In the ever-evolving world of manufacturing and metal processing, efficiency, precision, and safety are paramount. Among the various tools that contribute to these factors, the Industrial Cold Cutting Saw Machine stands out for its remarkable ability to deliver high-quality cuts while preserving the integrity of the material. This article delves into the operational mechanics, advantages, and diverse applications of industrial cold cutting saw machines, highlighting why they have become indispensable in contemporary manufacturing settings.
What is an Industrial Cold Cutting Saw Machine?
An industrial cold cutting saw machine employs a circular saw blade to cut metal materials without generating excessive heat. Unlike traditional band saws or high-speed cutting methods, cold cutting techniques involve lower RPM speeds, which significantly reduce the generation of thermal energies during the cutting process. This unique characteristic minimizes the risk of warping or distorting the metal, preserving its properties and potentially saving on additional finishing processes required to remove heat-induced stresses.
Key Advantages of Cold Cutting Saw Machines
1. **Precision Cutting**: One of the most significant benefits of industrial cold cutting saw machines is precision. The slow-speed operation combined with high-quality blades ensures that cuts are clean and accurate. This precision is essential in sectors where tolerances are tight, such as in the aerospace, automotive, or electronics industries.
2. **Material Preservation**: The cold cutting process is gentle on materials. It minimizes heat-affected zones, which can alter the metallurgy of a material and affect its mechanical properties. This preservation translates into better quality end products and longer life spans for machined components.
3. **Reduced Burrs and Clean Surface Finish**: Cold cutting results in fewer burrs and a cleaner surface finish compared to other cutting methods. This advantage reduces the need for post-processing tasks, helping manufacturers lower operational costs and speed up production times.
4. **Versatility**: Industrial cold cutting saw machines can cut through a diverse array of materials, including various metals such as aluminum, steel, and copper. They can handle multiple shapes and sizes, accommodating both small batch jobs and high-volume production runs.
5. **Enhanced Safety Features**: The slower operational speed and optimized design of these machines contribute to a safer working environment. With reduced risks of overheating or sparks, operators are less exposed to hazards associated with high-speed machining operations.
Applications of Industrial Cold Cutting Saw Machines
The versatility of cold cutting saw machines allows them to be employed in a myriad of applications across different industries:
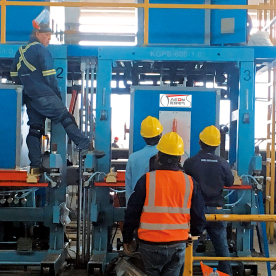
Understanding the Key Benefits and Applications of Industrial Cold Cutting Saw Machines in Modern Manufacturing Processes
– **Metal Fabrication**: In metal fabrication shops, these machines are indispensable for cutting metal profiles, tubes, sheets, and other components with high precision and surface quality.
– **Aerospace Industry**: Parts used in aerospace require extreme accuracy and minimal thermal distortion. Cold cutting allows manufacturers to produce components that meet stringent regulatory standards without compromising on quality.
– **Automotive Manufacturing**: The automotive industry frequently uses cold cutting saw machines to produce components that require precise fits and finishes, ensuring overall reliability and performance of vehicles.
– **Construction and Structural Applications**: Architects and builders use cold cutting saws to obtain clean cuts in materials used for structural frameworks, enhancing the aesthetic appeal and structural integrity of constructions.
– **Shipbuilding**: In shipbuilding, where size and weight restrictions are critical, cold cutting machines provide the ability to cut large metal panels while maintaining the necessary specifications and tolerances.
Conclusion
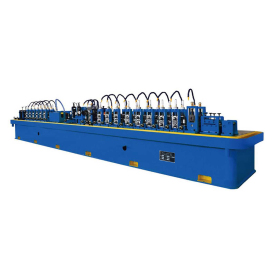
Understanding the Key Benefits and Applications of Industrial Cold Cutting Saw Machines in Modern Manufacturing Processes
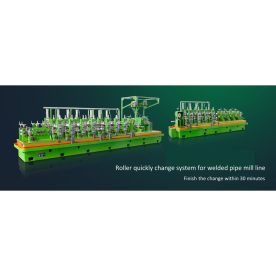
Understanding the Key Benefits and Applications of Industrial Cold Cutting Saw Machines in Modern Manufacturing Processes
The Industrial Cold Cutting Saw Machine is a crucial asset in today’s manufacturing landscape. Its ability to combine precision, efficiency, and safety makes it integral to a wide range of applications, from metal fabrication to aerospace and beyond. As industries continue to evolve and demand higher quality production processes, the role of cold cutting technology is expected to grow. Investing in modern cold cutting saw machines not only enhances the quality of output but also strengthens a company’s competitive edge in the market. It is evident that as we look towards the future of manufacturing, cold cutting technology will remain a pillar of quality and innovation.High frequency welder price