In the fast-evolving landscape of modern manufacturing, the need for high-quality components has become critical across various sectors. Among these components, tubes play a significant role, particularly in industries such as automotive, aerospace, construction, and medical equipment. The introduction of high-precision tube making machines has revolutionized the production process, allowing manufacturers to meet stringent quality standards while enhancing efficiency and reducing waste. This article explores the significance of high-precision tube making machines, their operational features, benefits, and their impact on the manufacturing industry as a whole.
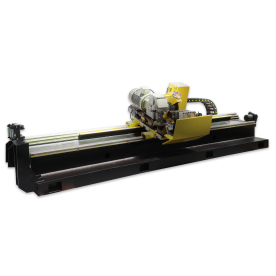
Revolutionizing Manufacturing: The Role of High-Precision Tube Making Machines in Modern Industry
High-precision tube making machines are engineered to produce tubes with exceptional accuracy, ensuring that dimensions are tightly controlled. These machines are capable of processing various materials such as stainless steel, aluminum, and plastics, making them versatile for different applications. The precision offered by these machines is crucial for industries where even minute deviations can lead to catastrophic failures. For example, in the aerospace industry, high-precision tubes are essential in fuel lines and hydraulic systems, where reliability and safety are paramount.
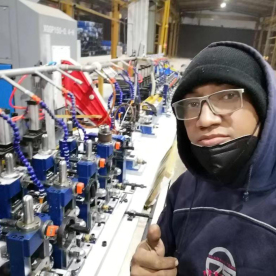
Revolutionizing Manufacturing: The Role of High-Precision Tube Making Machines in Modern Industry
One of the key features of these machines is their sophisticated technology, which often includes computer numerical control (CNC). CNC technology allows for automated adjustments and precise movements, enabling the machine to create complex tube shapes and custom specifications with minimal human intervention. This automation not only enhances precision but also significantly speeds up the production process, reducing lead times and allowing companies to respond quickly to market demands.
Additionally, high-precision tube making machines incorporate advanced materials handling systems that facilitate the efficient loading and unloading of raw materials and finished products. These systems are designed to minimize the risk of damages during handling, ensuring that the integrity of the tubes remains uncompromised throughout the production cycle. Moreover, the machines often include integrated quality control systems that monitor the production process in real-time, identifying any deviations from set parameters and triggering corrective actions immediately. This level of oversight not only assures quality but also reduces the occurrence of defects, saving manufacturers time and resources.
The benefits of utilizing high-precision tube making machines go beyond just quality and efficiency. These machines contribute to sustainability efforts by minimizing waste materials typically generated during the manufacturing process. Traditional tube-making methods often lead to significant scrap rates; however, with the precision and control offered by modern machines, manufacturers can optimize material usage, resulting in cost savings and reduced environmental impact.
Moreover, the adoption of high-precision tube making technology can lead to enhanced competitiveness within the industry. Manufacturers equipped with advanced machines can produce higher volumes of quality products at lower costs, positioning themselves more favorably in the marketplace. This advantage is especially crucial in industries characterized by fierce competition and fluctuating demand.
In addition to benefiting manufacturers, high-precision tube making machines also provide advantages to end-users. Industries that rely on these components benefit from improved reliability, which translates to longer lifespans and decreased maintenance costs. This reliability is vital in sectors like healthcare, where precision-engineered tubes can mean the difference between life and death.
However, the implementation of high-precision tube making machines does not come without challenges. The initial investment cost for these advanced machines can be significant, which may pose barriers for smaller manufacturers. Additionally, training staff to operate and maintain such sophisticated equipment requires investment in human capital. Despite these challenges, the long-term benefits of increased efficiency, reduced costs, and higher-quality products make high-precision tube making machines an attractive option for many businesses.
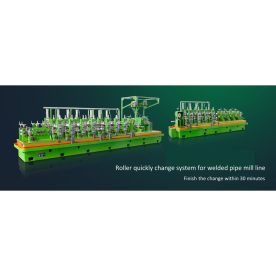
Revolutionizing Manufacturing: The Role of High-Precision Tube Making Machines in Modern Industry
In conclusion, high-precision tube making machines represent a significant advancement in manufacturing technology, offering a range of benefits that enhance productivity, quality, and sustainability. As industries continue to evolve and demand more reliable components, the adoption of these machines is likely to grow, shaping the future of tube production and manufacturing at large. Embracing such technology is essential for manufacturers aiming to stay ahead in a competitive landscape while ensuring they meet the increasing standards for quality and efficiency.Energy-efficient Pipe mill production line