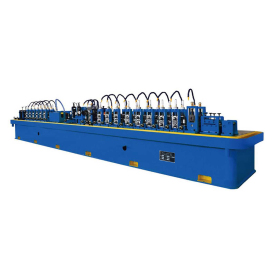
Revolutionizing Metal Fabrication: The Impact and Advantages of the Precision Cold Cutting Saw Machine in Modern Industry
In the ever-evolving landscape of manufacturing and metal fabrication, precision and efficiency are paramount. One of the most significant advancements in this field is the introduction of the Precision Cold Cutting Saw Machine. This innovative technology is redefining traditional cutting methods, enabling industries to achieve unprecedented accuracy while minimizing material waste. As we delve into the features, advantages, and applications of the Precision Cold Cutting Saw Machine, it becomes clear that it represents a crucial tool for modern manufacturing.
Understanding the Precision Cold Cutting Saw Machine
The Precision Cold Cutting Saw Machine is designed to cut materials with extreme accuracy while maintaining their structural integrity. Unlike traditional sawing methods that generate significant heat and often alter the properties of the material, cold cutting saws operate at lower temperatures. This reduced thermal impact preserves the material, resulting in clean edges and reducing the need for extensive finishing processes.
The technology employed in these machines is advanced, incorporating high-speed saw blades made from durable materials such as carbide or high-speed steel. These blades rotate at specific RPMs tailored to the material being cut, ensuring that the cutting performance is optimal. It is noteworthy that these machines can cut through a variety of materials, including metals like stainless steel, aluminum, and even some composites, making them versatile tools for various industries.
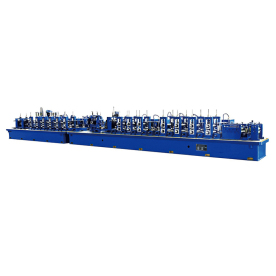
Revolutionizing Metal Fabrication: The Impact and Advantages of the Precision Cold Cutting Saw Machine in Modern Industry
Key Advantages of the Precision Cold Cutting Saw Machine
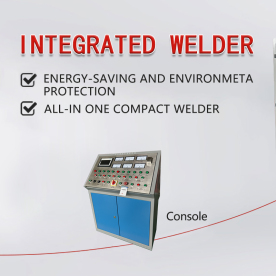
Revolutionizing Metal Fabrication: The Impact and Advantages of the Precision Cold Cutting Saw Machine in Modern Industry
1. **High Precision and Accuracy**: One of the most celebrated advantages of using a Precision Cold Cutting Saw Machine is its ability to achieve exact cuts. This feature is particularly essential in industries where tolerances are stringent, such as aerospace, automotive, and precision engineering. The precise cut reduces the need for additional processes like grinding or milling, leading to time savings and cost reductions.
2. **Minimal Material Waste**: Traditional cutting processes often lead to considerable waste, which can have significant financial implications for manufacturers. Cold cutting technology minimizes kerf loss— the width of the cut—allowing for more efficient use of raw materials. This efficiency not only lowers costs but also supports sustainability efforts, as less waste contributes to reduced environmental impact.
3. **No Heat-Affected Zones**: Unlike conventional sawing methods that produce heat, leading to changes in the material’s microstructure, the Precision Cold Cutting Saw Machine operates without significant heat generation. This characteristic is crucial in applications where maintaining the integrity and hardness of metal is required. It helps prevent warping and ensures that finished parts meet high-quality standards.
4. **Improved Safety**: Cold cutting machines tend to be safer than their traditional counterparts. The absence of high temperatures reduces the risk of burns or other heat-related injuries. Additionally, the precision and automation associated with these machines lead to a more controlled cutting environment, contributing to overall workplace safety.
5. **Versatility in Applications**: These machines are not limited to specific industries. Their capability to handle various materials and sizes makes them applicable in numerous fields, including construction, plumbing, and electrical installations. Additionally, as industries move towards more automated processes, the Precision Cold Cutting Saw Machine can integrate seamlessly into existing production lines.
Applications in Various Industries
The adoption of Precision Cold Cutting Saw Machines spans a wide array of industries. In the automotive sector, for instance, manufacturers utilize these machines to produce components with tight tolerances that meet rigorous safety standards. Similarly, the aerospace industry relies on the precision of these machines to ensure that critical aircraft components are manufactured with the utmost accuracy.
Moreover, the construction industry benefits from cold saw technology when fabricating metal supports and structural components. The electrical sector uses these machines for cutting conduit and piping, ensuring that fittings meet precise requirements for installation.
Conclusion
As we look toward the future, the Precision Cold Cutting Saw Machine stands at the forefront of metal fabrication technology. Its ability to deliver high precision, significantly reduce waste, enhance safety, and adapt to various applications marks a revolutionary step forward in modern manufacturing practices. Companies investing in this technology position themselves to benefit from increased efficiency and product quality, ultimately gaining a competitive edge in an increasingly demanding market. As industries continue to evolve, the Precision Cold Cutting Saw Machine will undoubtedly play a pivotal role in shaping their future.CNC Flying Saw Machine