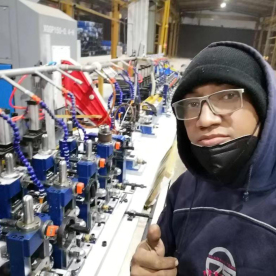
Enhancing Efficiency and Longevity in Metal Cutting with Precision-Made Spare Parts for Cold Cutting Saws
In the world of metal fabrication, efficiency and precision are paramount, particularly when it comes to using cold cutting saws. These tools are lauded for their ability to create clean, burr-free cuts in a variety of metal materials, which is essential for quality welding and assembly. However, the performance of cold cutting saws heavily relies on the quality and condition of their components. Precision-made spare parts for cold cutting saws play a crucial role in maintaining operational efficiency, ensuring longevity, and enhancing overall productivity in metalworking applications.
Cold cutting saws operate on a straightforward principle: they use a high-speed rotating blade to cut through metal without generating significant heat. This method helps to prevent thermal distortion and ensures the integrity of the material being worked on. Yet, like any machinery, these saws encounter wear and tear over time, necessitating the use of spare parts that are not just compatible but precisely engineered to restore optimal functionality.
One of the key advantages of utilizing precision-made spare parts is their fit and function. Unlike generic components, which may offer a quick fix but can lead to potentially detrimental outcomes, precision-made parts are designed to the exact specifications of the original equipment manufacturer (OEM). This enhances the overall performance of the cold cutting saw, reducing the likelihood of mechanical failures that can lead to costly downtime and repairs.
Moreover, precision-made spare parts are often manufactured from superior materials, which contribute significantly to their durability. In an environment where cutting metals subject tools to high stress, high-quality materials are essential for longevity. Enhanced durability translates to a longer lifespan for each component, reducing the frequency with which replacements must be made. This is particularly important in high-volume production settings, where uptime is critical for maintaining workflow and meeting client demands.
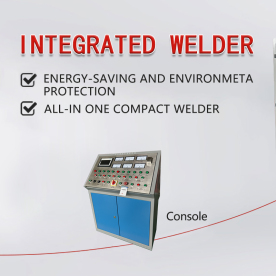
Enhancing Efficiency and Longevity in Metal Cutting with Precision-Made Spare Parts for Cold Cutting Saws
In addition to improving performance and longevity, precision-made spare parts can also enhance the quality of the cuts produced. When a cold cutting saw is equipped with parts that are precisely manufactured to suit its specifications, it operates more smoothly, leading to cleaner and more precise cuts. This not only minimizes the need for secondary finishing processes but also boosts the overall quality of the final product, which can be a decisive factor in the competitive realm of metal fabrication.
The economic benefits of using precision-made spare parts for cold cutting saws should not be overlooked. While the initial investment may be higher compared to generic alternatives, the long-term savings are significant. Reduced downtime, lower maintenance costs, and enhanced productivity can lead to a substantial return on investment. Companies that prioritize quality and precision in their machinery often find that they can operate more efficiently, keeping costs down while maximizing output.
Another vital aspect of maintaining cold cutting saws with precision-made spare parts is safety. Metal cutting tools can pose considerable hazards if not maintained properly. Components that are worn or not suitable for the equipment can lead to malfunction, jeopardizing the operator’s safety and risking significant injury. By investing in high-quality replacement parts, businesses not only ensure the performance of their equipment but also create a safer working environment.

Enhancing Efficiency and Longevity in Metal Cutting with Precision-Made Spare Parts for Cold Cutting Saws
Additionally, the availability of detailed specifications and support from manufacturers of precision-made spare parts can further ease the maintenance process. Having access to technical support and documentation ensures that operators and maintenance personnel can make informed decisions about repairs and replacements, ultimately enhancing the operational efficiency of their cold cutting saws.
In conclusion, precision-made spare parts for cold cutting saws are an integral part of any metalworking operation looking to improve efficiency, maintain high quality standards, and ensure safety. With their superior fit, durability, and associated economic benefits, these components provide a compelling case for investment. As industries continue to evolve and the demand for high-quality metal products increases, the reliance on precision engineering will only become more critical to success in the competitive marketplace of metal fabrication. By prioritizing the use of precision-made spare parts, businesses can pave the way for enhanced productivity and longevity in their metal cutting operations.Pipe making machine price comparison