over time, making it an environmentally and economically wise choice.
The user-friendly design of the All-in-One High Frequency Welder Machine further enhances its appeal. With an intuitive interface and advanced control systems, operators can easily navigate settings and parameters, minimizing the learning curve for new staff. Advanced models come equipped with digital displays, offering real-time feedback on welding conditions and parameters, ensuring the highest levels of precision and repeatability.
Safety is another essential aspect of welding operations, and the All-in-One High Frequency Welder Machine incorporates numerous safety features to protect both operators and equipment. These machines typically include automatic shut-off mechanisms, overcurrent protection, and emergency stop buttons. Proper safety training and equipment usage can help mitigate risks and ensure compliance with industry regulations.
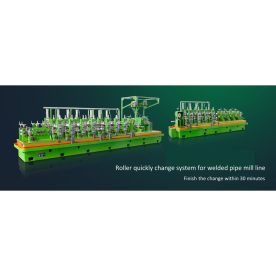
Discover the Benefits and Versatility of the All-in-One High Frequency Welder Machine for Modern Manufacturing Processes
In addition to being versatile, efficient, and user-friendly, the All-in-One High Frequency Welder Machine is known for its exceptional durability. Built with robust materials and components, these machines are designed to withstand the rigors of demanding industrial environments. Regular maintenance and proper care can further prolong their lifespan, providing manufacturers with a reliable welding solution for years to come.

Discover the Benefits and Versatility of the All-in-One High Frequency Welder Machine for Modern Manufacturing Processes
As industries continue to seek ways to improve productivity and reduce costs, investing in an All-in-One High Frequency Welder Machine becomes an increasingly attractive option. Its ability to consolidate multiple processes into one unit, coupled with its adaptability and energy efficiency, positions it as a leading choice for modern manufacturing needs.
In conclusion, the All-in-One High Frequency Welder Machine is revolutionizing the welding landscape within multiple sectors. Its combination of versatility, high-speed performance, energy efficiency, and user-friendly operation makes it an invaluable tool for today’s manufacturers. As technology continues to advance, those who embrace such innovations will undoubtedly lead the way in quality and efficiency in their respective industries. Investing in this cutting-edge technology not only meets the demands of modern manufacturing but also sets a strong foundation for future growth and success.Tailor-Made Spare Parts for Tube Mills