High frequency welding for plastic, often referred to as HF welding, is a transformative technique that has gained prominence in various industries over the years. This advanced welding method employs high-frequency electromagnetic energy, enabling manufacturers to join plastic materials with precision, strength, and efficiency. In this article, we delve into the fundamental principles of high frequency welding, its diverse applications, and the advantages it brings to modern manufacturing.
What is High Frequency Welding?
High frequency welding is a process that utilizes electromagnetic energy, typically in the radio frequency range (usually between 27.12 MHz to 40.68 MHz), to heat and fuse thermoplastic materials together. The process begins by placing the plastic components between two electrodes. When high-frequency voltage is applied, the electromagnetic waves generate heat within the plastic material, causing it to reach its melting point. Once the materials are sufficiently heated, they are pressed together, forming a strong and durable bond as they cool.
Principles of Operation
The key element in high frequency welding for plastic is its ability to directly heat the plastic material through dielectric heating. This differs from traditional welding methods such as ultrasonic welding or hot plate welding, where external heat sources are involved. The dielectric properties of the thermoplastic generate heat internally, allowing for rapid processing times and uniform heating throughout the weld area.
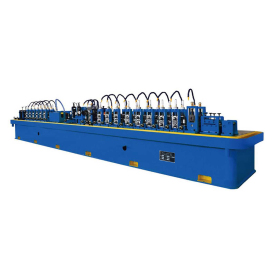
Understanding High Frequency Welding for Plastic: Innovative Techniques, Applications, and Benefits in Modern Manufacturing
One of the notable aspects of this welding technique is its ability to handle a variety of plastic components, including PVC, PET, and polyurethane. Moreover, HF welding is especially effective for thin-walled plastics, which are often challenging to weld using alternative methods due to the risk of overheating or warping.
Applications of High Frequency Welding
High frequency welding for plastic finds extensive applications across numerous industries, including:
1. **Automotive**: In the automotive sector, HF welding is employed to assemble various components such as dashboards, interior panels, and air ducts. The ability to create strong, seamless joints enhances the durability and aesthetic quality of automotive parts.
2. **Medical Devices**: The medical industry relies heavily on high frequency welding for producing devices like IV bags, sterile packaging, and other medical supplies. The process is essential in ensuring that these products maintain the highest standards of cleanliness and integrity.
3. **Textiles**: HF welding has revolutionized the production of technical textiles used in outdoor gear, inflatable products, and protective clothing. It allows manufacturers to form seams that are both strong and waterproof, making them ideal for outdoor and industrial applications.
4. **Packaging**: High frequency welding plays a vital role in the manufacturing of plastic packaging, such as blister packs and custom containers. The quick and reliable bonding process ensures product integrity and enhances shelf life.
5. **Consumer Goods**: From electronic housings to household products, HF welding is used in creating a wide array of consumer goods. This versatility is crucial in meeting the diverse demands of the consumer market.
Advantages of High Frequency Welding
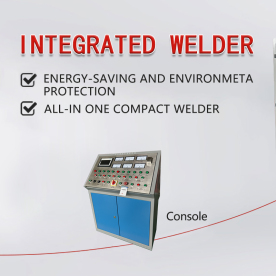
Understanding High Frequency Welding for Plastic: Innovative Techniques, Applications, and Benefits in Modern Manufacturing
The adoption of high frequency welding for plastic comes with several distinct advantages:
– **Speed**: The process is incredibly fast, often completing welds in a matter of seconds. This efficiency significantly enhances production rates and can lead to lower labor costs.
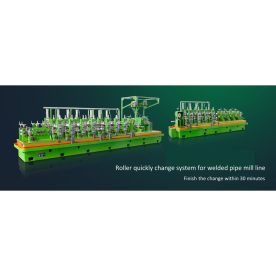
Understanding High Frequency Welding for Plastic: Innovative Techniques, Applications, and Benefits in Modern Manufacturing
– **Precision**: High frequency welding allows for precise control over weld parameters, resulting in consistent and repeatable welds. This precision is especially beneficial in industries where quality and performance are paramount.
– **Quality**: The internal heating method reduces the risk of surface damage typically associated with other welding techniques. This ensures that the aesthetic and functional properties of the material are preserved.
– **Environmentally Friendly**: The process generates minimal waste, as it does not require additional adhesives or solvents. Moreover, many thermoplastics can be recycled, contributing to sustainable manufacturing practices.
– **Versatility**: High frequency welding can accommodate a wide range of material thicknesses and shapes, making it suitable for various applications.
Conclusion
High frequency welding for plastic is a cutting-edge technology that enhances the efficiency and quality of plastic manufacturing. Its principles of operation, diverse applications, and numerous advantages make it a preferred choice for industries seeking reliable and durable bonding solutions. As technology continues to evolve, the significance of high frequency welding is likely to grow, paving the way for more innovations in plastic joining methods and applications. Whether in automotive, medical, textiles, or consumer goods, the impact of this welding technique will undoubtedly shape the future of manufacturing.Heavy-Duty Cold Cutting Saw Machine