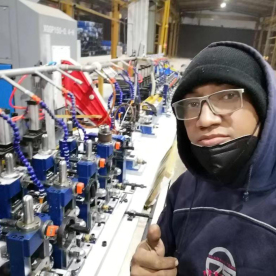
Exploring the Benefits and Innovations of Durable Mould for Tube Mills: How Advanced Materials Revolutionize Production Efficiency and Quality
In today’s industrial landscape, the demand for high-quality steel tubes continues to grow, leading to an increased focus on the capabilities and performance of tube mills. As manufacturers seek ways to enhance productivity and maintain quality, the development of durable mould for tube mills has become a critical area of innovation. This article explores the impact of durable moulds on tube manufacturing processes, highlighting the materials, technologies, and benefits associated with this essential component.
The foundational purpose of a mould in tube mills is to shape and form the metal into precise profiles. Traditionally, moulds were crafted from less durable materials, which contributed to frequent wear, reduced operational efficiency, and increased downtime due to maintenance or replacement needs. However, advancements in materials science have led to the introduction of durable moulds designed to withstand the demanding conditions of tube production, thereby extending the lifespan of these critical tools.
One of the key drivers of the shift towards durable moulds in tube mills is the development of advanced alloys and composite materials. These innovative substances can resist extreme conditions, including high temperatures and corrosive environments, which are common in metal forming processes. The primary focus is on reducing wear and tear during the continuous processing of metal, ultimately resulting in higher production rates and lower costs associated with maintenance and repair.
Moreover, the improved thermal stability and durability of advanced mould materials facilitate better heat dissipation during production. Excessive heat can cause deformation in the mould, negatively impacting the shape and quality of the finished product. Durable moulds that effectively manage heat minimize this risk and ensure consistent edge sharpness, contributing to superior dimensional accuracy and surface finish of the tubes produced.
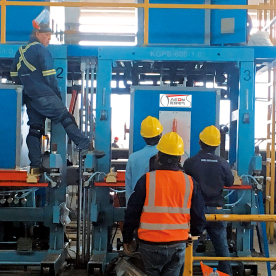
Exploring the Benefits and Innovations of Durable Mould for Tube Mills: How Advanced Materials Revolutionize Production Efficiency and Quality
In addition to material advancements, innovations in manufacturing processes for durable moulds have also played a significant role in advancements in tube mill technology. For instance, modern machining techniques, such as Computer Numerical Control (CNC) machining and additive manufacturing, allow for the creation of complex mould designs with high precision and efficiency. This level of customization leads to enhanced performance, tailored to specific production requirements.
The benefits of implementing durable moulds in tube mills extend beyond operational performance; they also have a positive impact on overall cost management. With improved durability, manufacturers can achieve longer production runs without the need for mould replacements, significantly reducing downtime and the costs associated with both maintenance and lost production time. Moreover, the enhanced quality of the end product can lead to decreased waste and increased customer satisfaction, providing a competitive edge in a saturated market.
Another important aspect of durable moulds is the environmental impact. By improving the longevity of moulds, manufacturers can reduce the frequency of production waste associated with replacing worn-out tools. This approach not only leads to cost savings but also aligns with sustainable manufacturing practices, as fewer materials are consumed over time.
Corrosion and scaling are significant challenges in tube mills due to the nature of the materials processed. Durable moulds are engineered to resist these phenomena, extending their operational life and ensuring consistent performance. Specialized coatings and treatments can be applied to mould surfaces to enhance their resistance to corrosion and damage, providing an added layer of protection.
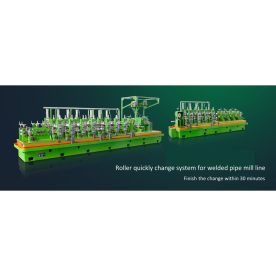
Exploring the Benefits and Innovations of Durable Mould for Tube Mills: How Advanced Materials Revolutionize Production Efficiency and Quality
Furthermore, the trend towards automation and Industry 4.0 technologies in manufacturing emphasizes the need for high-performance moulds that can integrate seamlessly with advanced production systems. Smart manufacturing requires the ability to monitor, adapt, and optimize production processes in real time, and durable moulds provide the reliability and performance necessary to achieve these objectives.
In conclusion, the adoption of durable mould for tube mills represents a significant advancement in industrial manufacturing processes. By leveraging advanced materials and manufacturing techniques, manufacturers can enhance productivity, improve product quality, and achieve greater sustainability. As the demand for high-quality tube products continues to rise, investing in durable mould technology will be crucial for companies looking to maintain a competitive edge in the evolving global marketplace. Embracing these innovations is not merely a choice; it is a strategic necessity for success in the future of tube manufacturing.Original Spare Parts for Annealing Machines