In the ever-evolving landscape of manufacturing, customized solutions have emerged as a pivotal element that determines the success and efficiency of production processes. Among these manufacturing technologies, pipe making machines play a crucial role in various industries, including construction, automotive, and oil and gas. As companies strive for better productivity, reduced waste, and increased profitability, the demand for pipe making machine customization solutions has grown significantly.
Pipe making machines are primarily used to produce a range of pipes that can be utilized in several applications. These machines can be tailored to meet specific operational needs, allowing manufacturers to output different pipe sizes, materials, and qualities based on their unique demands. Customization not only enhances operational efficiency but also opens doors for innovation in design and manufacturing methods.
One of the primary benefits of pipe making machine customization solutions is enhanced flexibility. Most standard machines are designed to produce one or a limited range of pipe types, often leading to overhead costs for businesses that need to produce various products. Customized machines, on the other hand, can be engineered to switch between different pipe types with minimal setup time, reducing idle time and increasing the overall output. This adaptability is particularly crucial in industries where demand can fluctuate or where clients may require unique specifications that aren’t easily met with standard equipment.
Furthermore, the customization process can incorporate the latest technological advancements, such as automated controls and smart manufacturing capabilities. For example, integrating advanced sensors and IoT (Internet of Things) technology allows for real-time monitoring and data collection, which can enhance predictive maintenance and optimize production rates. These innovations can lead to significant cost savings, as operators can rectify any issues before they escalate, thereby minimizing downtime.
Custom pipe making machines can also be specifically designed to cater to the particular materials used in pipe production. Different materials, such as PVC, steel, or composite substances, require unique handling and processing techniques. By customizing the machine’s components, such as the forming and welding stations, manufacturers can create processes that ensure the pipes’ structural integrity and performance, thereby improving product quality. For instance, utilizing specialized molds and dies during the shaping process can yield pipes with superior accuracy in dimensions and finish quality, resulting in fewer rejects and higher customer satisfaction.
Another vital aspect of customization is the ability to produce energy-efficient and environmentally friendly machines. With an increasing emphasis on sustainability, manufacturers are increasingly looking for solutions that minimize energy consumption and waste generation. Customization can lead to the design of machines that use less power without compromising performance. For instance, energy-efficient servo motors and optimized heating systems can drastically reduce the machine’s operational energy footprint while maintaining high throughput levels.
Additionally, the integration of automated feeding systems and robots can lead to minimal manual intervention, ensuring both safety and speed in manufacturing operations. This kind of intelligent customization aligns perfectly with the growing demand for high productivity levels while also reducing labor costs.
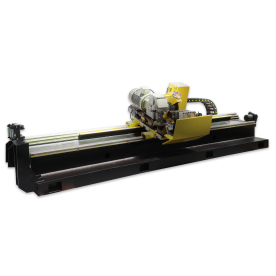
Innovative Pipe Making Machine Customization Solutions: Tailoring Efficiency and Precision for Modern Manufacturing Needs
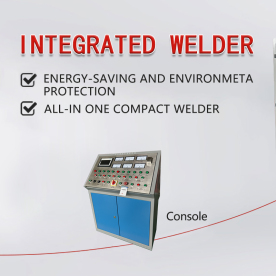
Innovative Pipe Making Machine Customization Solutions: Tailoring Efficiency and Precision for Modern Manufacturing Needs
It is also worth noting that customized pipe making machines can greatly simplify the integration of additional features that enhance functionality. These features might include marking systems for tracking production runs, automatic pipe cutting systems for precise lengths, and labeling machines for easier identification of products. Such additions can streamline operations from start to finish, creating a seamless manufacturing process.
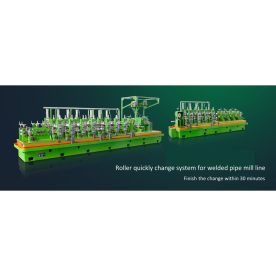
Innovative Pipe Making Machine Customization Solutions: Tailoring Efficiency and Precision for Modern Manufacturing Needs
While many manufacturing companies recognize the importance of customization, they might hesitate to invest due to perceived costs and complexities. However, it’s essential to understand that investing in customized pipe making machine solutions can lead to higher returns in the long run. The enhanced efficiency, product quality, and innovation brought by custom solutions can give companies a competitive edge in the market.
In conclusion, pipe making machine customization solutions are transforming how manufacturers approach production in various industries. By tailoring machines to meet specific operational needs, businesses can enjoy increased flexibility, operational efficiency, and product quality. As technology continues to advance, the potential for innovation within customized solutions will only grow, making it an essential strategy for manufacturers aiming to thrive in an increasingly competitive environment. Investing in such technologies promises not just to fulfill present needs but to pave the way for future growth and adaptability.Reliable Spare Parts for Cold Cutting Saws