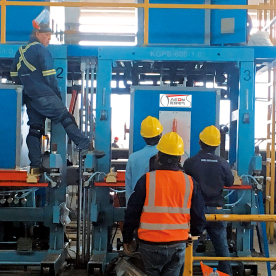
Unlocking the Power of Precision Induction Heating Equipment: Transforming Manufacturing with Enhanced Efficiency and Versatility
Precision induction heating equipment has emerged as a revolutionary technology in the manufacturing industry, offering unparalleled advantages in heating processes. As industries seek to enhance their production efficiency and precision, this equipment stands out by providing optimal heating solutions for a variety of applications. This article will delve into the intricacies of precision induction heating, exploring its principles, benefits, applications, and the future of this transformative technology.
At its core, induction heating is an electromagnetic heating method that employs high-frequency currents to generate heat directly in conductive materials. Precision induction heating equipment utilizes advanced technology to ensure that this heating is targeted and controlled, allowing for greater accuracy in the heating process. The equipment consists of an induction coil, a power supply, and a control system. The induction coil creates an electromagnetic field, which induces eddy currents within the workpiece, generating heat internally. This controlled heating process enables manufacturers to achieve precise temperatures, making it ideal for delicate applications where overheating can cause material degradation or undesirable outcomes.
One of the primary advantages of precision induction heating equipment is its efficiency. Traditional heating methods often waste energy through excessive heat loss to the surroundings. In contrast, induction heating focuses energy directly into the material, leading to rapid heating times and significant energy savings. This efficiency not only reduces costs but also contributes to the sustainability of manufacturing processes, as it minimizes energy consumption and lowers carbon footprints.
Another benefit worth noting is the enhanced control precision that this technology offers. With the ability to program specific heating profiles, manufacturers can achieve uniform heating across complex geometries, ensuring consistent performance across batches. This level of control is particularly critical in applications such as metal hardening, where precise temperature management is necessary to achieve the desired mechanical properties without compromising the integrity of the material. Furthermore, the quick start-up and shut-down times of precision induction heating equipment reduce idle times, allowing for more efficient production schedules and higher overall productivity.
The versatility of precision induction heating equipment also cannot be overlooked. It finds applications across a wide range of industries, including automotive, aerospace, medical, and electronics. In the automotive industry, for instance, induction heating is used for processes such as shrink fitting, brazing, and hardening components. It is particularly useful for applications requiring tight tolerances and minimal distortion, such as the hardening of gears and shafts.
In the aerospace sector, the technology plays a vital role in both manufacturing and maintenance. Precision induction heating is employed for the assembly of components, including rotating parts, where even minute changes in dimensions can have significant implications for performance. Additionally, in the medical field, this equipment is utilized for processes like sterilization and the welding of medical device components, where precision and reliability are paramount.
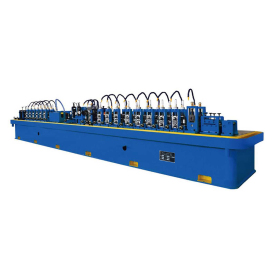
Unlocking the Power of Precision Induction Heating Equipment: Transforming Manufacturing with Enhanced Efficiency and Versatility
Despite the many advantages, adopting precision induction heating equipment does come with its challenges. Initial investment costs can be high, particularly for small to medium-sized enterprises. However, considering the long-term savings and efficiency gains, many find this investment justifiable. Furthermore, training and expertise are required to operate and maintain these systems effectively. Organizations must invest in upskilling their workforce to handle this advanced technology adequately.

Unlocking the Power of Precision Induction Heating Equipment: Transforming Manufacturing with Enhanced Efficiency and Versatility
Looking to the future, precision induction heating equipment is poised to become even more integral in modern manufacturing. As industries push for greater automation and integration into smart manufacturing frameworks, induction heating systems will be adapted to work seamlessly with IoT capabilities. Enhanced data analytics and control algorithms could lead to even greater efficiencies, proactive maintenance, and real-time monitoring, further elevating the role of precision induction heating in production processes.
In conclusion, precision induction heating equipment is transforming the manufacturing landscape through its efficiency, precision, and versatility. As industries continue to evolve, this technology will play a crucial role in meeting the demands of modern production while promoting sustainability and cost-effectiveness. Embracing precision induction heating equipment is not just a strategic choice; it is a forward-thinking approach that positions organizations for success in an increasingly competitive and technologically-driven market.Automatic Cold Cutting Saw Machine