****
Induction heating is becoming increasingly vital in various industrial processes, from metal fabrication to cooking technology. The efficiency and precision of this method have made it a preferred choice for numerous applications. However, off-the-shelf solutions may not always meet the unique requirements of specific industries. This is where customized induction heating equipment comes into play, providing tailored solutions that enhance productivity, optimize performance, and reduce costs.
Customized induction heating equipment refers to equipment specifically designed and engineered to meet the particular needs of a user or industry. Instead of relying on standard induction systems, which might not fully align with operational requirements, companies can work with manufacturers to develop solutions that meet their precision, size, and heating parameters.
Advantages of Customized Solutions
One of the primary benefits of customized induction heating equipment is its capacity to adapt to specific processes. For instance, in the automotive industry, induction heating can be used for hardening and tempering metal components. Each part may have different dimensional requirements, heating temperatures, and treatment times. A standard induction heating solution may not provide the necessary control over these variables, leading to inconsistencies in quality. However, a customized system can be engineered to deliver precise heating cycles that align perfectly with the specifications of each part.
Beyond precision, customized induction heating solutions offer enhanced efficiency. Manufacturers can optimize the size and power of their induction coils to match the specific requirements of their processes, reducing energy consumption and lowering operational costs. When induction heating systems are designed with specific applications in mind, they often can achieve faster heating times, reducing cycle times and improving overall productivity.
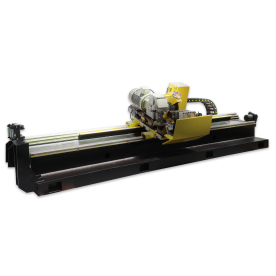
The Revolution of Customized Induction Heating Equipment: Tailoring Solutions for Diverse Industrial Applications
Moreover, customization allows for integration with existing production line systems and equipment. Many companies have standardized machinery and processes that would benefit from the integration of induction heating, but standard systems may not fit neatly into their operational framework. Customized solutions can be designed to integrate seamlessly, enhancing the overall functionality of production lines without necessitating significant changes or additional expenses.
Applications Across Industries
Customized induction heating equipment can be found in a variety of industries, each with unique requirements. In the manufacturing sector, for example, it is commonly used for applications such as forging, brazing, and soldering. Each of these processes has distinct requirements for heating and cooling rates, and customized solutions ensure that these parameters are met consistently.
In the field of medical device manufacturing, where precision and sterility are vital, customized induction heating systems can be developed to prepare metal implants while minimizing the risk of contamination. By controlling various factors, such as temperature and dwell time, manufacturers can ensure that instruments meet the necessary quality standards.
Another promising application is in the food processing industry. Customized induction heating equipment is being utilized for tasks such as pasteurization and cooking, where precision in temperature control is crucial for food safety and quality. The ability to design an induction heating system that ensures even heat distribution can drastically improve food processing efficiency.
Future Trends and Developments
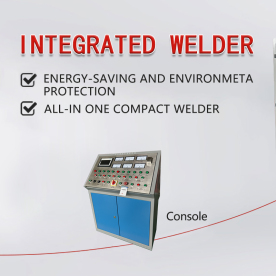
The Revolution of Customized Induction Heating Equipment: Tailoring Solutions for Diverse Industrial Applications

The Revolution of Customized Induction Heating Equipment: Tailoring Solutions for Diverse Industrial Applications
As technology evolves, so too will the capabilities of customized induction heating equipment. Advances in materials science and computer-aided design are enhancing the ability to create specialized systems that deliver even greater precision and efficiency. Furthermore, with the rise of Industry 4.0, there is also a significant focus on integrating smart technology into induction heating solutions. By incorporating IoT devices, artificial intelligence, and data analytics, future customized induction heating systems will likely provide real-time monitoring, predictive maintenance notifications, and enhanced process control, empowering industries to maximize productivity and minimize downtime.
In conclusion, customized induction heating equipment is revolutionizing the way industries approach heating processes. By tailoring solutions to meet specific needs, businesses can enhance precision, efficiency, and integration with existing systems, ultimately leading to better product quality and lower costs. As technology continues to evolve, so will the capabilities of these customized systems, solidifying their place as a cornerstone in modern industrial applications.High-efficiency pipe mill production line