In the ever-evolving landscape of manufacturing and metalworking, the quest for efficiency, precision, and innovation drives industries to explore advanced technologies. Among the forefront of these innovations is automatic induction heating equipment, a game-changer that is transforming how metals are processed and manipulated. This article delves into the functionality, benefits, and diverse applications of automatic induction heating equipment, showcasing its impact on modern manufacturing practices.
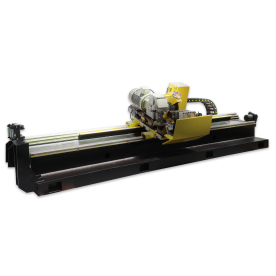
Revolutionizing Metal Processing: The Benefits and Applications of Automatic Induction Heating Equipment in Modern Manufacturing
Induction heating is a process that utilizes electromagnetic fields to generate heat directly within conductive materials. Unlike traditional heating methods that rely on external heat application, induction heating focuses on heating the object itself through electromagnetic induction. This mechanism enables rapid heating, providing significant advantages in terms of speed, energy efficiency, and precision.
**Functionality of Automatic Induction Heating Equipment**
Automatic induction heating equipment comprises several key components, including induction coils, power supplies, and control systems. The induction coil creates a magnetic field that induces electrical currents in the metal object. As these currents flow through the resistance of the metal, heat is generated, allowing for precise control over the temperature. The automatic feature of these systems means that they can be programmed to achieve specific heating profiles, adjusting parameters like temperature and duration without manual intervention.
One of the standout features of automatic induction heating equipment is its ability to heat parts uniformly and selectively. This uniformity minimizes the risk of thermal distortion and ensures that the metal reaches the desired temperature uniformly, which is crucial for processes like hardening, forging, and brazing. Furthermore, with integration capabilities, these systems can easily connect to existing manufacturing lines, enhancing workflow without requiring significant redesign or investment.
**Benefits of Automatic Induction Heating Equipment**
The advantages of using automatic induction heating equipment in manufacturing are vast. Here are some key benefits that industries have come to appreciate:
1. **Increased Efficiency**: Induction heating significantly reduces the time required for heating compared to traditional methods. As a result, production cycles are shortened, enabling manufacturers to fulfill orders faster and respond more dynamically to market demands.
2. **Energy Savings**: Induction heating systems are highly energy-efficient. They convert a higher percentage of electrical energy into usable heat, reducing wasted energy and lowering electricity costs. This efficiency is not only beneficial for the bottom line but also aligns with the growing demand for sustainable manufacturing practices.
3. **Precision and Control**: Automatic induction heating equipment allows for precise temperature control, which is vital for processes that require exact heating specifications. The ability to program specific profiles ensures that each part is processed according to exacting standards, enhancing overall product quality.
4. **Reduced Risk of Overheating**: The inherent design of induction heating minimizes the risk of overheating or damaging parts due to human error. The automatic controls can respond in real-time to ensure that the metal does not exceed predetermined temperature thresholds.
5. **Versatility**: Automatic induction heating can be applied to a wide range of metals and processes, from hardening and annealing to soldering and brazing. This versatility makes it an attractive option for various sectors, including automotive, aerospace, and consumer goods.
**Applications in Modern Manufacturing**
The applications of automatic induction heating equipment span a broad spectrum of industries. In the automotive sector, manufacturers utilize these systems for heat treatment processes, ensuring components achieve the necessary hardness and structural integrity. Similarly, in the aerospace industry, precise and controlled heating is critical for fabricating parts that must withstand extreme conditions.
Another area where automatic induction heating is making a significant impact is in the agricultural machinery sector. Farmers are increasingly adopting technologies that enhance the durability and efficiency of their equipment, and induction heating plays a vital role in optimizing metal components.
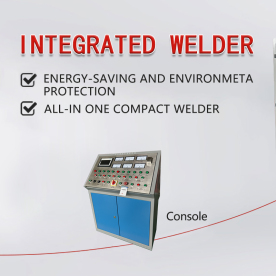
Revolutionizing Metal Processing: The Benefits and Applications of Automatic Induction Heating Equipment in Modern Manufacturing
In conclusion, automatic induction heating equipment is not just a technological advancement; it is a transformative solution that enhances manufacturing efficiency, improves product quality, and supports sustainable practices. By leveraging the power of induction heating, industries can stay competitive in a rapidly changing environment, meeting the demands of both the market and the future of manufacturing.
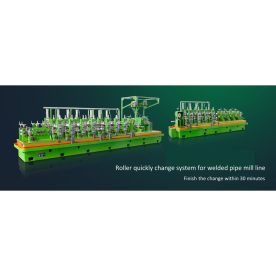
Revolutionizing Metal Processing: The Benefits and Applications of Automatic Induction Heating Equipment in Modern Manufacturing
As companies continue to embrace these innovations, the future of metal processing looks bright, with automatic induction heating equipment leading the charge toward more efficient and effective manufacturing processes.Cold cutting saw machine