****
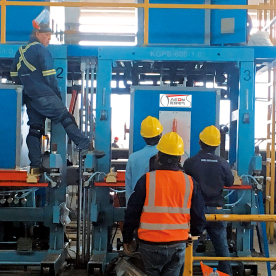
Exploring the Advantages and Innovations in Integrated Pipe Mill Production Line Systems for Enhanced Manufacturing Efficiency
In the ever-evolving landscape of industrial manufacturing, the need for improved efficiency, precision, and adaptability has never been more critical. One of the most significant advancements in this sector has been the development and implementation of integrated pipe mill production line systems. These systems represent a paradigm shift from traditional manufacturing processes, offering seamless integration of various stages of pipe production—from raw material processing to finishing and quality control. This article delves into the mechanics, advantages, and innovations surrounding integrated pipe mill production lines, showcasing how they revolutionize the pipe manufacturing industry.
Understanding Integrated Pipe Mill Production Line Systems
An integrated pipe mill production line system encompasses various stages of pipe production, including the melting and forming of metal, welding, heat treatment, and surface finishing. Unlike conventional systems that require separate and often disjointed processes, an integrated system combines these stages into a single cohesive operation. This integration leads to enhanced workflow, increased efficiency, and a reduction in waste and potential errors during production.
The core of an integrated pipe mill production line is its ability to automate and synchronize each step of the manufacturing process. This is achieved through advanced technologies such as computer numerical control (CNC), real-time monitoring systems, and data analytics. These technologies allow for precise control over every aspect of production—from regulating temperatures during metal treatment to monitoring the dimensions of finished pipes.
Advantages of Integrated Pipe Mill Production Line Systems
1. **Increased Efficiency:** One of the most compelling benefits of integrated pipe mill production lines is the significant increase in operational efficiency. By streamlining the production processes, manufacturers can reduce the time taken to convert raw materials into finished products. This improved throughput not only meets market demands but also enhances profitability.
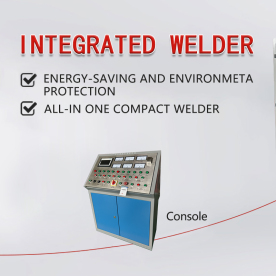
Exploring the Advantages and Innovations in Integrated Pipe Mill Production Line Systems for Enhanced Manufacturing Efficiency
2. **Cost Reduction:** Integrating multiple stages of production into one system reduces overhead costs associated with managing separate operations. Additionally, waste generated during production is minimized through improved process control, leading to further cost savings.
3. **Enhanced Quality Control:** Quality assurance is paramount in pipe manufacturing, particularly in industries such as oil and gas, construction, and automotive. Integrated pipe mill systems incorporate sophisticated monitoring tools that ensure each pipe meets stringent quality standards. Defects can be detected in real time, allowing for instant remediation and minimizing the production of faulty products.
4. **Flexibility and Customization:** The ability to adapt to varying production needs is another advantage of integrated systems. With advanced software and machinery, manufacturers can quickly switch between different pipe specifications, materials, and sizes. This flexibility is crucial in today’s market, where customization is often required to meet specific customer demands.

Exploring the Advantages and Innovations in Integrated Pipe Mill Production Line Systems for Enhanced Manufacturing Efficiency
5. **Sustainability:** As industries worldwide strive to adopt more sustainable practices, integrated pipe mill production line systems are increasingly becoming part of the solution. The reduction of waste, coupled with the ability to optimize resource usage, contributes to a more sustainable manufacturing process. Furthermore, some systems are designed to utilize recycled materials, further enhancing their eco-friendliness.
Innovations in Integrated Pipe Mill Production Line Systems
The advancements in technology underpinning integrated pipe mill production lines are continuously evolving. Recent innovations include the incorporation of Artificial Intelligence (AI) and machine learning capabilities into production processes. These technologies allow for predictive maintenance, where potential malfunctions can be identified and addressed before they disrupt production, contributing to ongoing system reliability.
Moreover, advancements in materials science have led to the development of new alloys and composites that can be seamlessly integrated into existing production lines. This allows manufacturers to enhance the properties of their pipes, resulting in stronger, lighter, and more corrosion-resistant products.
Another noteworthy innovation is the implementation of Industry 4.0 concepts, where the Internet of Things (IoT) plays a critical role. Through IoT connectivity, manufacturers can gain insights into the production process, enabling data-driven decision-making that enhances overall system performance.
Conclusion
Integrated pipe mill production line systems mark a significant advancement in the manufacturing landscape. By promoting efficiency, reducing costs, ensuring quality, and embracing technological innovation, these systems revolutionize how pipes are produced. As industries continue to demand high-quality, customizable products, the integrated approach will likely become the standard, pushing manufacturers to explore new heights of productivity and sustainability. The future of pipe production lies firmly in the hands of integrated systems, paving the way for a more efficient and environmentally responsible manufacturing era.High frequency welder machine