In the competitive landscape of modern manufacturing, the importance of efficiency, precision, and durability has never been more critical. Among various production techniques, tube mills stand out for their ability to create high-quality metal tubes for a wide range of applications. Integral to the effectiveness of these mills is the role played by durable moulds, which are essential for ensuring the longevity and reliability of the manufacturing process. This article delves into the features, benefits, and considerations surrounding the use of durable mould for tube mills.
Understanding Tube Mills
Tube mills are specialized machines that form metal sheets into tubular shapes. These machines can process various materials, including steel, aluminum, and copper, and are widely used to produce everything from pipes to automotive components. The design and functioning of tube mills rely heavily on the use of specific moulds that provide the necessary shape and contour to the tubes produced.
What is Durable Mould for Tube Mills?
Durable moulds are precision-engineered tools designed to withstand the high-stress environments typical of tube manufacturing. They are made from high-quality materials that are resistant to wear, corrosion, and thermal expansion. The durability of these moulds is paramount, as they significantly influence the production process’s overall efficiency and output quality.
These moulds must maintain their shape and functionality despite the extreme mechanical and thermal forces they encounter during operation. The design specifics of a durable mould can vary based on the type of tube being produced, the materials used, and the operational environment of the tube mill.
Features of Durable Moulds
1. **Material Composition**: Durable moulds are typically made from high-strength alloys or metals capable of withstanding high temperatures and pressures. Advanced materials such as tool steels, carbides, or even composites are often used for their enhanced properties.
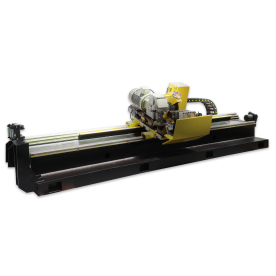
Exploring the Advantages and Features of Durable Mould for Tube Mills in Modern Manufacturing Processes
2. **Precision Engineering**: The moulds used in tube mills are often produced using advanced manufacturing techniques such as CNC machining. This ensures that every mould is both accurate and consistent, which is vital for maintaining uniformity in the production process.
3. **Thermal Resistance**: Tube milling processes can generate substantial heat. Durable moulds are engineered to resist thermal deformation, ensuring they retain their shape and function under elevated temperatures.
4. **Corrosion Resistance**: Many manufacturing environments expose moulds to corrosive substances. Choosing the right coating or substrate material can protect durable moulds from chemical wear.
5. **Complex Designs**: Advances in mould design allow for the creation of complex geometries that meet specific production needs. These intricate designs can enhance the efficiency of the welding and shaping processes in tube mills.
Benefits of Using Durable Moulds
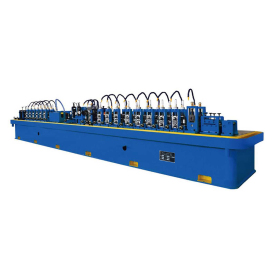
Exploring the Advantages and Features of Durable Mould for Tube Mills in Modern Manufacturing Processes
1. **Enhanced Longevity**: The primary advantage of investing in durable moulds is their increased lifespan. This reduces the frequency of replacements and maintenance, leading to cost savings in the long run.
2. **Improved Quality**: Durable moulds ensure that products feature uniform dimensions and finishes, which is crucial for applications requiring high precision and reliability.
3. **Higher Production Efficiency**: With reduced wear and tear, durable moulds contribute to fewer machine downtimes. This leads to an overall increase in the production rates of the tube mills.
4. **Cost Effectiveness**: Although the initial investment in durable moulds may be higher than traditional options, the long-term benefits, including reduced maintenance costs and improved production efficiency, make them a cost-effective choice.
5. **Sustainability**: Durable moulds contribute to a more sustainable manufacturing process by minimizing waste and the necessity for material replacements, thus lowering the environmental impact.
Conclusion
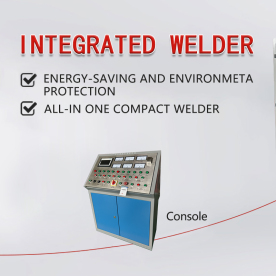
Exploring the Advantages and Features of Durable Mould for Tube Mills in Modern Manufacturing Processes
The role of durable moulds in tube mills cannot be overstated. As industries continue to evolve and place higher demands on manufacturing processes, the need for reliable and efficient production methods becomes increasingly critical. With their advanced materials, precision engineering, and numerous advantages, durable moulds have become essential components in ensuring that tube mills produce high-quality products efficiently and sustainably. Investing in these moulds is a strategic move that can yield substantial dividends, both in operational excellence and economic performance. For manufacturers looking to enhance their tube production capabilities, embracing durable mould technology is a step toward future-proofing their operations.All-in-one solid state HF Equipment