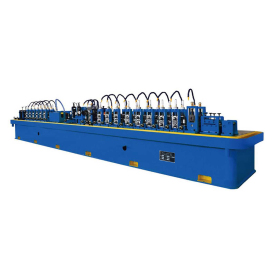
Revolutionizing Metalworking: The Impact of Energy-Saving and Environmental-Friendly All-in-One Welders on the Industry
****
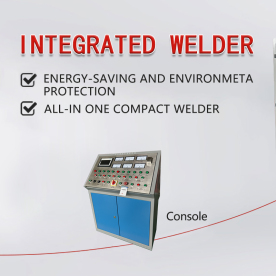
Revolutionizing Metalworking: The Impact of Energy-Saving and Environmental-Friendly All-in-One Welders on the Industry
In recent years, the metalworking industry has witnessed a remarkable shift towards more sustainable practices. One of the most significant advancements leading this change is the development of energy-saving and environmental-friendly all-in-one welders. These innovative machines not only help reduce energy consumption but also minimize the environmental impact of welding operations. This article explores the features, benefits, and the wider implications of integrating energy-saving and environmentally-conscious technologies into welding processes.
Understanding All-in-One Welders
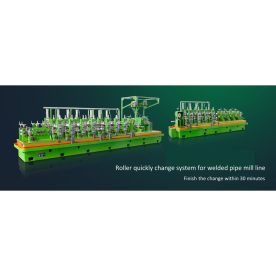
Revolutionizing Metalworking: The Impact of Energy-Saving and Environmental-Friendly All-in-One Welders on the Industry
All-in-one welders are multifunctional machines designed to perform various welding processes, including MIG, TIG, and stick welding, all within a single unit. While traditional welding setups typically require multiple machines for different types of welding, all-in-one welders streamline the process, making them more efficient and user-friendly. The advent of energy-saving technology in these machines represents a crucial step towards greener manufacturing practices.
Key Features of Energy-Saving Welders
1. **Advanced Inverter Technology**: Many energy-saving welders utilize inverter technology, which converts the standard electrical supply into a higher frequency electrical signal. This not only enhances the efficiency of the welding process but also significantly reduces energy consumption compared to older transformer-based machines.
2. **Adaptive Current Control**: These welders often come equipped with intelligent features that allow them to adjust the output power based on the type of material and thickness being worked on. This means that energy is only used as needed, preventing unnecessary wastage.
3. **Integrated Cooling Systems**: Energy-efficient cooling systems help maintain the optimal operating temperature of the welder, preventing overheating and extending the machine’s lifespan. This reduces both energy expenditure and maintenance costs over time.
4. **User-Friendly Interfaces**: Many modern all-in-one welders feature intuitive control panels that allow users to select the type of welding and material effortlessly. This simplicity reduces the time spent on setup and operation, which translates to increased productivity and lower energy use.
Environmental Benefits
The environmental impact of traditional welding processes is considerable, primarily due to high energy consumption and the release of harmful gases and particulates. Energy-saving and environmental-friendly all-in-one welders contribute to reducing this impact in several ways:
1. **Lower Carbon Footprint**: By consuming less energy and utilizing cleaner technology, these welders help decrease the overall carbon emissions associated with welding activities. This is crucial in efforts to combat climate change.
2. **Reduced Waste Generation**: Efficient welding processes result in less scrap material and waste production. With precise control over the welding parameters, operators can achieve better-quality welds, which minimizes the need for rework and reduces waste.
3. **Sustainability Features**: Many energy-efficient welders are constructed from recyclable materials and designed with lifespan considerations in mind. This approach not only promotes sustainability but also signals a commitment to environmental responsibility from manufacturers.
4. **Fume Extraction Systems**: Some models come with built-in fume extraction capabilities, which help filter and remove harmful smoke and gases from the welding environment. This contributes to a healthier workplace for operators and reduces pollution.
The Future of Welding
As industries continue to prioritize sustainability, the demand for energy-saving and environmentally-friendly welding solutions is likely to grow. The integration of advanced technology into welding equipment not only meets regulatory standards but also aligns with the global shift towards more responsible business practices.
Moreover, the rise of automation and smart technologies offers exciting possibilities for the future of welding. The combination of energy-efficient welders with automation can further optimize processes, enhancing productivity while ensuring environmental considerations remain at the forefront.
Conclusion
Energy-saving and environmental-friendly all-in-one welders represent a significant leap forward in the welding industry. By incorporating advanced technology and sustainable practices, these machines are not just tools for metalworking; they are catalysts for change within the manufacturing landscape. Their widespread adoption will be essential as industries strive to meet energy efficiency goals and adhere to stricter environmental regulations. As we look ahead, it becomes clear that investing in such technologies is not only beneficial for businesses but also imperative for the health of our planet.Solid state HF welder with temperature control