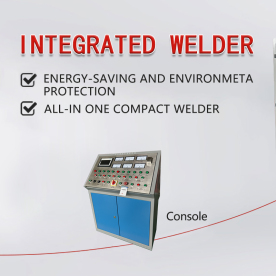
Unlocking Efficiency: The Importance of Custom-Made Spare Parts for Solid State HF Welders in Industrial Applications
In the world of industrial manufacturing, efficiency and precision are imperative. Among various tools and processes, solid state high-frequency (HF) welders play a crucial role, particularly in metal fabrication and joining technologies. These advanced machines allow manufacturers to achieve exceptionally strong and consistent welds. However, like any complex machinery, solid state HF welders require maintenance, and often the demand for custom-made spare parts arises to ensure ongoing performance and durability.
The Role of Solid State HF Welders
Solid state HF welders use high-frequency electromagnetic fields to create welds in metals, making them an ideal choice for applications that require precision and speed. Industries such as automotive, aerospace, and electronics rely heavily on these machines due to their ability to join a variety of materials without compromising material integrity. The solid state design also offers numerous advantages over traditional tube-type welders, including lower power consumption, improved thermal efficiency, and enhanced control over welding parameters.
The Need for Custom-Made Spare Parts
Even the most reliable solid state HF welders can experience wear and tear over time, which can impact efficiency and output quality. Standard interchangeable parts may not always fit the specific configuration or requirements of every machine. This is where the significance of custom-made spare parts comes into play.
1. Perfect Fit
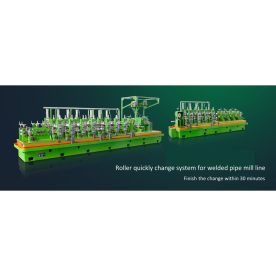
Unlocking Efficiency: The Importance of Custom-Made Spare Parts for Solid State HF Welders in Industrial Applications
Custom-made spare parts are designed to fit the specific model and design of a welder, ensuring optimal performance. Off-the-shelf components may not align perfectly with the established specifications of a machine, leading to discomforted operation and potential damage. Tailor-made parts ensure a snug fit, minimizing any risks associated with imprecise alignment.
2. Enhanced Durability
By opting for custom-made spare parts, manufacturers can choose materials and specifications that enhance their durability. For example, a part that typically wears down quickly in standard designs can be manufactured using specialized materials or coatings that extend its life. This level of customization allows for stronger components that can withstand the rigors of industrial applications.
3. Improved Performance
Bespoke parts can incorporate advanced technology or features that standard components do not offer, providing an immediate boost to machine performance. Enhanced heat resistance, improved conductivity, or specialized geometries can help maintain a higher quality of weld, translating to better products and reduced wastage.
4. Cost-Effectiveness
While the initial investment in custom-made spare parts may seem higher than generic alternatives, the long-term savings can be significant. Enhanced durability translates to fewer repairs and replacements over time, reducing downtime and maintenance costs. Additionally, improved performance can result in increased throughput, ensuring that production targets are met without costly interruptions.
Manufacturing Custom Spare Parts
The process of creating custom-made spare parts for solid state HF welders typically involves several key steps:
– **Consultation and Assessment**: Manufacturers assess the existing systems and pinpoint what parts require replacement or improvement. – **Design and Prototyping**: Utilizing CAD software, engineers create detailed designs tailored precisely to the specifications of the welder.

Unlocking Efficiency: The Importance of Custom-Made Spare Parts for Solid State HF Welders in Industrial Applications
– **Material Selection**: Custom manufacturing allows for the use of specialized materials that enhance performance and durability, as discussed earlier.
– **Production**: Advanced manufacturing techniques such as 3D printing, CNC machining, or additive manufacturing are employed to create the parts.
– **Testing and Quality Assurance**: Before deployment, parts undergo rigorous testing to ensure they meet quality standards and function as intended.
Conclusion
In the competitive landscape of industrial manufacturing, the reliability and efficiency of machinery such as solid state HF welders are critical for success. The role of custom-made spare parts cannot be overstated — they not only improve machine performance but also contribute to overall operational cost-effectiveness. By ensuring that spare parts are tailored to specific needs, manufacturers can optimize their machinery, keep production lines running smoothly, and ultimately deliver high-quality products. Investing in custom solutions may be the key to maintaining a competitive edge in today’s market.Precision Mould for Tube Mills