In today’s fast-paced industrial environment, efficiency and precision are more crucial than ever. One of the machines leading the charge in pipe production is the pipe making machine. This specialized equipment has been instrumental in streamlining the manufacturing process for various types of pipes, catering to a wide array of industries such as construction, plumbing, and telecommunications. To understand its significance, we must explore how pipe making machines work, their advantages, and the advancements that have made them an essential part of manufacturing modern pipes.
A pipe making machine is designed to produce pipes from various materials, primarily steel, plastic, and other composites. The process typically begins with the formation of a flat strip or coil of raw material. This material is then fed into the machine, where it undergoes several crucial steps, including cutting, shaping, welding, and finishing. Most machines can produce a range of pipe diameters and wall thicknesses, allowing manufacturers to tailor their products to specific project requirements.
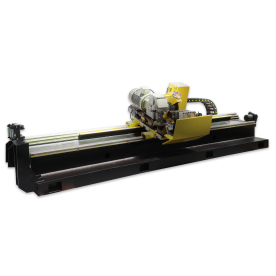
Revolutionizing Manufacturing: Exploring the Innovations and Benefits of the Pipe Making Machine in Modern Industries
One of the key innovations in the pipe making machine sector is the introduction of advanced automation and computer numerical control (CNC) technology. These advancements enable manufacturers to achieve a level of precision that was previously unattainable. Automatic feeding systems allow for faster production rates, reducing the time it takes to transition from raw material to finished product. CNC technology provides meticulous control over the manufacturing process, ensuring each pipe meets the exact specifications needed for its intended application.
The benefits of using a pipe making machine extend beyond mere efficiency. Firstly, automated machines tend to produce less waste, making the manufacturing process more environmentally friendly. The precision of modern pipe making machines also means fewer defects and tighter tolerances, which ultimately leads to higher quality products. When pipes are manufactured with precision, they are less likely to fail under pressure or during use, which is crucial in industries that rely on the integrity of their piping systems.
Moreover, pipe making machines can produce a variety of pipe types, including seamless, welded, and spiral pipes. This versatility opens up numerous market opportunities for manufacturers. For instance, seamless pipes are often used in high-pressure applications in the oil and gas industry, while welded pipes are prevalent in construction and plumbing. The ability to produce different types of pipes on the same machine reduces the need to invest in multiple pieces of equipment, thereby minimizing capital expenditure.
Another significant advantage of modern pipe making machines is their capacity to operate in a lean manufacturing environment. Many manufacturers today are adopting lean principles to optimize their operations by reducing waste, improving quality, and increasing efficiency. Pipe making machines equipped with data tracking and monitoring systems allow manufacturers to analyze production data in real-time. This capability enables immediate adjustments to be made in the production process, thus minimizing downtime and enhancing overall productivity.
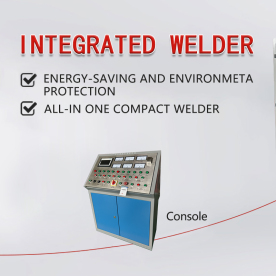
Revolutionizing Manufacturing: Exploring the Innovations and Benefits of the Pipe Making Machine in Modern Industries
As industries evolve, so too do the requirements for pipe manufacturing. The emerging trend towards sustainability and eco-friendliness has spurred innovation in pipe making machines. Newer models are being designed to utilize recycled materials and less energy during production. Manufacturers are also focusing on producing pipes that are safer for the environment while maintaining their durability and cost-effectiveness. This shift aligns well with global efforts to reduce carbon footprints and embrace greener practices in manufacturing.
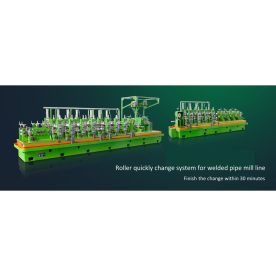
Revolutionizing Manufacturing: Exploring the Innovations and Benefits of the Pipe Making Machine in Modern Industries
In conclusion, the pipe making machine is a crucial component of modern manufacturing, merging efficiency with precision to produce high-quality pipes for various applications. As technology continues to advance, it is clear that the role of pipe making machines will only become more significant. By embracing these innovations, manufacturers can not only improve their own production capabilities but also contribute to a more sustainable industrial landscape. The future of pipe production looks promising, driven by a growing commitment to quality, efficiency, and environmental responsibility.Cost-Effective Spare Parts for Solid State HF Welding Machines