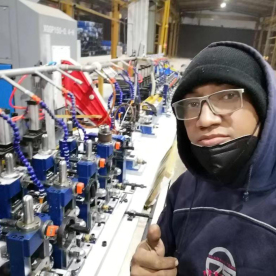
Revolutionizing Manufacturing Efficiency: The Impact of Industrial-Grade Induction Heating Equipment on Modern Production Lines
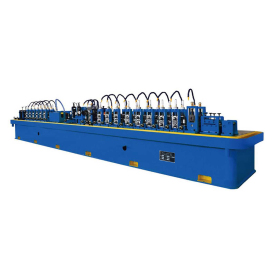
Revolutionizing Manufacturing Efficiency: The Impact of Industrial-Grade Induction Heating Equipment on Modern Production Lines
In the fast-evolving manufacturing industry, the continuous quest for efficiency, energy savings, and precision has led to the adoption of advanced technologies. One of the most transformative technologies is industrial-grade induction heating equipment. This sophisticated machinery has established itself as a cornerstone in various production processes due to its unparalleled benefits in heating and energy management.
Induction heating works on the principle of electromagnetic induction, where an alternating current is passed through a coil, generating a magnetic field. This magnetic field induces a current in conductive materials, producing heat in the material itself rather than relying on external heating methods. This unique characteristic significantly improves the heating process as it enables rapid and uniform heating of metal parts, making it an essential tool in many industrial applications.
One of the most notable advantages of industrial-grade induction heating equipment is its energy efficiency. Traditional heating methods often waste a considerable amount of energy, heating the surrounding environment and not just the material. In contrast, induction heating directly heats the workpiece, minimizing energy loss. This characteristic not only reduces energy consumption but also lowers operational costs, which is critical for manufacturers striving to improve profit margins in a competitive marketplace.
Furthermore, induction heating allows for precise temperature control, which is vital in many industrial processes, such as forging, hardening, annealing, and brazing. The ability to attain and maintain specific temperatures ensures that materials are treated uniformly, leading to enhanced product quality and fewer defects. This precision can also shorten processing times, as items can undergo rapid heating cycles without the risk of overheating or damaging the material. This benefit is particularly evident in fast-paced industries where production speed is crucial.
Another significant advantage of industrial-grade induction heating equipment is its versatility. The technology can be utilized across various applications, including metalworking, automotive manufacturing, aerospace components, and even the food and medical industries. Different types of induction heating systems can accommodate various sizes of materials and help manufacturers achieve specific heating configurations needed for their processes. As industries seek to adopt lean manufacturing principles, the adaptability of induction heating technology plays a pivotal role in meeting diverse manufacturing requirements.
The safety features of induction heating equipment also enhance its appeal. Traditional heating methods can pose risks, including burns and fire hazards due to the presence of hot surfaces and flames. Induction heating systems operate at lower temperatures externally, significantly reducing the risk of injury to operators. Moreover, they often come equipped with advanced features, including temperature monitoring and automatic shut-off mechanisms, further ensuring workplace safety.
As businesses strive to adopt greener manufacturing practices, the environmental impact of industrial processes has become increasingly important. The efficiency of induction heating equipment results in reduced carbon footprints due to lower energy consumption and the potential to use renewable energy sources. Additionally, since induction heating does not produce fumes or by-products like some conventional heating methods, it contributes to cleaner manufacturing environments.
The growing trend of automation and Industry 4.0 integration has also spotlighted the role of industrial-grade induction heating equipment. These systems can be easily integrated into automated production lines, allowing for real-time monitoring and control. This connectivity not only enhances operational efficiency but also provides data analytics to inform decision-making processes and predict maintenance needs.
Despite its many advantages, the initial investment in industrial-grade induction heating equipment can be significant. However, manufacturers must weigh this upfront cost against the long-term savings and efficiency gains. In many cases, companies find that the return on investment justifies the expenditure as they benefit from reduced operational costs, increased production rates, and enhanced product quality.

Revolutionizing Manufacturing Efficiency: The Impact of Industrial-Grade Induction Heating Equipment on Modern Production Lines
In conclusion, industrial-grade induction heating equipment is revolutionizing manufacturing by providing energy-efficient, precise, and safe heating solutions. Its versatility makes it suitable for various applications, while its compatibility with modern automation and sustainability efforts positions it as a vital component in the future of manufacturing. As industries continue to evolve and adapt, investing in this advanced technology will likely yield significant competitive advantages, enabling manufacturers to meet the challenges of the 21st century head-on.Annealing Machine Applications in Industry