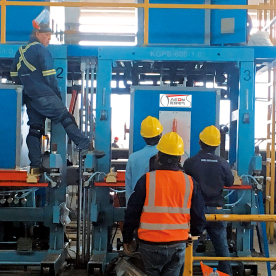
Enhancing Efficiency and Reliability in Pipe Mill Production Lines Through Comprehensive Quality Control Measures
The manufacturing of pipes is a vital component in various industries, including construction, automotive, and oil and gas. To meet the growing demands for quality and durability, modern pipe mill production lines must incorporate stringent quality control measures that ensure the final product meets or exceeds industry standards. This article explores the critical role of quality control in pipe mill production lines, highlighting the various measures and technologies employed to enhance efficiency and reliability.
Quality control in pipe manufacturing involves a systematic process that guarantees the quality and integrity of the pipes produced. It begins with raw material selection, where the quality of steel or other materials used significantly influences the performance of the final product. High-quality raw materials are essential, and suppliers are often vetted through rigorous quality assurance protocols. This selection process not only affects the end product’s durability but also its ability to resist corrosion and other environmental impacts.
Once the materials are procured, the production line processes begin. An advanced pipe mill production line typically consists of several stages, including forming, welding, testing, and finishing. These processes require close monitoring to maintain quality standards. For example, in the forming stage, the steel strip is processed into a cylindrical shape. Ensuring that the pipe wall thickness and diameter are consistent is crucial, as these factors directly impact the pipe’s strength and performance.
The welding process is another critical area where quality control measures are paramount. Whether using Electric Resistance Welding (ERW), Submerged Arc Welding (SAW), or other methods, the welds must be inspected for defects. Automated ultrasonic testing and X-ray inspections are commonly employed to detect any inconsistencies or flaws that could compromise the integrity of the welds. By utilizing these non-destructive testing methods, manufacturers can identify potential issues in real time, allowing for immediate corrective actions to be taken.
Post-welding, the pipes undergo rigorous testing to ensure they meet specified standards. Hydrostatic testing, where pipes are filled with water and subjected to high pressure, is a widely used method to assess the pressure resistance of pipes. This testing not only evaluates the pipe’s integrity but also helps identify any leaks or weak points. Additionally, various mechanical tests, such as tensile strength and yield strength tests, are conducted to ensure that the pipes can withstand the required loads during their operational lifespan.
The finishing stage is equally important in the pipe mill production line. Surface treatments such as galvanizing, coating, or painting help enhance the pipes’ resistance to corrosion and environmental damage. Quality control measures in this phase include thickness measurements of protective coatings and tests for adhesion strength. These assessments ensure that the protective layers are applied correctly and will hold up under various operating conditions.
Incorporating effective quality control measures also involves implementing a robust documentation and traceability system. Each stage of production should be logged with relevant data, including the material specifications, test results, and process parameters. This documentation is crucial for compliance with industry standards and regulations. It also allows manufacturers to analyze historical data to improve processes and quality over time.
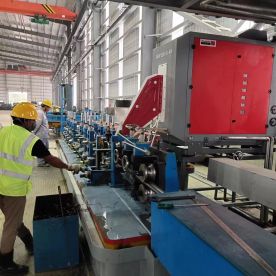
Enhancing Efficiency and Reliability in Pipe Mill Production Lines Through Comprehensive Quality Control Measures
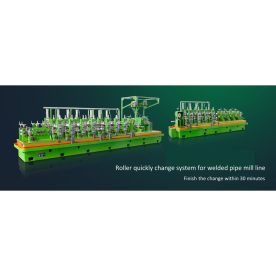
Enhancing Efficiency and Reliability in Pipe Mill Production Lines Through Comprehensive Quality Control Measures
Moreover, training and skill development of personnel operating the pipe mill production line play an essential role in quality assurance. Workers should be well-versed in the production processes and quality control protocols. Regular training sessions and workshops help ensure that employees are equipped with the latest techniques and technologies for effective quality management.
In conclusion, quality control measures in pipe mill production lines are essential for producing high-quality, reliable products that meet market demands. From raw material selection to post-production testing, each stage requires meticulous attention to detail and adherence to rigorous standards. By embracing advanced technologies and fostering a culture of quality, manufacturers can enhance the efficiency and reliability of their production lines, ultimately leading to improved customer satisfaction and competitive advantage in the marketplace. The commitment to quality not only safeguards the integrity of the pipes produced but also contributes to the overall safety and success of the projects in which they are utilized.Induction heating equipment