****
In the ever-evolving world of manufacturing, particularly in the pipe production industry, customization has become a key differentiator in meeting diverse customer demands. Customized pipe mill production line solutions have emerged as a vital component of this industry, allowing manufacturers to enhance efficiency, reduce production costs, and ensure high-quality output. This article explores the significance of customized solutions, the benefits they provide, and the innovative approaches being adopted in the design and implementation of pipe mill production lines.
Understanding Customized Pipe Mill Production Lines
Pipe mill production lines are specialized systems designed for the manufacturing of pipes used in various applications, from construction to oil and gas. These lines encompass a series of machines and processes, including cutting, welding, forming, and finishing, tailored to produce pipes of different dimensions, materials, and specifications. Customized pipe mill production line solutions refer to the ability to adapt these lines to meet specific customer requirements, ensuring the final product matches exact standards and preferences.
The need for customization arises from the increasing diversity in pipe applications and materials. While some industries demand standard pipes for general uses, others require specialized products, such as pipes with unique coatings or structural properties. Customization enables manufacturers to cater to varying market demands, thereby enhancing their competitive advantage.
Benefits of Customized Pipe Mill Production Lines
1. **Increased Flexibility**: Customized production lines are built to handle multiple pipe sizes and types without significant downtime. This flexibility not only allows manufacturers to respond swiftly to changing market needs but also helps in optimizing production schedules.
2. **Enhanced Efficiency**: Tailoring the production line to specific products eliminates unnecessary steps and machinery, streamlining operations. This approach reduces production time and minimizes waste, leading to significant cost savings over time.
3. **Improved Product Quality**: Customized solutions enable precise control over the manufacturing process, resulting in higher quality pipes. By incorporating advanced technologies, such as automated monitoring and inspection systems, manufacturers can ensure that every pipe meets stringent quality standards.
4. **Lower Production Costs**: Although the initial investment in a customized pipe mill production line may be higher, the long-term cost benefits are substantial. Reduced waste, shorter production times, and decreased labor costs translate into overall savings, making customized lines a financially sound choice.
5. **Market Differentiation**: Offering a unique range of custom pipe products allows manufacturers to distinguish themselves from competitors. By meeting specific demands, companies can develop a loyal customer base and explore new market opportunities.
6. **Technological Advancements**: Customized pipe mill production lines often incorporate the latest technologies, such as automation, machine learning, and artificial intelligence. These advancements not only enhance production capabilities but also aid in predictive maintenance, reducing downtime and increasing operational efficiency.
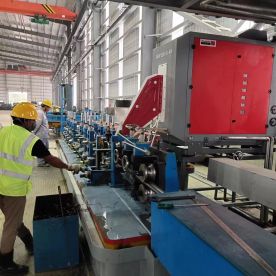
Innovative Customized Pipe Mill Production Line Solutions: Tailoring Processes to Enhance Efficiency and Product Quality in the Manufacturing Sector
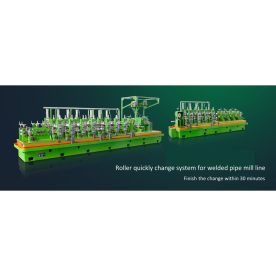
Innovative Customized Pipe Mill Production Line Solutions: Tailoring Processes to Enhance Efficiency and Product Quality in the Manufacturing Sector
Innovative Approaches in Designing Customized Solutions

Innovative Customized Pipe Mill Production Line Solutions: Tailoring Processes to Enhance Efficiency and Product Quality in the Manufacturing Sector
The design of customized pipe mill production lines involves a comprehensive analysis of customer needs and market trends. Manufacturers often engage in extensive consultations with clients to define the specifications, desired output, and production timelines. This collaborative approach results in better-aligned solutions that address real-world challenges.
1. **Flexible Machinery**: Investing in modular machinery that can be easily reconfigured for various pipe types is a fundamental aspect of customized production lines. Manufacturers are increasingly adopting solutions that allow for quick adjustments, minimizing setup times.
2. **Automation and Smart Manufacturing**: With the rise of Industry 4.0, the integration of automation into customized production lines has revolutionized the pipe manufacturing process. Automated systems enhance precision and reduce human error, while smart technology provides real-time data analytics for continuous improvement.
3. **Robust Quality Control Systems**: To ensure the highest standards, customized pipe mill production lines often include integrated quality control measures. This may involve non-destructive testing methods and real-time inspection technologies that monitor the products throughout the manufacturing process.
4. **Sustainable Practices**: Modern pipe manufacturers are increasingly focusing on sustainability. Customized production lines can be designed to optimize resource usage, reduce energy consumption, and incorporate recycled materials, aligning with environmental standards and customer expectations.
Conclusion
Customized pipe mill production line solutions are no longer just an option; they have become a necessity in the competitive landscape of pipe manufacturing. By focusing on adaptability, efficiency, and quality, manufacturers can not only meet customer demands but also pave the way for future growth and innovation. Embracing this tailored approach not only enhances operational capabilities but also ensures that manufacturers remain at the forefront of their industry, ready to tackle the challenges of tomorrow.Durable All-in-one High Frequency Welder