In the realm of modern manufacturing and repair industries, the significance of advanced welding technologies cannot be overstated. Among these technologies, portable high frequency welders have emerged as a game-changer, redefining the standards of efficiency, convenience, and versatility in welding applications. This article explores the numerous advantages, applications, and technical insights behind portable high frequency welding, underscoring its crucial role in today’s fast-paced industrial landscape.
The Mechanics of Portable High Frequency Welders
At its core, the portable high frequency welder operates on the principle of generating high-frequency electrical currents that facilitate the welding process. This technique is particularly effective for bonding conductive materials like metals and thermoplastics. The welder generates a high-frequency electromagnetic field that penetrates the material, allowing precise heat generation at the joint interface. This results in expedited welding times and improved joint integrity, making these devices particularly valuable in settings where speed and quality are paramount.
Portability: A Key Feature
The term “portable” in portable high frequency welders signifies more than just lightweight design. These devices are engineered for ease of transport, enabling professionals to carry them to job sites with minimal hassle. Whether it’s a remote construction location, a maintenance facility, or an on-site repair job, the convenience of portability allows operators to perform welding tasks wherever the materials are located, eliminating the need for extensive setup processes.
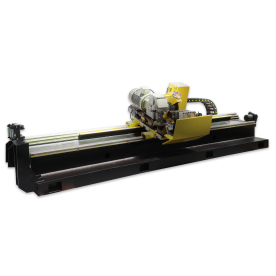
Exploring the Versatility and Efficiency of Portable High Frequency Welders for Diverse Industrial Applications
Advantages of Using Portable High Frequency Welders
1. **Versatility Across Applications**: One of the standout features of portable high frequency welders is their adaptability. They can be employed in a myriad of industries, ranging from automotive and aerospace to plumbing and construction. Whether working on intricate components or large structural elements, these welders can facilitate a wide variety of welding tasks.
2. **Enhanced Efficiency**: High frequency welding techniques are designed to minimize heat distortion, allowing for quicker welding speeds without sacrificing quality. This efficiency means that projects can be completed in less time, reducing labor costs and increasing productivity.
3. **Improved Weld Quality**: A portable high frequency welder delivers consistent results, thanks to its precise temperature control and uniform heat distribution. This feature is particularly advantageous when working with thin materials or when aesthetics are a priority, as it minimizes the risk of warping and other imperfections.
4. **User-Friendly Technology**: Modern portable high frequency welders come equipped with intuitive controls and digital interfaces, making them accessible to both novice and experienced welders. Features like automatic shut-off, adjustable frequency settings, and user-friendly operation reduce the learning curve and enhance safety.
5. **Cost-Effectiveness**: By investing in portable high frequency welders, businesses can significantly reduce operational costs. These tools require less energy compared to traditional welding methods and often need minimal maintenance, resulting in lower overhead expenses.
Industries Benefiting from Portable High Frequency Welding
1. **Automotive Industry**: In the automotive sector, high frequency welding is crucial for producing strong, reliable joints in both structural and cosmetic components. The lightweight nature of portable welders allows mechanics to perform repairs on vehicles efficiently.
2. **Aerospace Applications**: Aerospace components require exceptional strength-to-weight ratios, and portable high frequency welders provide the necessary precision and control. This technology is often used to bond lightweight materials that are increasingly prevalent in aircraft manufacturing.
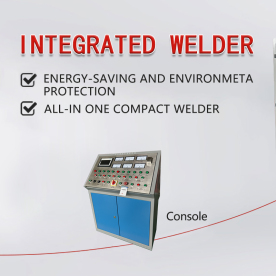
Exploring the Versatility and Efficiency of Portable High Frequency Welders for Diverse Industrial Applications
3. **Plumbing and HVAC**: With the growing prevalence of plastic pipes in plumbing and HVAC systems, high frequency welding has become an essential technique for creating leak-proof joints. The portability of these welders allows technicians to work directly on the job site, streamlining installation processes.
4. **Manufacturing and Fabrication**: Many fabrication shops utilize portable high frequency welding for both production runs and custom projects. The ability to quickly reposition the equipment enhances workflow efficiency and responsiveness to customer demands.
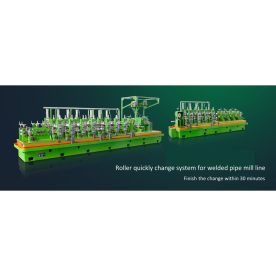
Exploring the Versatility and Efficiency of Portable High Frequency Welders for Diverse Industrial Applications
Conclusion
The emergence of the portable high frequency welder signifies a pivotal advancement in welding technology. With their impressive efficiency, versatility, and user-friendly design, these tools are redefining welding practices across various industries. As businesses continue to seek ways to enhance productivity and quality, the adoption of portable high frequency welders is poised to grow, solidifying their place as indispensable assets in the modern industrial toolkit. Investing in this technology not only streamlines operations but also sets the stage for innovation and improvement in welding practices for years to come.IF pipe seam annealing machine price comparison