In the rapidly evolving world of manufacturing, the demand for efficient, reliable, and high-quality welding solutions has never been more critical. Among the myriad of welding technologies available, the automatic high-frequency welder has emerged as a game changer. Known for its ability to provide rapid welding processes with exceptional precision, this innovative tool has transformed how industries approach the joining of various materials. This article delves into the advantages and applications of automatic high-frequency welders, illustrating their significant impact on modern manufacturing.
Understanding Automatic High-Frequency Welding
High-frequency welding, often referred to as radio frequency (RF) welding, is a specialized process that employs electromagnetic energy to heat and join materials. This method is particularly effective for thermoplastic materials, as it generates heat at the molecular level, resulting in a strong, consistent weld. Automatic high-frequency welders are designed to automate this process, offering efficiencies and benefits that manual welding methods simply cannot match.
Key Advantages of Automatic High-Frequency Welders
1. **Speed and Efficiency**: One of the most significant advantages of automatic high-frequency welders is their speed. The automated process allows for rapid production cycles, significantly increasing output compared to traditional welding methods. As industries strive to keep up with demand, the ability to produce high-quality welds quickly is invaluable.
2. **Precision and Consistency**: Automatic welders are programmed to deliver precise welding parameters, ensuring consistent results across multiple pieces. This precision minimizes the risk of defects, reducing waste and the need for extensive quality control processes. As a result, manufacturers can deliver products of consistently high quality, reducing the likelihood of customer complaints or returns.
3. **Versatility**: Automatic high-frequency welders are adaptable and can handle various materials, including plastics, composites, and even some textiles. This versatility allows manufacturers to expand their product lines without investing in multiple welding technologies, making it a cost-effective solution in the long run.
4. **Reduced Labor Costs**: By automating the welding process, companies can decrease their reliance on manual labor. Workers are freed up to focus on more complex tasks that require skill and attention, while the automated system handles repetitive welding operations. This shift not only lowers labor costs but also helps to minimize workplace injuries associated with manual welding.
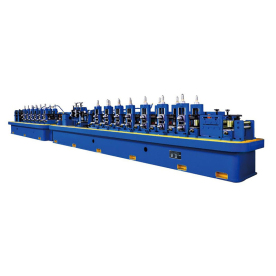
Exploring the Advantages and Applications of the Automatic High-Frequency Welder in Modern Manufacturing Processes
5. **Energy Efficiency**: Automatic high-frequency welders are designed with energy efficiency in mind. By focusing heat directly on the welding area, these machines minimize energy waste, contributing to lower operational costs and a reduced carbon footprint.
Applications in Various Industries
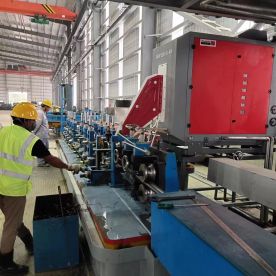
Exploring the Advantages and Applications of the Automatic High-Frequency Welder in Modern Manufacturing Processes
The applications of automatic high-frequency welders span across multiple industries, showcasing their versatility and effectiveness.
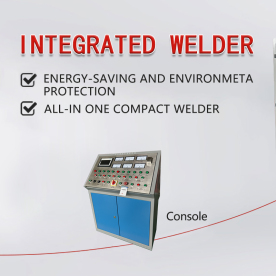
Exploring the Advantages and Applications of the Automatic High-Frequency Welder in Modern Manufacturing Processes
– **Textile and Fashion**: In the textile industry, automatic high-frequency welders are used to join fabrics, create seams, and seal materials in products ranging from clothing to outdoor gear. Their ability to produce strong and waterproof seams makes them ideal for items like rain jackets and tents.
– **Packaging**: In packaging applications, these welders are instrumental in creating sealed pouches and bags. The automatic nature of the process ensures that high-volume production is both fast and consistent, which is essential for meeting the demands of consumer goods and pharmaceuticals.
– **Automotive**: The automotive sector also benefits from high-frequency welding. It is used for fabricating parts like dashboards, seat covers, and insulation materials. The ability to create strong, durable joints is critical in ensuring the longevity and safety of automotive components.
– **Medical Devices**: In the medical industry, where quality and precision are paramount, automatic high-frequency welders are used to assemble medical bags, tubing, and other critical components. The automation aspect ensures a high degree of sterility and quality control, essential in medical applications.
Conclusion
The automatic high-frequency welder represents a significant advancement in welding technology, offering unparalleled speed, precision, and versatility across various industries. As manufacturing processes continue to evolve and the demand for high-quality products increases, the role of automatic high-frequency welders will undoubtedly become more prominent. By embracing this innovative technology, manufacturers can not only improve their production capabilities but also enhance product quality, ultimately leading to increased customer satisfaction and competitive advantage in the marketplace. As industries look to the future, investing in automatic welding solutions will be a key strategy in meeting the challenges ahead.Specialized Spare Parts for Solid State HF Welder Maintenance