In today’s fast-paced manufacturing environment, companies are constantly seeking innovative solutions to improve efficiency, reduce costs, and enhance product quality. One of the most significant advancements in industrial heating technology has been the development of customized induction heating equipment. This method offers a wide range of benefits over traditional heating techniques, making it increasingly popular in various industrial applications. This article will delve into the advantages of customized induction heating equipment while highlighting its diverse uses across different sectors.
What is Induction Heating?
Induction heating is a process that uses electromagnetic fields to heat conductive materials. When an alternating current passes through a coil, it creates a magnetic field that induces electric currents (or eddy currents) within the metal object placed inside or near the coil. This induced current generates heat due to the electrical resistance of the material. The unique aspect of induction heating is that heat is generated directly within the material, leading to faster heating times and improved energy efficiency compared to conventional heating methods.
The Need for Customization
While standard induction heating equipment is suitable for many applications, industries often face unique challenges that require specialized solutions. Customization allows manufacturers to design equipment that meets specific requirements, including size, power output, temperature control, and safety features.
Customized induction heating equipment can be tailored for various applications, such as hardening, melting, soldering, brazing, and heat treatment of materials. Moreover, industries like automotive, aerospace, electronics, and metal fabrication can benefit substantially from these bespoke solutions.
Advantages of Customized Induction Heating Equipment
1. **Efficiency and Speed**: One of the primary benefits of customized induction heating equipment is its efficiency. The induction heating process minimizes heat loss, as it directly heats the workpiece rather than surrounding air or surfaces. Additionally, customized equipment can optimize heating times, allowing for quicker processing and increased production rates.
2. **Precision and Control**: Custom equipment can be designed with advanced controls that allow for precise temperature regulation. This capability is essential in applications such as heat treating, where specific temperature profiles are necessary to achieve desired material properties. As a result, manufacturers can ensure consistent quality and performance in their products.
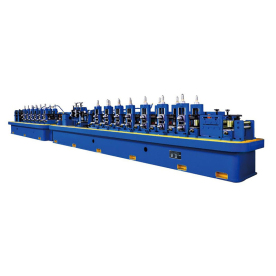
Exploring the Advantages and Applications of Customized Induction Heating Equipment in Modern Manufacturing and Industrial Processes
3. **Energy Savings**: Induction heating systems are known for their energy efficiency. Customized solutions can be tailored to operate at peak efficiency, reducing the overall energy consumption. This not only leads to cost savings for manufacturers but also contributes to environmental sustainability by lowering the carbon footprint associated with production processes.
4. **Reduced Material Damage**: The localized heating nature of induction heating allows for minimal thermal distortion and reduced damage to surrounding materials. When equipment is customized correctly, it can minimize the risk of heat-affected zones, preserving the integrity of the workpiece and reducing the need for subsequent repairs or rework.
5. **Enhanced Safety**: Customized induction heating equipment can incorporate safety features specific to the operational environment. Features such as protective enclosures, automated shutdowns, and monitoring systems can be integrated to enhance operator safety.
6. **Scalability**: As manufacturing capacities grow or shift, customizable induction heating systems can be adapted to meet changing demands. This scalability ensures that manufacturers can invest in equipment that will last for years, providing flexibility for future growth or adjustments in production.
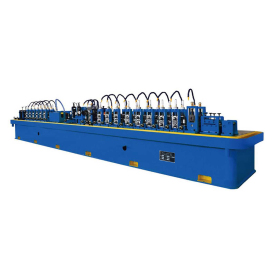
Exploring the Advantages and Applications of Customized Induction Heating Equipment in Modern Manufacturing and Industrial Processes
Applications in Various Industries
Customized induction heating equipment serves several critical applications across different industrial sectors:
– **Automotive Industry**: Used for hardening components like gears and crankshafts, induction heating ensures that automotive parts meet stringent durability and performance standards. – **Aerospace**: The aerospace sector relies on customized induction heating for processes like soldering and brazing of intricate components, ensuring high reliability and performance in demanding conditions. – **Electronics**: Induction heating plays a crucial role in manufacturing electronic components, where precision and control are paramount for sensitive materials.
– **Metal Fabrication**: From welding to metal treatment, customized solutions simplify and enhance metalworking processes, enabling manufacturers to craft intricate designs with precision.
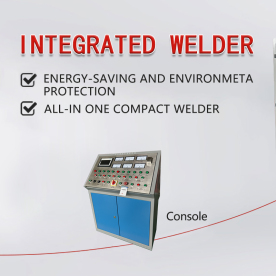
Exploring the Advantages and Applications of Customized Induction Heating Equipment in Modern Manufacturing and Industrial Processes
Conclusion
The introduction and development of customized induction heating equipment have revolutionized many aspects of modern manufacturing. By offering efficiency, precision, and adaptability, these tailored solutions help businesses streamline operations and improve product quality. As industries continue to evolve and require more specialized equipment, the role of customized induction heating will undoubtedly expand, driving innovation and competitiveness in the global market.Precision-Made Spare Parts for Cold Cutting Saws