****
In today’s rapidly evolving manufacturing landscape, the demand for high-quality steel tubes and pipes is greater than ever. One of the most effective solutions to meet this demand is the Automatic Electric Resistance Welding (ERW) tube mill equipment. This technology not only enhances production efficiency but also ensures the delivery of precision-crafted products that cater to various industrial needs. This article delves into the functionality, advantages, and applications of automatic ERW tube mill equipment, highlighting its crucial role in the manufacturing sector.
Understanding Automatic ERW Tube Mill Equipment
Electric Resistance Welding (ERW) is a process where steel strips or coils are formed into a tube shape and welded using electrical resistance heat at the seam. An automatic ERW tube mill equipment optimizes this process, allowing for continuous operation with minimal manual intervention. The setup typically includes a series of components, such as uncoilers, accumulator, levelers, forming stations, welding modules, and cooling systems, all integrated into a seamless production line.
Key Components of ERW Tube Mill Equipment
1. **Uncoiler**: This component feeds the steel coil into the mill. Automatic uncoilers are designed to hold and uncoil heavy coils of steel, ensuring a consistent material supply.
2. **Accumulator**: An accumulator stores additional material, allowing continuous operation of the mill even during brief interruptions or changes in coil feeds.
3. **Levelers and Formers**: Levelers flatten the steel strip, while forming rolls shape it into a round or square tube profile. Advanced mills feature adjustable roll setups that can accommodate various tube sizes.
4. **Welding Module**: This is where the fundamental ERW process occurs. The edges of the tube are heated and joined through an electric current. Modern welding modules can monitor and adjust parameters in real-time, enhancing welding integrity.
5. **Cooling and Sizing Sections**: Post-welding, tubes undergo a cooling process, followed by sizing to ensure uniform diameter and wall thickness. This is crucial for fulfilling specific application requirements.
6. **Cut-to-Length Systems**: The final tubes are measured and cut to desired lengths, suitable for various applications across industries.
Advantages of Using Automatic ERW Tube Mill Equipment
1. **Increased Efficiency**: Automatic ERW tube mill equipment allows for high-speed production with minimal downtime. This capability is crucial for manufacturers looking to meet large orders without sacrificing quality.
2. **Consistent Quality**: Automation minimizes human error, ensuring that the quality of the produced tubes is consistent. Each tube meets strict industry standards, which is vital for industries such as construction, automotive, and energy.
3. **Cost-Effectiveness**: Automation leads to reduced labor costs and increased throughput. While the initial investment in such equipment may be significant, the long-term savings and efficiency gains typically justify the cost.
4. **Flexibility**: Modern automatic ERW tube mills can be easily adjusted to produce varying sizes and shapes of tubes, making them suitable for diverse applications.
5. **Environmentally Friendly**: Many automatic ERW tube mills are designed with energy efficiency in mind, reducing the carbon footprint associated with steel production. Moreover, the reduced scrap rate ensures better resource utilization.
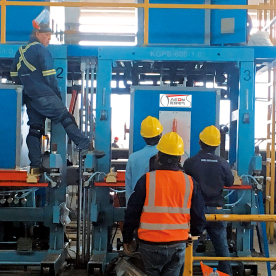
Exploring the Efficiency and Innovation of Automatic ERW Tube Mill Equipment in Modern Manufacturing Processes
Applications of Automatic ERW Tube Mill Equipment
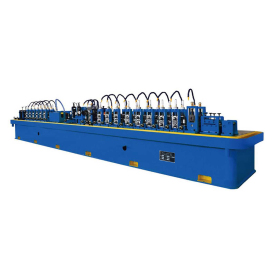
Exploring the Efficiency and Innovation of Automatic ERW Tube Mill Equipment in Modern Manufacturing Processes
Automatic ERW tube mill equipment is widely used across multiple sectors, including:

Exploring the Efficiency and Innovation of Automatic ERW Tube Mill Equipment in Modern Manufacturing Processes
– **Construction**: Steel tubes are fundamental in structural applications, such as scaffolding, frames, and fittings.
– **Automotive**: ERW tubes are commonly used in vehicle manufacturing for exhaust systems, chassis components, and more.
– **Energy**: The oil and gas industry relies on durable ERW tubes for pipelines and fittings, ensuring safe transportation of resources.
– **Manufacturing**: From machinery supports to furniture, the versatility of ERW tubes makes them indispensable in various manufacturing processes.
Conclusion
The integration of automatic ERW tube mill equipment into the manufacturing process signifies a notable advancement in efficiency, quality, and flexibility. As industries continue to evolve, the importance of this technology will only grow, enabling manufacturers to produce high-quality tubes that meet the stringent demands of modern applications. By investing in such innovative equipment, businesses can enhance their operational capabilities and stay competitive in a global market.High-Quality Spare Parts for Annealing Machine