In the competitive realm of manufacturing, particularly within the domain of pipe production, maintaining a robust quality control system is paramount. A pipe mill production line represents a sophisticated and intricate assembly of equipment and processes designed to manufacture high-quality pipes. For industries that rely on pipes, such as construction, oil and gas, and infrastructure, the impact of quality cannot be overstated. Therefore, implementing comprehensive quality control measures throughout the production process is essential in ensuring product reliability, safety, and performance.
Overview of the Pipe Mill Production Line
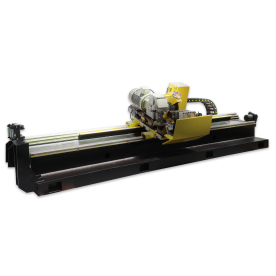
Streamlining Efficiency and Ensuring Excellence: An In-Depth Look at Pipe Mill Production Line with Quality Control Measures
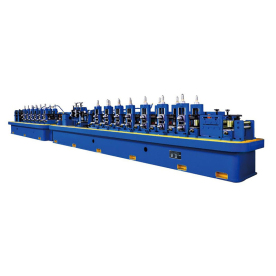
Streamlining Efficiency and Ensuring Excellence: An In-Depth Look at Pipe Mill Production Line with Quality Control Measures
The pipe mill production line is a specialized setup that incorporates several stages: from raw material handling to finishing. The process generally begins with the selection of high-quality steel or other appropriate materials that will be transformed into pipes. This often involves a series of operations such as cutting, forming, welding, and finishing, which must all be carefully monitored and controlled.
The primary equipment involved in a pipe mill production line includes:
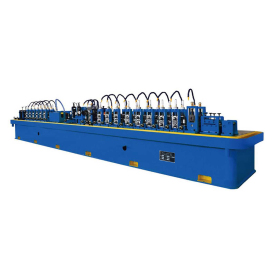
Streamlining Efficiency and Ensuring Excellence: An In-Depth Look at Pipe Mill Production Line with Quality Control Measures
1. **Slitter Line**: This machine cuts coils of metal into narrower strips, which will be fed into the next stages of production. 2. **Forming Machines**: These are responsible for shaping the metal strips into pipe profiles. Various methods can be employed, including roll forming and stretch forming. 3. **Welding Station**: Once the strips are formed, they are welded together to create a continuous pipe. This step often employs automatic or semi-automatic welding processes to ensure uniformity. 4. **Heat Treatment Units**: To improve the material properties of the pipes, heat treatment may be applied, ensuring the pipes can withstand various stresses and environmental conditions. 5. **Finishing and Inspection**: This final stage involves cutting the pipes to the desired lengths and performing surface treatments, such as cleaning and coating.
Importance of Quality Control Measures
Given the critical nature of pipes in various applications, implementing quality control measures at each stage of the pipe mill production line is vital. Quality control helps identify and rectify defects early in the manufacturing process, minimizing waste and ensuring compliance with industry standards.
Key Quality Control Measures
1. **Material Verification**: Collecting samples and performing tests on the raw materials before they enter the production line ensures that the metals used meet the required specifications. This initial step is crucial, as using subpar materials can lead to severe quality issues down the line.
2. **In-Process Inspections**: During the production phases, regular inspections at various checkpoints help monitor dimensional accuracy, weld integrity, and overall quality. Employing technologies such as X-ray or ultrasonic testing can be beneficial in evaluating welds and identifying any potential defects beneath the surface.
3. **Automated Monitoring Systems**: Integrating advanced sensors and monitoring systems throughout the production line helps gather real-time data on process conditions, such as temperature, pressure, and speed. This data can be analyzed to ensure optimal production conditions and automatically alert operators to any deviations from acceptable limits.
4. **Statistical Process Control (SPC)**: Implementing SPC techniques enables manufacturers to analyze variability within the production process. By collecting and analyzing data, companies can identify trends that may indicate potential quality issues and make necessary adjustments proactively.
5. **Final Inspection and Testing**: Once the pipes are produced and finished, a final inspection is performed, which may include dimensional checks, pressure tests, and surface quality assessments. This step is critical to ensure that the finished products meet all required standards before they are shipped to customers.
6. **Documentation and Traceability**: Maintaining comprehensive records of quality control measures and product specifications at each stage of the production line ensures traceability. In the event of a quality issue, having detailed documentation allows manufacturers to identify the source of the problem and take corrective action.
Conclusion
In conclusion, a pipe mill production line requires a meticulously orchestrated series of processes, all governed by stringent quality control measures. From raw material selection to final inspection, each stage plays a vital role in ensuring the production of high-quality pipes that meet the demands of various industries. By using state-of-the-art technology, conducting routine inspections, and employing statistical techniques, pipe manufacturers can optimize their production processes while ensuring that their products maintain the highest standards of quality and reliability. This not only builds trust with clients but also secures a competitive edge in the market.Solid state HF welder for metal processing