****
In the ever-evolving world of manufacturing and industrial applications, precision and efficiency are key factors determining the success of any production process. One groundbreaking solution that has gained immense popularity is the all-in-one high frequency welder machine. This advanced welding technology not only enhances productivity but also ensures that the finished products meet the highest quality standards. In this article, we will explore the features, benefits, and applications of the all-in-one high frequency welder machine, shedding light on why it has become a go-to choice for many industries.
What is a High Frequency Welder Machine?
A high frequency welder uses electromagnetic waves to create heat in materials, allowing for quick and efficient bonding. This process is especially effective for thermoplastics and various composite materials. The all-in-one design means that these machines can undertake multiple functions, including welding, sealing, and even cutting, offering a versatile solution for manufacturers.
Key Features of the All-in-One High Frequency Welder Machine
1. **Versatility**: One of the standout features of the all-in-one high frequency welder is its versatility. Capable of handling a wide range of materials including PVC, PU, and other thermoplastics, these machines can tackle multiple applications from automotive components to consumer goods.
2. **Time Efficiency**: Traditional welding methods can be time-consuming. However, the all-in-one high frequency welder machine accelerates the process by producing strong bonds in less time. This allows manufacturers to optimize production lines and ultimately increase output.
3. **Precision**: When it comes to welding, accuracy is paramount. The all-in-one machine is designed to deliver precise results, minimizing material wastage and ensuring the quality of the finished product. This feature is particularly advantageous in industries where detail is critical.
4. **User-Friendly Interface**: Modern machines come equipped with intuitive touch screens and user-friendly interfaces that simplify operation. This ensures that operators can quickly learn and adapt to the machinery, reducing training time and minimizing errors.
5. **Energy Efficiency**: High frequency welding is known for its low energy consumption compared to other welding methods. Manufacturers are increasingly adopting these systems not only for their effectiveness but also for their reduced carbon footprint.
Advantages of Using an All-in-One High Frequency Welder Machine
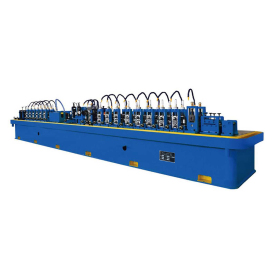
Discover the Versatility and Efficiency of the All-in-One High Frequency Welder Machine for Your Industrial Needs
1. **Cost-Effective Production**: By integrating various functions into one machine, businesses can save on equipment costs and maintenance. This streamlined approach helps minimize operational expenses while maximizing efficiency.
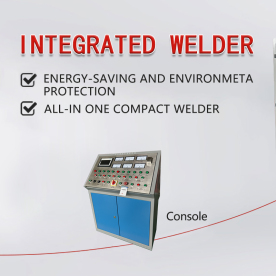
Discover the Versatility and Efficiency of the All-in-One High Frequency Welder Machine for Your Industrial Needs
2. **Enhanced Quality Control**: The consistent quality provided by high frequency welding means that products meet strict industry standards, reducing the likelihood of defects and returns. This reliability enhances customer satisfaction.
3. **Flexibility in Production Lines**: The ability to quickly switch between different applications makes the all-in-one welder ideal for diverse manufacturing needs. It allows businesses to adapt to changing market demands without investing in additional equipment.
4. **Improved Safety**: Modern high frequency welders come with advanced safety features, including emergency shut-off mechanisms and automatic monitoring systems. These enhancements not only protect the operators but also minimize the risks associated with traditional welding techniques.
Applications of the All-in-One High Frequency Welder Machine
The versatility of the all-in-one high frequency welder machine makes it suitable for numerous industries. In the automotive sector, these machines are utilized for bonding interior components, while the packaging industry employs them for sealing bags and containers. Furthermore, manufacturers in the textiles sector use high frequency welding to create durable seams in specialized fabrics.
In the medical device industry, precise welding is crucial, and the all-in-one high frequency welder has proven invaluable for producing sterile components. Its applications extend into electronics, where it is used for creating reliable connections in various devices.
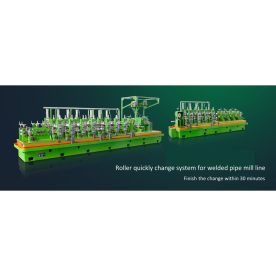
Discover the Versatility and Efficiency of the All-in-One High Frequency Welder Machine for Your Industrial Needs
Conclusion
In conclusion, the all-in-one high frequency welder machine stands out as a pivotal tool in modern manufacturing, combining efficiency, versatility, and precision into one compact design. As industries seek to enhance production capabilities while maintaining quality, these machines offer an innovative solution that can cater to diverse needs. Forward-thinking businesses that adopt this technology will not only improve their operational processes but also position themselves favorably in a competitive marketplace. Embracing the all-in-one high frequency welder machine could be the key to unlocking new levels of productivity and success in your manufacturing endeavors.High-Wear-Resistant Spare Parts for Tube Mills