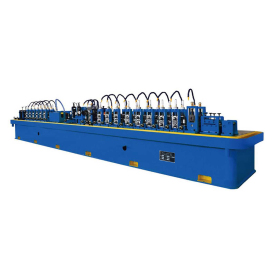
Exploring the Latest Advances in Industrial Tube Making Machinery: Revolutionizing Manufacturing Processes and Enhancing Efficiency
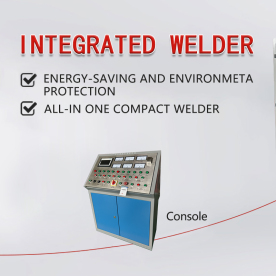
Exploring the Latest Advances in Industrial Tube Making Machinery: Revolutionizing Manufacturing Processes and Enhancing Efficiency
In recent years, the manufacturing sector has experienced a significant transformation, driven largely by technological advancements and the demand for enhanced productivity. Among the innovations playing a pivotal role in this evolution is the industrial tube making machinery. These machines have not only increased operational efficiency but have also improved the quality and precision of the tubes produced across various industries.
The industrial tube making machinery comprises a range of advanced equipment designed for the production of tubes made from various materials, including metals, plastics, and composites. The applications for these tubes are diverse, spanning industries such as automotive, aerospace, construction, and energy. Given the extensive range of requirements in these sectors, manufacturers need highly efficient, reliable, and versatile machinery to meet production demands.
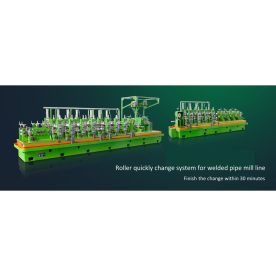
Exploring the Latest Advances in Industrial Tube Making Machinery: Revolutionizing Manufacturing Processes and Enhancing Efficiency
One of the major advancements in industrial tube making machinery is the introduction of automation and computer numerical control (CNC) systems. These technologies have fundamentally changed how tube manufacturing operates. Automation allows for increased production speed, while CNC technology offers precision that was previously unattainable with manual processes. As a result, manufacturers can produce complex shapes and designs with minimal human intervention, reducing the chances of error and wastage.
Moreover, modern tube making machinery is equipped with intelligent monitoring systems that track production in real time. These systems analyze performance data to identify bottlenecks, predict maintenance needs, and ensure optimal operation. This predictive maintenance feature minimizes downtime and extends the life of the machinery, which is crucial for manufacturers looking to maximize return on investment.
Another significant trend in the industry is the use of eco-friendly materials and processes. With growing concerns about climate change and environmental sustainability, manufacturers are increasingly seeking machinery that allows them to produce tubes with reduced energy consumption and lower emissions. Many modern industrial tube making machines incorporate energy-efficient technologies that help in achieving these goals. Additionally, the ability to recycle materials during the production process not only conserves resources but also decreases overall production costs.
The versatility of industrial tube making machinery cannot be overstated. Manufacturers can produce a wide range of tube sizes and shapes, catering to specific industry needs. For instance, in the automotive sector, manufacturers require tubes for exhaust systems, fuel lines, and structural components, each demanding unique specifications. Meanwhile, the aerospace industry requires lightweight, durable tubes for airframes and engine components. The flexibility of advanced tube making machinery allows manufacturers to easily switch between different types of production runs, making it an ideal solution in today’s fast-paced manufacturing environment.
Furthermore, the advances in materials science have also influenced the design and functionality of tube making machinery. Manufacturers can now work with high-performance alloys and composites that offer strength, lightweight characteristics, and resistance to extreme temperatures and corrosive environments. This has led to the creation of tubes that can withstand demanding applications in industries like oil and gas, where the surrounding conditions can be particularly harsh.
In addition to its production capabilities, industrial tube making machinery also emphasizes safety and ergonomics. With automated systems, the risk of workplace injuries is significantly reduced. Operators benefit from easier interfaces and improved control, enabling them to manage operations with greater ease and comfort. As a result, manufacturers can maintain a safer and more productive work environment.
The rise of the digital revolution has also impacted the industrial tube making sector, with the integration of the Internet of Things (IoT) and Industry 4.0 principles. Manufacturers are increasingly adopting connected machinery that allows for better data sharing and analysis, ultimately leading to smarter production processes. This connectivity fosters collaboration across different manufacturing stages and facilitates faster decision-making.
In conclusion, the advancements in industrial tube making machinery are set to continue shaping the manufacturing landscape. By adopting innovative technologies, manufacturers can enhance production efficiency, maintain quality control, and respond to market demands more effectively. As these machines become more sophisticated and aligned with sustainability goals, the future of tube manufacturing looks promising, paving the way for more sustainable and efficient manufacturing practices. Companies that stay ahead of the curve by investing in modern tube making machinery will likely enjoy a competitive advantage in an increasingly complex and demanding market.Pneumatic Cold Cutting Saw Machine