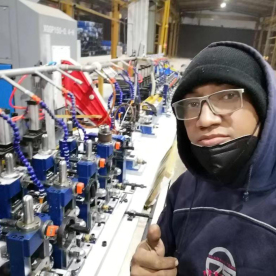
Exploring the Advantages and Applications of Industrial All-in-One High Frequency Welders in Modern Manufacturing
In the world of manufacturing and fabrication, the quest for efficiency, precision, and versatility is ongoing. Among the many tools that facilitate these objectives, the Industrial All-in-One High Frequency Welder stands out as a revolutionary solution. This piece of equipment not only enhances productivity but also ensures superior quality in welding processes across various industries. In this article, we will delve into the features, advantages, and applications of the Industrial All-in-One High Frequency Welder, highlighting why it has become indispensable in modern manufacturing.
Understanding High Frequency Welding
High frequency welding is a process widely used in industries ranging from automotive to packaging, as well as textiles and construction. It utilizes high frequency electromagnetic waves to generate heat in the materials being joined, typically plastics or thin metals, allowing them to fuse together without the need for additional filler materials or mechanical fasteners. This method provides various benefits, such as reduced operational costs, minimized energy consumption, improved product integrity, and enhanced welding speed.
The All-in-One Design
One of the primary advantages of the Industrial All-in-One High Frequency Welder is its integrated design. Traditional welder setups often require multiple devices, tools, and equipment. This not only consumes physical space but can also complicate workflows and increase setup times. The all-in-one unit consolidates these necessary components into a single unit, allowing for seamless operation and ease of use.
**Key Features:**
1. **Versatile Functionality:** The all-in-one design encompasses various welding techniques, enabling manufacturers to switch between processes with minimal downtime. This versatility is crucial for production lines that handle different projects concurrently.
2. **Compact Footprint:** By combining several welding capabilities into one machine, businesses can save valuable floor space in their operational environment—a critical factor for facilities aiming to maximize efficiency.
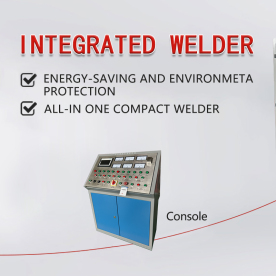
Exploring the Advantages and Applications of Industrial All-in-One High Frequency Welders in Modern Manufacturing
3. **User-Friendly Interface:** Modern Industrial All-in-One High Frequency Welders come with intuitive control panels and digital displays, allowing operators to monitor and adjust settings easily. This user-centric design reduces the learning curve for new employees and results in shorter training times.

Exploring the Advantages and Applications of Industrial All-in-One High Frequency Welders in Modern Manufacturing
4. **Energy Efficiency:** These machines are often designed with energy-saving features, allowing manufacturers to decrease their energy consumption while maintaining high output levels. With rising energy costs, this attribute represents significant cost savings over time.
Advantages of Using an All-in-One High Frequency Welder
The multifaceted benefits of an Industrial All-in-One High Frequency Welder are essential for manufacturers looking to remain competitive:
– **Increased Productivity:** The speed at which high frequency welding can be performed contributes to higher output rates. With faster setup and operation, businesses can expand production without necessitating additional labor costs.
– **Quality Assurance:** High frequency welding provides precision that is often unmatched by other welding methods. This precision directly translates to fewer defects and reworks, encouraging a higher standard of quality in products, which is crucial in today’s competitive markets.
– **Cost-Effectiveness:** By reducing the need for multiple machines and lowering energy consumption, these welders help businesses save money in both initial investments and ongoing operational expenses.
– **Enhanced Flexibility:** The ability to quickly transition between different welding tasks means that manufacturers can respond to market demands more readily. This flexibility allows companies to experiment with new products or variations without significant disruption to their current workflows.
Applications Across Industries
The Industrial All-in-One High Frequency Welder has found applications across numerous sectors, including:
– **Automotive Manufacturing:** Used for welding components of vehicles, such as bumpers and other plastic parts. – **Textile Industry:** Welding fabrics for bags, protective gear, and clothing, enhancing durability and appearance. – **Packaging:** For creating airtight seals in packaging materials to ensure product safety and longevity.
Conclusion
The Industrial All-in-One High Frequency Welder represents an unmatched combination of efficiency, flexibility, and precision in modern manufacturing. By streamlining processes, reducing costs, and improving product quality, these advanced welding machines are indispensable tools for any manufacturer aiming to thrive in today’s fast-paced, competitive landscape. Embracing this technology not only aligns with industry standards but also propels businesses toward greater innovation and success in their respective fields.Precision-control All-in-one Welding Equipment