In the world of manufacturing, pipe mills play a crucial role in producing pipes that are essential for various industries such as construction, oil and gas, and water supply. To meet the increasing demand for pipes, it is important to have a complete pipe mill production line solution that can streamline the manufacturing process and improve efficiency.
A complete pipe mill production line solution consists of various components that work together to produce high-quality pipes in a cost-effective manner. These components include pipe forming machines, welding equipment, cutting machines, and inspection systems. By integrating these components into a seamless production line, manufacturers can achieve high productivity and consistent quality in their pipe production.
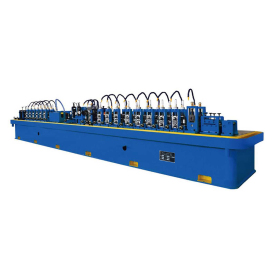
Complete Pipe mill production line solution: Everything you need to know
One of the key components of a pipe mill production line is the pipe forming machine. This machine is responsible for shaping the raw material, usually a coil of steel, into a pipe of the desired diameter and thickness. There are different types of pipe forming machines available, such as ERW (Electric Resistance Welding) machines, seamless pipe mills, and spiral pipe mills, each suited for specific types of pipes.
Another important component of a pipe mill production line is the welding equipment. Welding is a crucial step in the pipe manufacturing process, as it creates a strong and durable seam that holds the pipe together. There are various welding techniques used in pipe manufacturing, including high-frequency welding, submerged arc welding, and laser welding. The choice of welding technique depends on the material being used and the specifications of the pipes being produced.
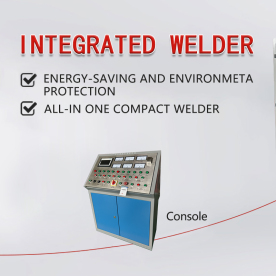
Complete Pipe mill production line solution: Everything you need to know
After the pipes are formed and welded, they need to be cut to the desired length. Cutting machines in a pipe mill production line are used to cut the pipes with precision and accuracy. There are different types of cutting machines available, such as flying cut-off machines, rotary cut-off machines, and cold saws, each suited for different pipe sizes and production speeds.
Once the pipes are cut to size, they undergo inspection to ensure they meet the required quality standards. Inspection systems in a pipe mill production line are used to detect defects, measure dimensions, and perform non-destructive testing on the pipes. By automating the inspection process, manufacturers can quickly identify and rectify any issues, ensuring that only high-quality pipes are shipped to customers.

Complete Pipe mill production line solution: Everything you need to know
Overall, a complete pipe mill production line solution offers manufacturers a comprehensive approach to pipe manufacturing, from raw material handling to final inspection. By investing in a complete production line solution, manufacturers can improve the efficiency of their pipe manufacturing process, reduce production costs, and deliver high-quality pipes to their customers on time.
In conclusion, a complete pipe mill production line solution is essential for manufacturers looking to stay competitive in the pipe manufacturing industry. By integrating various components such as pipe forming machines, welding equipment, cutting machines, and inspection systems, manufacturers can streamline their production process and produce high-quality pipes efficiently. With the right production line solution in place, manufacturers can meet the growing demand for pipes and maintain their reputation for excellence in the industry.Pipe making machine with welding function