In the ever-evolving world of manufacturing, the need for advanced technology to enhance productivity, quality, and efficiency is paramount. The IF Pipe Seam Annealing Machine has emerged as a critical tool in the pipe manufacturing industry, particularly for the production of high-quality welded pipes. This article delves into the functionalities, advantages, and applications of the IF pipe seam annealing machine, underscoring its significance in modern production processes.
Understanding the IF Pipe Seam Annealing Machine
The primary purpose of the IF pipe seam annealing machine is to optimize the properties of welded pipe seams by applying controlled heating processes. This machine utilizes the induction heating method, which employs electromagnetic induction to heat the material without direct contact. The inherent advantages of the IF pipe seam annealing machine include energy efficiency, precise heating control, and rapid processing times.
During the production of welded pipes, the seam area can experience various mechanical and thermal stresses due to the welding process. These stresses can lead to issues such as brittleness, poor ductility, and ultimately, compromised structural integrity. The IF pipe seam annealing machine addresses these issues by heating the pipe seams to a specific temperature, allowing for a recrystallization process that restores the metal’s ductility and strength properties.
Advantages of the IF Pipe Seam Annealing Machine
1. **Enhanced Material Properties**: One of the key benefits of using the IF pipe seam annealing machine is the enhancement of mechanical properties of the welded area. The controlled heating not only relieves internal stresses but also improves the overall toughness and ductility of the material, making it better suited for various applications.
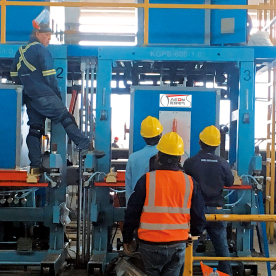
Revolutionizing Pipe Manufacturing: The Essential Role of the IF Pipe Seam Annealing Machine in Modern Production Processes
2. **Energy Efficiency**: Compared to traditional heating methods, such as furnace heating, the induction heating process employed by the IF machine is significantly more energy-efficient. It selectively heats only the seam area, leading to reduced energy consumption and lower operational costs.
3. **Speed and Productivity**: The rapid heating and cooling cycles facilitated by the IF pipe seam annealing machine contribute to increased production speeds. Manufacturers can achieve high throughput rates without sacrificing quality, which is crucial in a highly competitive market.
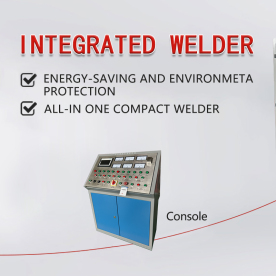
Revolutionizing Pipe Manufacturing: The Essential Role of the IF Pipe Seam Annealing Machine in Modern Production Processes
4. **Consistent Quality**: Consistency in production quality is vital in the pipe manufacturing industry. The IF machine ensures uniform heating, reducing the risk of defects and variations in the welded seam. This predictability in results can significantly enhance a manufacturer’s reputation and reliability in the market.
5. **Automatic Control**: Modern IF pipe seam annealing machines are equipped with advanced control systems that automatically adjust parameters such as temperature, speed, and heating time. This automation minimizes human error, ensuring that every seam is treated with precision.
Applications in Industry
The IF pipe seam annealing machine is utilized across a range of industries where welded pipes are essential. Some key applications include:
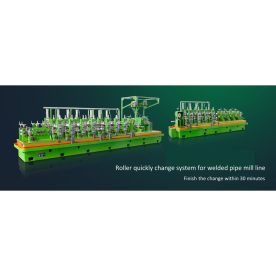
Revolutionizing Pipe Manufacturing: The Essential Role of the IF Pipe Seam Annealing Machine in Modern Production Processes
– **Oil and Gas Industry**: Pipelines require highly durable and reliable pipes to transport oil and gas. The annealing process ensures that the welded seams can withstand high pressures and harsh conditions.
– **Water Supply and Treatment**: Welded pipes used in water distribution systems benefit from annealing, which enhances their resistance to corrosion and extends their service life.
– **Construction**: In construction, the strength and durability of pipes are critical. The IF pipe seam annealing machine helps produce pipes that can handle structural loads and environmental stressors.
– **Automotive and Aerospace**: These industries require pipes that are not only strong but also lightweight. The annealing process optimizes the properties of materials used in exhaust systems, fuel lines, and hydraulic systems.
Conclusion
In summary, the IF pipe seam annealing machine plays an indispensable role in the manufacturing of high-quality welded pipes. By enhancing material properties, increasing energy efficiency, improving production speed, and ensuring consistent quality, the machine has revolutionized how manufacturers approach pipe production. As industries continue to demand higher standards and better-performing products, the significance of the IF pipe seam annealing machine will only grow. Investing in such advanced technology is not just an option; it’s a necessity for manufacturers aiming to thrive in a competitive landscape.Tailor-Made Spare Parts for Tube Mills