In the modern industrial landscape, the need for efficient, reliable, and innovative production solutions is at an all-time high. Among these solutions, the pipe mill production line stands out as a critical component in various sectors, including construction, oil and gas, plumbing, and manufacturing. What sets apart a state-of-the-art pipe mill production line is not just its ability to fabricate pipes but also its integrated welding and cutting functions, which collectively enhance overall productivity and quality. This article will delve into the significance of these integrated systems, their functionality, and their impacts on the manufacturing industry.
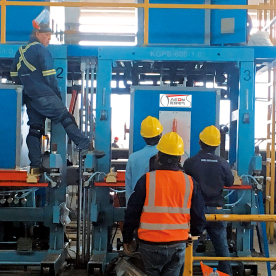
Enhancing Manufacturing Efficiency: The Comprehensive Role of Pipe Mill Production Lines with Integrated Welding and Cutting Functions
Understanding Pipe Mill Production Lines
Pipe mill production lines are sophisticated assembly systems designed specifically for the fabrication of pipes from raw materials such as steel, aluminum, and other metals. These lines can produce pipes of various dimensions and specifications, catering to diverse industrial needs. The production process typically involves the transformation of flat metal strips into round or square pipes through a series of mechanical processes, including forming, welding, and cutting.
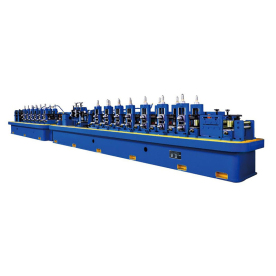
Enhancing Manufacturing Efficiency: The Comprehensive Role of Pipe Mill Production Lines with Integrated Welding and Cutting Functions
Integrated Welding Functions
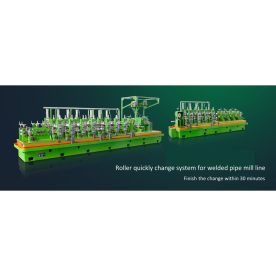
Enhancing Manufacturing Efficiency: The Comprehensive Role of Pipe Mill Production Lines with Integrated Welding and Cutting Functions
One of the pivotal components of advanced pipe mill production lines is the welding function. Welding is crucial for joining two or more metal pieces together to create strong, durable seams that can withstand high pressure and temperatures. In a traditional setup, welding processes may be conducted separately; however, modern pipe mills integrate this function directly into the production line.
The integration of welding machines, such as electric resistance welders or TIG (Tungsten Inert Gas) welding units, allows for real-time welding during the pipe fabrication process. This not only speeds up production times but also ensures consistency in weld quality. High-quality welds are essential in industries like oil and gas, where even the slightest defect can lead to catastrophic failures. The technological advancements in welding equipment contribute to more precise control over parameters like temperature and speed, which ultimately results in better weld integrity and reduced material wastage.
Cutting Functions: Precision and Efficiency
In addition to welding, cutting is another vital function integrated within the pipe mill production line. As pipes are manufactured, they must be cut to specified lengths to meet customer requirements. The cutting process should be efficient, fast, and precise, as it directly impacts production yield and material cost.
Modern pipe mills employ advanced cutting technologies, including laser cutting, saw cutting, and high-precision plasma cutting. These technologies allow for clean, straight cuts without significant burrs or deformations that could compromise the quality of the pipes. Laser cutting technology, in particular, is lauded for its ability to deliver high accuracy and reduced kerf width, allowing for more efficient use of raw material.
Furthermore, integrating cutting functions into the production line goes beyond simply expediting the process; it also provides the ability to change sizes and specifications quickly, enabling manufacturers to adapt to market demands with ease. This flexibility is crucial in today’s fast-paced industrial environment, where customization and rapid turnaround times are necessary for competitive advantage.
Benefits of Integrated Systems
The integration of welding and cutting functions within pipe mill production lines yields numerous benefits. Firstly, it enhances operational efficiency by reducing the need for separate processes that require additional labor and machine setups. Secondly, it improves quality control, as both welding and cutting can be monitored in real-time, reducing the likelihood of defects. Thirdly, it optimizes material usage by minimizing waste, as operators can fine-tune cutting dimensions more effectively and produce pipes that meet exact specifications.
Additionally, these integrated systems often come equipped with advanced software solutions and automation, further streamlining operations. The utilization of computer numerical control (CNC) technology facilitates precise programming of both welding and cutting actions, allowing manufacturers to maintain high production rates without sacrificing quality.
Conclusion
In conclusion, the role of pipe mill production lines with integrated welding and cutting functions is indispensable in today’s manufacturing landscape. These advanced systems not only provide a competitive edge by enhancing efficiency and lowering production costs but also ensure high-quality outputs that are essential in critical industries. As technology continues to advance, the evolution of pipe mill production lines will likely contribute to even greater innovations in manufacturing, thereby solidifying their place as a cornerstone of industrial production in the years to come.All-in-one High Frequency Welder Machine