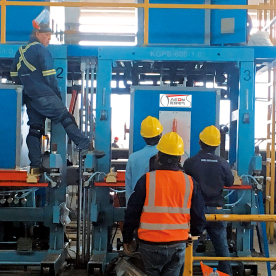
Revolutionizing Pipe Production: Exploring the Advantages of High-Efficiency ERW Tube Mill Technology for Modern Manufacturing Needs
In today’s fast-paced manufacturing environment, the demand for high-quality steel tubes is at an all-time high. As industries such as construction, automotive, and oil and gas expand, the need for advanced manufacturing technologies has become paramount. Among these technologies, the High-efficiency Electric Resistance Welding (ERW) tube mill stands out as a transformative solution that enhances production capabilities, reduces costs, and increases the quality of steel tubes.
High-efficiency ERW tube mills utilize a process where sheets of metal are rolled and then welded together using an electrical resistance method. This technique allows for the quick and efficient production of tubular products that can be used in a variety of applications, from structural frameworks to fluid transportation systems. The key advantage of high-efficiency models is their ability to streamline the production cycle, minimizing waste while maximizing output—a necessity in a competitive market.
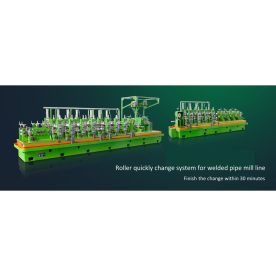
Revolutionizing Pipe Production: Exploring the Advantages of High-Efficiency ERW Tube Mill Technology for Modern Manufacturing Needs
One of the central benefits of high-efficiency ERW tube mills is their rapid operational speed. Traditional manufacturing methods often involve lengthy processing times, which can lead to increased costs and delivery delays. High-efficiency ERW systems are designed to operate at higher speeds without compromising on quality. This efficiency enables manufacturers to meet tight deadlines and customer demands while maintaining the superior quality of the products. As a result, businesses can enhance their production capacity and cater to larger orders without the need for extensive capital investment in new production lines.

Revolutionizing Pipe Production: Exploring the Advantages of High-Efficiency ERW Tube Mill Technology for Modern Manufacturing Needs
Moreover, the consistency and quality of the tubes produced by high-efficiency ERW tube mills are markedly superior to those manufactured via traditional methods. The welding process employed in these mills ensures a uniform weld seam, which translates into improved tensile strength and durability of the finished product. This is particularly crucial in industries where structural integrity is paramount, such as construction and heavy machinery. As customers place a premium on quality, high-efficiency ERW tube mills allow manufacturers to deliver products that not only meet but exceed industry standards.
Another notable feature of high-efficiency ERW tube mills is their adaptability. Modern versions of these mills can process a wide range of materials, including different grades of steel and various sized tubes. This adaptability makes them suitable for diverse applications, from small-scale projects to large-scale industrial applications. Furthermore, many high-efficiency models include advanced automation and control technologies that enable manufacturers to quickly adjust their operations according to specific production needs, thereby reducing downtime and boosting overall efficiency.
Sustainability in manufacturing is another significant aspect where high-efficiency ERW tube mills shine. With increasing regulations and consumer demand for eco-friendly practices, manufacturers are seeking ways to reduce their carbon footprint. High-efficiency tube mills consume less energy per unit produced compared to traditional methods, resulting in lower operational costs and reduced environmental impact. The technology employed in these mills often also includes recycling systems that allow for the reuse of scrap metal, contributing to more sustainable production processes.
The implementation of high-efficiency ERW tube mills involves not only technological advancements but also a shift in workforce training and operational strategies. Employees must be skilled in operating these sophisticated machines and in understanding the principles of modern manufacturing processes. Companies that invest in training and development can reap the benefits of high efficiency and quality, as knowledgeable workers are better equipped to handle the complexities of advanced manufacturing technologies.
In conclusion, high-efficiency ERW tube mills represent a significant leap forward in the production of steel tubes, addressing the urgent needs of various industries with speed, precision, and sustainability. As manufacturing continues to evolve, embracing such advanced technologies will be key to maintaining competitiveness and meeting global demands. Companies utilizing these high-efficiency solutions will not only enhance their productivity but also position themselves as leaders in innovation and quality in the manufacturing landscape. The future of tube production lies in the integration of these advanced technologies, setting a new standard for excellence in the industry.Precision-Crafted Spare Parts for Annealing Machines