In today’s fast-paced manufacturing environment, precision is paramount. The quest for accurate and efficient cutting solutions has led to the evolution of various machining technologies. Among these, the High-Speed Cold Cutting Saw Machine stands out as a game changer in the engineering and manufacturing sector. This innovative tool not only enhances productivity but also ensures top-notch precision, drastically reducing errors and material waste during the cutting process.
The High-Speed Cold Cutting Saw Machine operates on a fundamental principle: utilizing circular saw blades made of high-speed steel to achieve rapid and clean cuts without the hassle of overheating common in traditional cutting methods. This feature is particularly important as it preserves the integrity of the material being worked on, maintaining its structural properties. Unlike conventional sawing techniques that generate excessive heat due to friction, the cold cutting process does away with this issue, ensuring that the finished product’s quality is uncompromised.
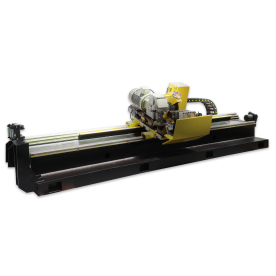
Revolutionizing Industrial Cutting: The Advantages of the High-Speed Cold Cutting Saw Machine for Precision Engineering
One of the primary benefits of implementing a High-Speed Cold Cutting Saw Machine in industrial applications is its ability to cater to a variety of materials. From ferrous and non-ferrous metals to harder materials like composites and plastics, this machine handles it all with exceptional ease. The adaptability of the equipment makes it ideal for diverse sectors, ranging from automotive and aerospace to construction and manufacturing.
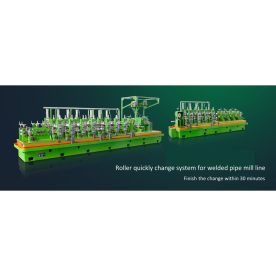
Revolutionizing Industrial Cutting: The Advantages of the High-Speed Cold Cutting Saw Machine for Precision Engineering
In terms of operational efficiency, these machines are engineered for high-performance cutting at rapid speeds. The ability to cut through metal up to five times faster than traditional band saws significantly boosts production rates. This increase in speed is coupled with enhanced accuracy, as the saw’s design minimizes the kerf loss—essentially the amount of material lost during the cutting process. As a result, manufacturers can expect higher yields from their materials, providing them with a significant competitive edge in the market.

Revolutionizing Industrial Cutting: The Advantages of the High-Speed Cold Cutting Saw Machine for Precision Engineering
Moreover, the High-Speed Cold Cutting Saw Machine is equipped with advanced technology that allows for programmable settings. Operators can easily adjust cutting speeds and parameters according to the specific requirements of the job. This programmable nature not only streamlines operations but also reduces the likelihood of human error—ensuring that each cut is executed with the utmost precision. Furthermore, the integration of digital interfaces facilitates easier monitoring of the cutting process, which further enhances performance predictability and operational safety.
From a maintenance perspective, the high-speed cold cutting saw is designed with durability and longevity in mind. The machines require less frequent maintenance compared to traditional saws, saving both time and money in the long run. Using high-quality materials and robust construction ensures that these machines withstand the rigors of continual industrial use. Consequently, businesses can find comfort in their investment, knowing that they are equipped with reliable technology that contributes positively to their production lines.
Safety is another critical consideration when it comes to industrial cutting operations. High-Speed Cold Cutting Saw Machines feature numerous safety mechanisms designed to protect operators and minimize the risk of accidents. Automatic shut-off features, emergency stop buttons, and protective enclosures are just a few of the many options available, thereby enhancing the overall safety of the workplace.
In conclusion, the High-Speed Cold Cutting Saw Machine represents a significant advancement in cutting technology, offering unmatched precision, speed, and versatility. Its ability to efficiently handle a wide range of materials while minimizing waste and maximizing productivity makes it an indispensable tool in modern manufacturing settings. As industries continue to seek innovative solutions to meet growing demands, investing in high-speed cold cutting technology can lead to substantial improvements in operational efficiency, product quality, and overall success. Whether in automotive, aerospace, or any other field that requires precision cutting, this machine is sure to become an essential part of any production process.Industrial-grade All-in-one Welder