****
Welding technology has come a long way since its inception, witnessing remarkable advancements that make the process more efficient, precise, and versatile. Among the latest innovations, the All-in-One High Frequency Welder Machine has emerged as a game-changer in various industries, from manufacturing to automotive, textile, and beyond. This article delves into what makes this machine stand out, its myriad benefits, features, and applications.
Understanding All-in-One High Frequency Welder Machines
At its core, an All-in-One High Frequency Welder Machine integrates several functions into one unit, eliminating the need for multiple machines. Typically, these welders are capable of accomplishing high-frequency welding, which utilizes electromagnetic energy to bond materials, especially thermoplastics. This process is particularly advantageous because it reduces production time while enhancing the quality of the weld.
The innovative design does not merely allow for welding; it can fuse, cut, and even emboss materials with remarkable precision. With the ability to work on a variety of materials, from thin films to thicker sheets, these machines are ideal for businesses looking to streamline their production processes.
Key Features of High Frequency Welder Machines
1. **Multi-Functionality**: The “All-in-One” aspect speaks to the versatility of the machine. It allows operators to switch between different welding techniques, including high-frequency, ultrasonic, and frequency conversion welding, all without the need for tool changes or extensive setups.
2. **Compact Design**: Unlike traditional welding setups that may require significant floor space and operational adjustments, modern All-in-One High Frequency Welders are designed with compactness in mind. This not only saves valuable workspace but also makes it easier to transport and set up in various production environments.
3. **User-Friendly Interface**: Most machines come equipped with intuitive controls, allowing even novice operators to quickly become proficient. Touchscreen interfaces enable real-time adjustments and monitoring of the welding process, ensuring consistent results.
4. **Energy Efficiency**: High frequency welders are designed to maximize energy use while minimizing waste. They significantly reduce operational costs by lowering energy consumption compared to traditional welding methods.
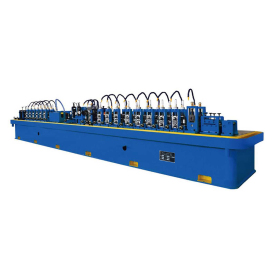
Revolutionizing the Welding Industry: The Complete Benefits and Features of an All-in-One High Frequency Welder Machine
5. **Precision and Quality**: The technology ensures that welds are not just strong but also uniform and aesthetically pleasing. The ability to monitor and control various parameters in real-time leads to a consistent product, reducing the likelihood of defects or reworks.
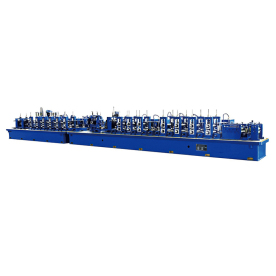
Revolutionizing the Welding Industry: The Complete Benefits and Features of an All-in-One High Frequency Welder Machine
6. **Safety Features**: Modern machines incorporate safety mechanisms designed to protect operators and the work environment. Features such as emergency stop buttons, protective covers, and automatic shut-off capabilities help mitigate risks commonly associated with welding tasks.
Applications Across Industries
1. **Textile Manufacturing**: The All-in-One High Frequency Welder is indispensable in the textile industry, where it is used for welding and sealing fabrics, producing durable seams that withstand wear and tear.
2. **Automotive Sector**: In automotive manufacturing, these machines are employed for bonding plastic components, harnesses, and even in the production of high-performance screens and dashboards.
3. **Packaging**: The packaging industry benefits from high frequency welding during the production of flexible packages that require sealed seams that are both durable and resistant to moisture and contaminants.

Revolutionizing the Welding Industry: The Complete Benefits and Features of an All-in-One High Frequency Welder Machine
4. **Medical Devices**: A variety of medical devices require high precision and sterile conditions. High-frequency welders are crucial for manufacturing components without compromising hygiene.
5. **Electronics**: In the electronics industry, these welders are used to seal casings and assemblies, ensuring that products are protected against dust and moisture.
The Bottom Line
The All-in-One High Frequency Welder Machine has revolutionized the way we approach welding and fabrication in diverse industries. With its multi-functionality, energy efficiency, and the capacity to ensure high-quality welds, it presents an attractive option for businesses seeking to optimize production and heighten product quality. Investing in this modern welding technology is not just a step toward efficiency but also a leap into the future of manufacturing practices. As industries continue to evolve and demand for precision rises, adopting innovative solutions like the All-in-One High Frequency Welder Machine will be crucial for staying competitive in the marketplace.Customized ERW tube mill solutions