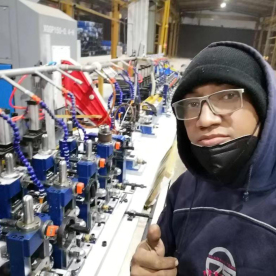
Enhancing Efficiency and Longevity in Tube Manufacturing: The Role of Durable Mould for Tube Mills
In today’s competitive manufacturing landscape, tube mills play a crucial role in the production of pipes and tubes used in a myriad of applications, from construction to automotive engineering. As industries evolve and demand increases, manufacturers are continuously seeking ways to enhance production efficiency, reduce waste, and improve product quality. One pivotal component that can significantly impact these factors is the use of durable mould for tube mills. This article delves into the importance of durable mould designs, their benefits, and their influence on the overall performance of tube mills.
**Understanding the Role of Moulds in Tube Manufacturing**
Moulds are essential in the tube manufacturing process, as they shape and form the metal or plastic into the desired pipe or tube specifications. In tube mills, flavoured by the continuous rolling of material, moulds facilitate the precise shaping of round or square tubes, ensuring uniformity and adherence to design specifications. The quality and durability of these moulds directly correlate with the quality of the final product, making it imperative for manufacturers to invest in high-quality, durable moulds.
**The Importance of Durability**
The demand for pipes and tubes is ever-increasing, which puts significant pressure on tube mills to deliver products faster while maintaining high quality. Durable moulds not only withstand the rigors of the moulding process but also reduce the frequency of replacements and maintenance. With traditional moulds, wear and tear can lead to inconsistencies in the final product and interruptions in the manufacturing process. Durable moulds, designed with robust materials and innovative engineering, can resist high-pressure conditions, increased abrasion, and thermal stresses. This longevity translates into lower operational costs and more consistent product quality.
**Benefits of Using Durable Mould for Tube Mills**
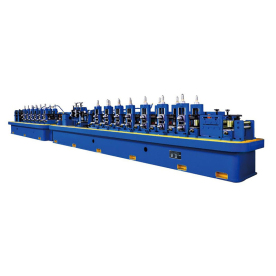
Enhancing Efficiency and Longevity in Tube Manufacturing: The Role of Durable Mould for Tube Mills
1. **Cost-effectiveness**: Investing in durable moulds may require a higher initial expenditure, but the long-term savings are substantial. With reduced wear and longer lifespans, manufacturers can avoid frequent replacements and minimize downtime associated with maintenance or repairs.
2. **Improved Production Speeds**: Durable moulds ensure smoother operations and less friction during the shaping process. This can enable tube mills to run at higher speeds, increasing the overall production output without compromising quality.
3. **Consistency in Quality**: The precision offered by high-quality, durable moulds ensures that each piece produced meets stringent specifications. Variability can lead to defects that might require reworking or scrapping, which not only wastes materials but also affects delivery schedules.
4. **Enhanced Performance**: Durable moulds can maintain their shape and integrity over extended periods, which translates into better performance overall. They can cope with the dynamic demands of modern manufacturing, ensuring that producers meet their client’s specifications without fail.
5. **Environmental Impact**: By reducing the frequency of mould replacement and the waste associated with defective production, manufacturers can lessen their environmental footprint. Durable moulds contribute to sustainability by ensuring that the resources utilized in the production process are maximized.

Enhancing Efficiency and Longevity in Tube Manufacturing: The Role of Durable Mould for Tube Mills
**Technological Innovations in Mould Design**
The advancement in materials science has led to the development of moulds that are not only durable but also capable of withstanding extreme conditions. Companies are now utilizing advanced alloys and composite materials that offer enhanced resistance to wear and corrosion. Additionally, innovations like coatings that reduce friction and improve heat dissipation further extend the life of moulds used in tube mills. Manufacturers are increasingly turning to computer-aided design (CAD) and simulation technologies to optimize mould geometry, ensuring maximum efficiency during production runs.
**Conclusion**
As tube mill manufacturers navigate an increasingly demanding market, the investment in durable mould technology is a critical step towards ensuring productivity and product quality. The multifaceted benefits of durable mould for tube mills—cost savings, increased production speeds, consistency, and reduced environmental impact—make it an essential component of modern manufacturing. Companies that embrace these advancements stand to gain a competitive edge and reaffirm their commitment to delivering high-quality products to their customers. In an era defined by innovation, durability, and efficiency, the mould may very well be the unsung hero of the tube manufacturing industry.Automatic induction heating equipment