****
In the fast-paced world of modern manufacturing, the need for efficient and precise welding techniques is critical. Among the advancements in welding technology, the all-in-one high frequency welder with adjustable power has emerged as a game-changer. This innovative device combines the benefits of versatility, power adaptability, and compact design, making it an invaluable tool for various industries. In this article, we will explore the features and advantages of this cutting-edge welding solution and how it can improve production processes, reduce costs, and enhance overall product quality.
Understanding High Frequency Welding Technology
High frequency welding is a process that uses electromagnetic induction to produce heat through the resistance of metal to high-frequency electrical currents. This method is particularly effective for welding thermoplastics and other materials, as it can generate heat quickly and efficiently. The applications of high frequency welding span multiple sectors, including automotive, textiles, packaging, and medical devices, making it a versatile solution.
The all-in-one high frequency welder streamlines this process by integrating various functionalities into one unit. Traditionally, welding operations required multiple machines for different welding techniques; however, the all-in-one solution simplifies this by providing capabilities that accommodate diverse welding requirements.
Adjustable Power: Flexibility at Your Fingertips
One of the standout features of the all-in-one high frequency welder is its adjustable power settings. This allows operators to customize the welding process based on the specific requirements of each job, ensuring optimal performance and outcomes. The adjustable power feature provides the following benefits:
1. **Material Compatibility:** Different materials require different levels of power for effective welding. With adjustable power settings, operators can switch between high and low frequencies to cater to various material types, such as PVC, EVA, and polyurethane, without compromising the quality of the weld.
2. **Precision Control:** The ability to adjust power levels allows for more precise control over the welding process. This precision is crucial for projects that demand intricate designs or specific tolerances, as it minimizes the risk of overheating or damaging the workpiece.
3. **Reduced Energy Consumption:** Customizing the power output not only enhances welding quality but also contributes to energy savings. By optimizing the power for each task, businesses can lower their energy costs while maintaining efficiency, leading to a more sustainable production process.
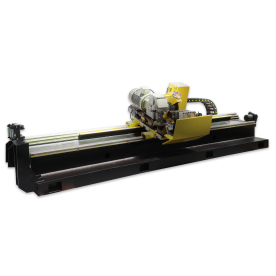
Unlocking Efficiency and Precision: The Advantages of All-in-One High Frequency Welder with Adjustable Power for Modern Manufacturing
Enhanced Efficiency and Productivity
Integrating an all-in-one high frequency welder with adjustable power can significantly enhance workflow efficiency and productivity. The key advantages include:
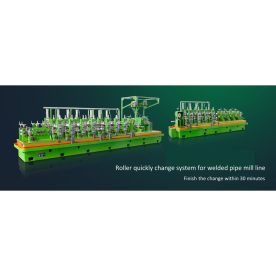
Unlocking Efficiency and Precision: The Advantages of All-in-One High Frequency Welder with Adjustable Power for Modern Manufacturing
– **Compact Design:** By combining multiple welding functionalities into a single unit, manufacturers can save valuable floor space in their facilities. The compact design also makes transportation and setup easier, reducing the time required to switch between processes.
– **Faster Setup Times:** Traditional welding methods often involve lengthy setup times and extensive adjustments. With an all-in-one welder, the setup process is simplified, allowing operators to quickly transition from one project to another without significant downtime.
– **Makings of Quality Welds:** Consistent weld quality is essential in manufacturing. The adjustable power mechanism helps ensure that each weld is uniform, free from defects, and meets strict quality standards, thus minimizing rework and waste.
User-Friendly Interface
Modern all-in-one high frequency welders are designed with user-friendly interfaces, ensuring that operators can easily adjust settings and monitor the welding process. The advanced digital displays provide real-time feedback on power levels, temperature, and other critical metrics, allowing for informed adjustments on the fly. This intuitive interface makes it easier for both novice and experienced welders to operate the machine, reducing the learning curve associated with traditional welding equipment.

Unlocking Efficiency and Precision: The Advantages of All-in-One High Frequency Welder with Adjustable Power for Modern Manufacturing
Conclusion
In conclusion, the all-in-one high frequency welder with adjustable power is a transformative tool for the manufacturing sector. Its versatility, precision, and efficiency contribute to enhanced workflow, reduced operational costs, and superior product quality. As industries continue to evolve, investing in advanced welding technology like this will be crucial for businesses striving to maintain a competitive edge. By adopting such innovations, manufacturers not only improve their processes but also prepare themselves for the future of production, where adaptability and efficiency are paramount.Precision Mould for Tube Mills