In the ever-evolving landscape of manufacturing, industries are continuously seeking methods to enhance productivity, reduce waste, and improve the quality of products. Among the many advancements in metal processing technology, the introduction of cold cutting saw machines has emerged as a significant game changer. This article delves into the benefits, applications, and operational principles of cold cutting saw machines, emphasizing their importance in the manufacturing sector.
Cold cutting saw machines are specialized tools designed primarily for cutting through various types of metal with precision and efficiency. Unlike traditional saws that generate excessive heat during the cutting process, cold cutting saws utilize a unique mechanism that minimizes friction and heat production. This process not only results in superior cutting quality but also extends the lifespan of the saw blades.
One of the primary advantages of cold cutting saw machines for metal is their ability to produce clean and precise cuts. The cold cutting process significantly reduces burr formation, which is often a byproduct of heat-generating cutting methods. This cleanliness is crucial in industries where metal parts must meet tight tolerances or be assembled with other components. In applications such as automotive manufacturing, aerospace engineering, and construction, where precision is paramount, the use of cold cutting saw machines can enhance both the quality and aesthetics of the finished products.
Another notable benefit of cold cutting saw machines is the reduction in thermal distortion. Metal components can warp or change shape when subjected to high temperatures during cutting. Cold cutting provides a solution by maintaining the material’s integrity and structural properties. This characteristic is especially beneficial when working with sensitive materials, such as aluminum and titanium, which can be particularly susceptible to heat-related deformation.
The versatility of cold cutting saw machines makes them suitable for a wide range of applications across various industries. They can effortlessly cut through different metal types, including steel, stainless steel, and other alloys. This flexibility allows manufacturers to streamline their operations, as one machine can handle multiple tasks, reducing the need for specialized equipment that takes up valuable factory space.
In terms of operational efficiency, cold cutting saw machines are designed to maximize productivity while minimizing downtime. Many models come equipped with automatic feeding systems, which enhance the cutting process’s efficiency by allowing for continuous operation without the need for constant supervision. This automation not only saves time and labor costs but also minimizes human error, resulting in uniformity in production.
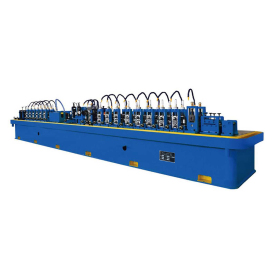
Exploring the Benefits and Applications of Cold Cutting Saw Machines for Metal in Modern Manufacturing
Maintenance is another critical aspect of cold cutting saw machines that sets them apart from traditional cutting methods. Because they operate at cooler temperatures, there is less wear on the saw blades, leading to longer service intervals and reduced maintenance costs. Moreover, the robust design of these machines ensures durability, making them a sound investment for manufacturing businesses.
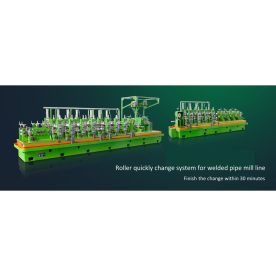
Exploring the Benefits and Applications of Cold Cutting Saw Machines for Metal in Modern Manufacturing
Additionally, cold cutting saw machines are environmentally friendly due to their operation. The cold cutting process generates minimal waste and requires less energy compared to conventional cutting machines. This efficiency aligns with the growing emphasis on sustainability in manufacturing, as businesses seek to reduce their carbon footprint and implement eco-friendlier practices.

Exploring the Benefits and Applications of Cold Cutting Saw Machines for Metal in Modern Manufacturing
While the advantages of cold cutting saw machines are extensive, it is essential for manufacturers to assess their specific needs and consider the initial investment required for such machinery. As with any advanced technology, the upfront costs can be higher than traditional cutting tools. However, the long-term savings from increased efficiency, reduced waste, and enhanced product quality often justify the investment.
In conclusion, cold cutting saw machines for metal are revolutionizing the way manufacturers approach metal processing. Their ability to deliver precise, clean cuts while maintaining material integrity positions them as an invaluable tool in various industrial applications. As the manufacturing sector grows more competitive, incorporating cold cutting technology can provide businesses with the edge they need to thrive. Embracing such advancements will not only optimize production processes but also yield higher quality outputs, benefiting manufacturers and consumers alike.Pipe mill production line with welding and cutting functions