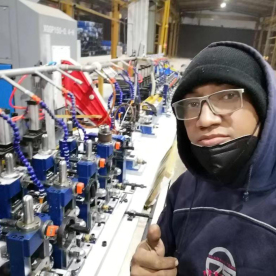
Exploring the Latest Advancements in Precision Pipe Making Equipment: Enhancements in Efficiency and Quality for Modern Manufacturing
In the evolving landscape of manufacturing, precision is a crucial factor that can make a significant difference in quality, reliability, and performance of the finished products. In industries that rely on piping systems—such as oil and gas, water management, and various manufacturing processes—precision pipe making equipment has become an essential cornerstone. This equipment not only enhances the efficiency of production but also ensures the highest standards of quality in the pipes produced.
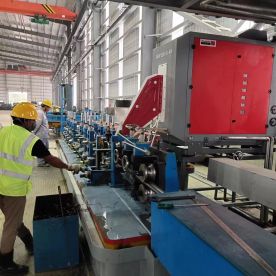
Exploring the Latest Advancements in Precision Pipe Making Equipment: Enhancements in Efficiency and Quality for Modern Manufacturing
Understanding the role of precision pipe making equipment requires a comprehension of the technologies and innovations that have emerged in recent years. Firstly, the term ‘precision pipe making equipment’ encompasses a wide range of machinery, including tube mills, pipe benders, seam welders, and inspection systems. Each of these categories has been significantly upgraded to meet the demands of contemporary markets where material efficiency, durability, and minimization of waste are of paramount importance.
One notable advancement in tube mill technology is the introduction of high-speed and highly automated systems. These tube mills now incorporate advanced servo motors and programmable logic controllers (PLCs), which allow manufacturers to produce pipes with extremely tight tolerances. This supports various applications, from structural pipes used in construction to high-pressure vessels required in the chemical and oil industries. Moreover, modern mills come equipped with real-time monitoring systems, which provide critical data regarding the performance of the equipment. This data aids operators in making informed decisions, thus reducing downtime and increasing overall productivity.
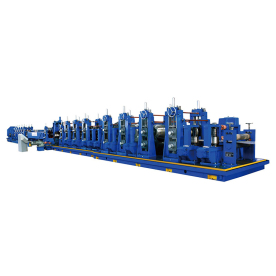
Exploring the Latest Advancements in Precision Pipe Making Equipment: Enhancements in Efficiency and Quality for Modern Manufacturing
Additionally, the integration of artificial intelligence (AI) into precision pipe making equipment signifies a transformative step in optimizing production processes. With AI algorithms analyzing machine performance and product quality, manufacturers can predict equipment failures before they occur, significantly reducing maintenance costs and unexpected downtimes. This predictive maintenance allows for a proactive approach, ensuring that the machinery operates at peak performance and longevity.
Furthermore, innovations in material science have led to the development of advanced piping materials like high-strength alloys and composite materials, which are produced with precision equipment. The ability to fabricate pipes made of high-strength materials while maintaining precise dimensions is essential in industries facing stringent safety regulations and performance criteria.
Another essential aspect of precision pipe making is the role of inspection equipment. High-quality pipes not only require precise manufacturing but also rigorous testing and quality control. Inspection machines equipped with laser measurement technologies and non-destructive testing capabilities ensure that each pipe meets industry standards. These advanced inspection systems detect any anomalies or defects in real-time, allowing for immediate corrections without halting the production line. Thus, manufacturers can maintain a steady output while ensuring that the quality of their products is uncompromised.
In addition to performance and efficiency, sustainability is becoming increasingly important for businesses worldwide. Precision pipe making equipment manufacturers are also taking strides towards sustainability by developing machines that consume less energy and produce less waste. This shift is aligned with global initiatives towards greener manufacturing practices. For instance, several advanced machines now incorporate processes that allow for reusing waste material, which not only enhances sustainability but can also lead to substantial cost savings for manufacturers.
The adoption of precision pipe making equipment does not come without its challenges. Investment costs for such advanced machinery can be substantial, making it a consideration for manufacturers to evaluate their return on investment. Additionally, there is a need for skilled personnel who can operate and maintain these sophisticated systems. Organizations are increasingly focused on training employees in the latest technologies and best practices to maximize the potential offered by their precision equipment.
In conclusion, precision pipe making equipment represents a significant advancement in the manufacturing sector. Through automation, artificial intelligence integration, and sustainable practices, manufacturers are not only enhancing their output but also contributing to the demands for higher quality and environmentally-friendly products. The future of precision pipe making looks promising, with technological innovations poised to further revolutionize the industry, ensuring industries worldwide have access to the essential piping systems that drive their operations. As we continue to innovate, the focus remains firmly on precision, quality, and sustainability—principles that will guide the manufacturing sector well into the future.Cost-Effective Spare Parts for Cold Cutting Saws