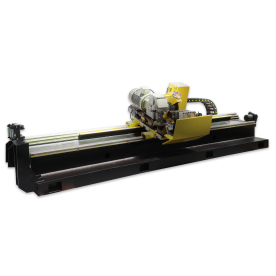
Exploring the Advancements and Applications of Industrial Tube Making Machinery in Modern Manufacturing Processes
****
In the world of manufacturing, the production of tubes is a crucial element across various industries, including construction, automotive, aerospace, and energy. Industrial tube making machinery is designed to meet the increasing demands for precision, efficiency, and versatility in tube production. This article delves into the advancements in industrial tube making machinery, its applications, and the essential role it plays in enhancing productivity and quality in manufacturing processes.
Understanding Industrial Tube Making Machinery
Industrial tube making machinery encompasses a range of specialized equipment used to manufacture tubes from various materials, including metals, plastics, and composites. These machines can create tubes with specific dimensions, wall thicknesses, and material properties tailored to meet stringent industry standards. The machinery can include processes such as extrusion, welding, bending, and more, depending on the final product requirements.
The Evolution of Tube Making Technology
Traditionally, tube production was a manual process, characterized by labor-intensive techniques that limited precision and efficiency. However, the rise of automation and advanced engineering has led to the development of sophisticated tube making machinery. Today’s machines leverage computer numerical control (CNC) technology, robotics, and sophisticated software to enhance production capabilities.
One of the significant advancements in this field is the integration of Industry 4.0 principles, which allow for smart manufacturing systems that optimize production lines. This includes real-time monitoring, predictive maintenance, and data analytics to improve efficiency and reduce downtime. This technological evolution has enabled manufacturers to produce high-quality tubes faster and with minimal waste, responding swiftly to market demands.
Various Types of Industrial Tube Making Machinery
1. **Tube Extrusion Machines**: These machines force a material, usually plastic or metal, through a die to create long tubes of uniform shape and size. Extrusion is preferred for its efficiency and the ability to produce continuous lengths of tubing.
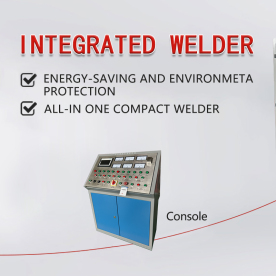
Exploring the Advancements and Applications of Industrial Tube Making Machinery in Modern Manufacturing Processes
2. **Tube Welding Machines**: Used mainly for metals, these machines are designed to join tube sections through various welding processes, including TIG, MIG, and laser welding. They ensure strong, reliable seams that meet structural integrity requirements.
3. **Tube Bending Machines**: These machines are vital for creating curved or angled tubes used in various applications. They can be programmed to produce complex angles and radii, which are particularly important in industries like automotive and aerospace.
4. **Tube Forming Machines**: These machines shape flat sheets of material into tubes. They can be set to create specific geometries that are necessary for specialized applications, such as HVAC systems or manufacturing equipment.
Applications Across Industries
The versatility and precision of industrial tube making machinery find applications across a wide range of sectors:
– **Automotive Industry**: Tubes are fundamental components in exhaust systems, fuel lines, and structural elements. The demand for lightweight, high-strength tubes has propelled advancements in materials and machinery.
– **Construction**: Steel and aluminum tubes are indispensable in building frameworks, plumbing, and electrical conduits. Industrial tube making machinery ensures that these critical components meet the demanding specifications of modern infrastructure.
– **Aerospace**: In aerospace applications, tubes must adhere to rigorous safety and performance standards. Machinery that can produce high-tolerance, lightweight tubes is essential for manufacturing aircraft parts.

Exploring the Advancements and Applications of Industrial Tube Making Machinery in Modern Manufacturing Processes
– **Energy Sector**: Tubes used in oil and gas pipelines, as well as renewable energy systems, must showcase exceptional durability and resistance to harsh environmental conditions. Advanced manufacturing techniques enhance the reliability of these components.
The Future of Industrial Tube Making Machinery
As industries strive toward sustainability, the future of industrial tube making machinery will likely incorporate eco-friendly materials and processes. Innovations in recycling technologies and the use of biodegradable materials are paving the way for a more sustainable approach to tube manufacturing.
In conclusion, industrial tube making machinery is at the forefront of manufacturing technology, continually evolving to meet the diverse needs of various sectors. As advances in automation and material science progress, the capabilities of tube making machinery will only continue to expand, solidifying its essential role in modern manufacturing and contributing to a more efficient and sustainable industrial landscape.Customized Flying Saw Machine