In the ever-evolving world of manufacturing, the demand for high-quality tubes and pipes has led to significant advancements in technology. One such innovation that has revolutionized the industry is the Precision ERW (Electric Resistance Welded) tube mill machinery. This specialized equipment is designed to produce high-precision tubes at a rapid speed and is widely used in various sectors, including automotive, construction, furniture, and machinery.
Understanding Precision ERW Tube Mill Machinery
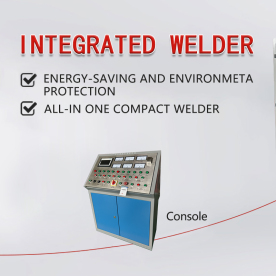
Exploring the Advantages and Innovations of Precision ERW Tube Mill Machinery in Modern Manufacturing Processes
At its core, ERW tube mill machinery utilizes an electric resistance welding process to manufacture tubular products. The process involves heating the edges of flat steel strips to form a tube and then welding them together to create a continuous tube. This method allows for the production of tubes with various diameters and wall thicknesses, catering to the diverse needs of different industries.
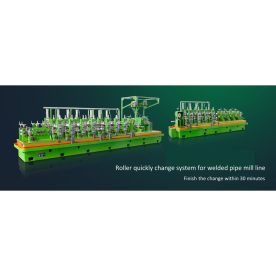
Exploring the Advantages and Innovations of Precision ERW Tube Mill Machinery in Modern Manufacturing Processes
Precision ERW tube mills are characterized by their ability to produce tubes with extremely tight tolerances. This is crucial for applications where precision is paramount, such as in the automotive industry, where tubes must fit perfectly into assembly processes. The term “precision” refers to the machinery’s capability to ensure consistent dimensions, circularity, and strength, which are all vital for end-product performance.
Key Features of Precision ERW Tube Mill Machinery

Exploring the Advantages and Innovations of Precision ERW Tube Mill Machinery in Modern Manufacturing Processes
1. **Advanced Control Systems**: Modern ERW tube mills are equipped with sophisticated control systems that monitor the entire production process. These systems can adjust settings in real time based on feedback from sensors, ensuring that the machinery operates at optimal levels. This feature not only enhances productivity but also minimizes waste and defects.
2. **High Speed and Efficiency**: Precision ERW tube mills are designed to operate at high speeds, significantly increasing production output. With advancements in technology, manufacturers can achieve faster cycle times without sacrificing quality. This efficiency meets the growing demand for just-in-time manufacturing practices, allowing producers to respond swiftly to market changes.
3. **Versatile Configurations**: These machines can be configured to produce a wide range of tube specifications, from small, thin-walled tubes to larger, heavy-duty variants. This versatility is especially beneficial for companies that serve multiple markets and need machinery that can adapt to different product requirements without extensive downtime for reconfiguration.
4. **Quality Assurance**: One of the standout features of precision ERW tube mills is their incorporation of inline quality assurance systems. These systems use non-destructive testing techniques to check the integrity of welded joints and the consistency of tube dimensions, ensuring that any defects are identified and corrected before the production batch is completed.
Benefits of Using Precision ERW Tube Mill Machinery
The investment in precision ERW tube mill machinery offers numerous benefits to manufacturers. One of the primary advantages is the cost-effectiveness achieved through reduced waste and improved material utilization. With precise control over the manufacturing process, companies can minimize scrap and rework, leading to increased profitability.
Additionally, the enhanced product quality associated with precision ERW tube production builds client trust and loyalty. When businesses can consistently deliver high-quality products that meet stringent industry standards, they position themselves as leaders in their fields. This reputation can lead to increased market share and new business opportunities.
Moreover, sustainability considerations are becoming increasingly important in manufacturing. Precision ERW tube mills not only reduce material waste but also consume less energy compared to conventional tube manufacturing processes. This aligns with global initiatives aimed at reducing the carbon footprint of industrial activities, making manufacturers more appealing to environmentally conscious consumers.
Future Trends
As technology continues to advance, the future of precision ERW tube mill machinery looks promising. Innovations in automation, artificial intelligence, and predictive maintenance are set to further enhance the capabilities of these machines. Manufacturers will likely see even greater efficiencies and product customization options, allowing them to stay competitive in a rapidly changing marketplace.
In conclusion, Precision ERW tube mill machinery represents a significant advancement in tube manufacturing technology. Its ability to produce high-quality, precise tubes efficiently makes it an essential tool for modern manufacturers. As industries continue to seek innovative solutions to meet their product demands, the capabilities of precision ERW tube mills will undoubtedly play a pivotal role in shaping the future landscape of manufacturing.Cost-Effective Spare Parts for Solid State HF Welding Machines