In the world of industrial manufacturing, efficiency and precision are key factors in ensuring success. This is especially true in the production of pipes, which are used in a wide range of industries such as construction, oil and gas, and automotive. To meet the increasing demands for quality pipes, manufacturers are constantly seeking ways to improve their production processes. One of the latest innovations in pipe manufacturing is the development of pipe mill production lines that are equipped with welding and cutting functions.
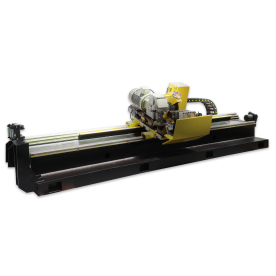
Revolutionizing Pipe Manufacturing with an Advanced Pipe Mill Production Line Equipped with Welding and Cutting Functions
Traditionally, pipe manufacturing involved multiple steps including cutting, welding, and shaping the pipes. This process was not only time-consuming but also prone to errors, leading to inconsistencies in the final products. However, with the advancement of technology, manufacturers can now streamline the pipe manufacturing process by integrating welding and cutting functions into a single production line.
The key component of these advanced pipe mill production lines is the automated welding system. This system uses advanced welding techniques such as submerged arc welding or gas metal arc welding to join the pipes together seamlessly. By automating the welding process, manufacturers can ensure consistent weld quality and eliminate the risk of human error. This not only improves the overall quality of the pipes but also increases production efficiency.
Additionally, the cutting function in these production lines plays a crucial role in shaping the pipes according to the desired specifications. The cutting system is equipped with high-precision cutting tools that can accurately cut the pipes to the required length and diameter. This ensures that the pipes meet the exact specifications set by the manufacturers, reducing material wastage and minimizing production costs.
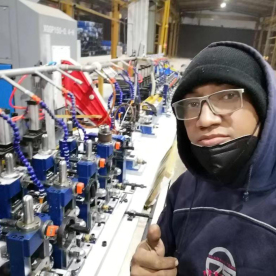
Revolutionizing Pipe Manufacturing with an Advanced Pipe Mill Production Line Equipped with Welding and Cutting Functions
Moreover, the integration of welding and cutting functions in a single production line offers several advantages to manufacturers. By combining these two processes, manufacturers can significantly reduce production time and increase output capacity. This not only enables manufacturers to meet tight deadlines but also allows them to take on large-scale projects without compromising quality.
Furthermore, the automated nature of these production lines also improves workplace safety by minimizing the need for manual labor in high-risk welding and cutting operations. This reduces the risk of accidents and injuries, creating a safer working environment for the operators.
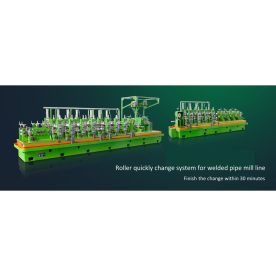
Revolutionizing Pipe Manufacturing with an Advanced Pipe Mill Production Line Equipped with Welding and Cutting Functions
In conclusion, the integration of welding and cutting functions in pipe mill production lines represents a significant advancement in the field of pipe manufacturing. By automating these essential processes, manufacturers can improve production efficiency, enhance product quality, and increase output capacity. This not only benefits the manufacturers but also the industries that rely on high-quality pipes for their operations. With the continuous development of technology, the future of pipe manufacturing looks brighter than ever.Roller for tube mill