High frequency welding, also known as high frequency induction welding or radio frequency welding, is a modern technique that has revolutionized the way metal parts are joined together in various industries. Its efficiency, precision, and versatility make it an ideal choice for manufacturers looking to enhance production and improve the quality of their products. This article delves into the benefits, applications, and advancements of high frequency welders used for metal fabrication and assembly.
Understanding High Frequency Welding
High frequency welding operates on the principle of electromagnetic induction, where high-frequency alternating current is passed through copper coils to generate a magnetic field. This magnetic field induces heat in the metal parts being welded, causing them to reach their melting point quickly and bond together seamlessly. The process stands out for its capability to produce strong, durable welds without the need for additional filler materials or extensive pre-heating.
Benefits of High Frequency Welders for Metal
1. **Speed and Efficiency**: One of the most significant advantages of high frequency welding is its speed. The process can be completed in mere seconds, enabling manufacturers to increase their output significantly compared to traditional welding methods. This high throughput is essential in today’s fast-paced production environments.
2. **Precision and Control**: High frequency welders offer superior control over heating and cooling rates, which results in high-quality welds with minimal distortion. This precision is critical, especially in industries where tolerances are tight, such as aerospace or automotive manufacturing.
3. **Energy Efficiency**: The high speed of the process not only enhances productivity but also contributes to energy savings. High frequency welding requires less power than other welding techniques over the same period, making it a cost-effective option for large-scale production runs.
4. **Versatility**: High frequency welders are compatible with a wide range of materials, including various metals such as steel, copper, aluminum, and some flexible materials like plastics. This versatility allows manufacturers to use the same equipment for different projects, streamlining their operations.
5. **Minimal Distortion**: Because high frequency welding uses localized heating, the weld zone experiences minimal thermal expansion and contraction. This characteristic reduces the risk of warping or distortion, ensuring that parts maintain their intended shape and dimensions.
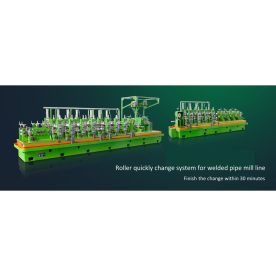
Exploring the Benefits and Applications of High Frequency Welder for Metal in Modern Manufacturing Processes
6. **Reduced Weld Defects**: The rapid heating and cooling cycles inherent in high frequency welding help reduce common weld defects such as porosity, inclusions, and cracks, leading to stronger and more reliable joints.

Exploring the Benefits and Applications of High Frequency Welder for Metal in Modern Manufacturing Processes
Applications of High Frequency Welding
High frequency welders are widely used across various sectors, including:
– **Automotive Industry**: In manufacturing automotive components, high frequency welding is used for joining lightweight metals and creating robust structural parts. This technology supports the growing trend toward lightweight vehicle designs that improve fuel efficiency.
– **Aerospace Sector**: The aerospace industry prioritizes strong yet lightweight materials. High frequency welding is employed to create fuselage sections and other critical components that must meet stringent performance and safety standards.
– **Manufacturing of Pipes and Tubing**: High frequency welders are particularly effective in the production of pipes and tubes, especially in the oil and gas industry. They are used to produce high-strength, leak-proof joints that can withstand harsh conditions.
– **Electrical Equipment and Electronics**: High frequency welding finds applications in the manufacturing of transformers and capacitors, where precise and reliable connections are essential.

Exploring the Benefits and Applications of High Frequency Welder for Metal in Modern Manufacturing Processes
– **Textile and Plastic Products**: In addition to metals, high frequency welders are also used for welding thermoplastics, creating durable seams in various textile applications.
Advances in High Frequency Welding Technology
As with any manufacturing technology, high frequency welders are continually evolving. Recent advancements have focused on enhancing automation, integration with smart manufacturing systems, and improving user interfaces. The introduction of specialized software can now monitor weld quality in real-time, collecting data that can be used for process optimization.
In conclusion, high frequency welders for metal are transforming how industries approach metal joining processes. Their speed, precision, and versatility make them an invaluable asset in modern manufacturing. As technology continues to advance, the capabilities and applications of high frequency welding will undoubtedly expand, driving further efficiencies and innovations in production. This technology will play a crucial role in shaping the future of manufacturing across various sectors.Industrial-Grade HSS Blade