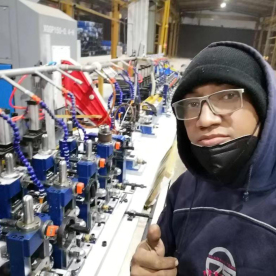
Exploring the Benefits and Applications of Precision Induction Heating Equipment in Modern Industries
Induction heating has emerged as a revolutionary technique in various applications, including manufacturing, automotive, aerospace, and metallurgy. Among the advancements in this field, precision induction heating equipment stands out for its ability to provide targeted heating solutions with unmatched efficiency and consistency. This article will delve into the principles of precision induction heating, its numerous advantages, and the different industries leveraging this technology to enhance their processes.
At its core, induction heating operates on the principle of electromagnetic induction. When an alternating current passes through a coil, it generates a magnetic field that induces an electric current in the conductive material placed within this field—typically, a metal. This induced current encounters resistance, generating heat directly in the metal rather than relying on external heating sources. Precision induction heating equipment is designed to optimize this process, allowing for controlled heating with exceptional accuracy.
One of the fundamental benefits of precision induction heating equipment is its energy efficiency. Traditional heating methods often lead to significant energy loss, primarily due to heat dissipation in the surrounding environment. In contrast, induction heating minimizes this loss by concentrating heat within the workpiece. The result is faster processing times and reduced operational costs, making it an attractive option for industries looking to improve productivity while minimizing energy consumption.
Another notable advantage of precision induction heating is its ability to provide uniform heating. Variability in temperature can lead to undesirable results such as warping, cracking, or uneven properties in materials. Precision induction heating equipment minimizes such variability, ensuring that the entire workpiece reaches the desired temperature in a uniform manner. This is especially crucial in applications like heat treating, where precise heating is necessary to achieve specific mechanical properties.
The versatility of precision induction heating equipment is one of its standout features. It can be used for a wide range of applications, including hardening, annealing, soldering, and melting. In the automotive industry, for example, induction heating is employed for processes such as gear hardening and wheel rim treatment. It allows manufacturers to achieve the hardness and tensile strength required in critical components while maintaining dimensional accuracy.
In the aerospace sector, the precision of induction heating allows for the treatment of high-performance alloys and materials that require strict adherence to tolerances. Aerospace components are often subjected to extreme conditions, making the reliability and integrity of each part essential. By using precision induction heating equipment, manufacturers can ensure that these components meet stringent specifications without compromising on quality.
Furthermore, the healthcare industry has also embraced precision induction heating technology. In the production of medical devices and implants, maintaining high levels of precision and sterility is paramount. Induction heating allows for quick sterilization of tools and equipment by rapidly raising temperatures without direct flame or prolonged exposure to high heat, reducing the risk of contamination.
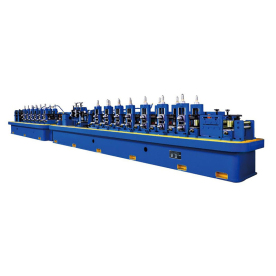
Exploring the Benefits and Applications of Precision Induction Heating Equipment in Modern Industries
Safety is another critical consideration in industrial heating processes. Traditional heating methods often pose risks associated with open flames or contact heat sources, while precision induction heating equipment operates with minimal risk. The induction process generates heat within the material itself, reducing risks of burns or fires that commonly arise with conventional heating methods.
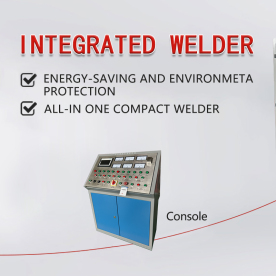
Exploring the Benefits and Applications of Precision Induction Heating Equipment in Modern Industries
However, like any technology, the implementation of precision induction heating equipment requires careful consideration. Factors such as the specific alloys being processed, the geometry of the parts, and the desired heating profiles must be evaluated to ensure the system is appropriately designed and set up for optimal performance. Additionally, the initial investment in precision induction heating technology can be significant, but the long-term savings in energy and efficiency often justify the expenditure.
In conclusion, precision induction heating equipment represents a significant advancement in heating technology with far-reaching implications across numerous industries. By providing energy-efficient, uniform, and precise heating solutions, it allows manufacturers to streamline operations, enhance product quality, and ensure the safety of processes. As technology continues to evolve, the potential applications and benefits of precision induction heating will likely expand, further solidifying its role as an essential tool in modern manufacturing and production environments.Precision Solid state HF welder