Introduction
In the landscape of modern manufacturing and construction, welding techniques continuously evolve to meet the increasing demands for efficiency, strength, and precision. Among these advancements, the Automatic High Frequency Welder has emerged as an innovative solution, revolutionizing the way metals are joined together. This article delves into the myriad benefits and applications of automatic high frequency welding technology, explaining why it’s becoming an essential tool across various industries.
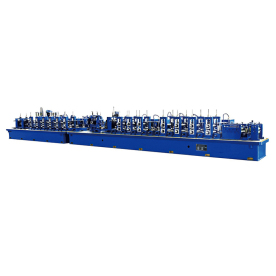
Exploring the Benefits and Applications of Automatic High Frequency Welder: A Game Changer in Modern Welding Technology
Understanding Automatic High Frequency Welding
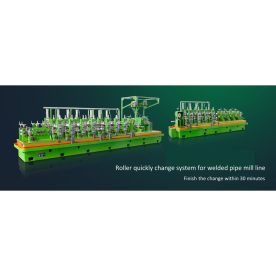
Exploring the Benefits and Applications of Automatic High Frequency Welder: A Game Changer in Modern Welding Technology
Automatic high frequency welding (AHFW) is a process primarily used for welding metal tubes and sheets. This technique utilizes a high-frequency electrical current to generate heat, which fuses the metal components together without requiring filler materials. By employing this method, manufacturers can achieve strong, reliable welds with minimal distortion and a smooth finish.
The operation of an automatic high frequency welder is straightforward. The machine generates a high-frequency electromagnetic field, which induces current in the workpieces when they are brought together. The heat generated through this process raises the temperature of the metal to its melting point, allowing for seamless joining. The automation component of the welder enhances speed and consistency, significantly improving productivity compared to traditional welding methods.
Benefits of Automatic High Frequency Welding
1. **Increased Efficiency**: One of the most significant advantages of automatic high frequency welders is their efficiency. The speed of the welding process, combined with the automation technology, allows businesses to produce significant quantities of welds in shorter time frames. This is particularly beneficial for operations that require mass production.
2. **High Quality and Consistency**: Automatic welder systems offer superior control over the welding parameters, which leads to higher quality welds with minimal defects. The precision of the automatic processes ensures that each weld meets the required specifications, reducing the risk of human error.
3. **Versatility**: Automatic high frequency welders can be used on a variety of materials, including different grades of steel, stainless steel, and non-ferrous alloys. This versatility makes them suitable for numerous applications, from automotive manufacturing to the production of pipes and tubes.
4. **Less Material Waste**: Compared to traditional welding methods, AHFW generates less waste. The process does not require additional filler materials, which not only saves costs but also reduces the environmental impact of manufacturing operations.
5. **Reduced Labor Costs**: With automation comes the reduction of labor costs. Automatic welding machines often require fewer operators than manual welding processes, allowing companies to allocate their workforce to other essential tasks while maintaining high productivity levels.
Applications of Automatic High Frequency Welders
The applications of automatic high frequency welders are vast and diverse. They find prominence in various sectors, including:
– **Automotive Industry**: In automotive manufacturing, automatic high frequency welding is used to produce exhaust pipes, fuel tanks, and other essential components. The strength and structural integrity obtained from this welding method are crucial for safety and performance.
– **Construction**: The construction industry utilizes automatic welding for fabricating structural steel elements, where precision and quality are paramount. The capability to make flawless joints is essential for ensuring the durability and safety of buildings and infrastructure.
– **Manufacturing of Tubes and Pipes**: Automatic high frequency welding is predominantly used in producing tubes and pipes for plumbing, HVAC systems, and more. Manufacturers can produce lengthy sections with consistent wall thickness, ensuring high performance in the end product.
– **Electronics**: The electronics industry uses AHFW in the manufacturing of components such as capacitors and transformers, where strong and reliable electrical connections are necessary.
Conclusion

Exploring the Benefits and Applications of Automatic High Frequency Welder: A Game Changer in Modern Welding Technology
The Automatic High Frequency Welder represents a significant advancement in welding technology. With its numerous benefits, including increased efficiency, high-quality welds, versatility, and reduced labor costs, this method is changing the face of manufacturing across various industries. As technology evolves, we can anticipate even more innovative applications and improvements in automatic high frequency welding, paving the way for a more efficient and sustainable future in metalworking. By investing in this modern welding technology, businesses can improve their productivity and maintain a competitive edge in an increasingly fast-paced market.Solid State HF Welder Replacement Parts