In the ever-evolving landscape of manufacturing, precision and efficiency have become paramount. Among the numerous innovations in this field, precision tube making equipment stands out as a critical component that ensures high-quality production of tubes and pipes used in various applications. From automotive to aerospace and medical industries, precision tubes are essential for structural integrity and functionality. This article explores the significance, advancements, and applications of precision tube making equipment, shedding light on how it revolutionizes production processes.
The Importance of Precision Tube Making Equipment
Precision tube making equipment refers to specialized machinery designed to produce tubes with exact dimensions, tolerances, and surface finishes. These tubes can be made from various materials, including metals, plastics, and composites, and are characterized by their uniformity and strength. The importance of this equipment cannot be overstated, as industries rely on precise specifications to ensure that products meet safety standards and performance criteria.
One of the primary benefits of precision tube making equipment is its ability to reduce material waste. Traditional tube fabrication methods often involve cutting and molding processes that result in significant off-cuts and scrap. However, advanced precision tube making machines utilize efficient processing techniques, minimizing waste and lowering production costs. This ecological and economical advantage is increasingly critical in a world that values sustainability.
Technological Advancements
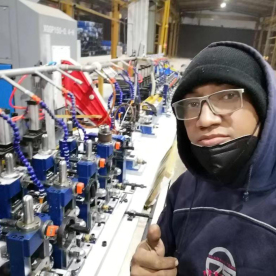
Revolutionizing Manufacturing: The Role of Precision Tube Making Equipment in Modern Industry
The landscape of precision tube making equipment has witnessed significant advancements over the years. One of the most notable developments is the incorporation of automation and advanced control systems. Modern equipment can now be operated with minimal human intervention, leading to improved consistency and efficiency in production. Automated machines can adjust parameters on-the-fly, responding to real-time feedback to maintain optimal performance.
Furthermore, CNC (Computer Numerical Control) technology has transformed precision tube making. CNC machines offer unparalleled levels of accuracy by following programmed instructions with extreme precision. This technology allows manufacturers to produce complex geometries and designs that would be challenging to achieve with manual processes. As a result, businesses can meet increasingly sophisticated market demands without sacrificing quality.
Another notable trend is the integration of Industry 4.0 principles within precision tube production. The Internet of Things (IoT) has made it possible to connect machines and systems, allowing for real-time monitoring and data analysis. Companies can track production metrics, machine health, and material usage, enabling predictive maintenance and enhancing overall productivity. This level of insight not only drives efficiency but also helps manufacturers make informed decisions about their operations.
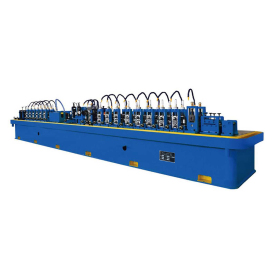
Revolutionizing Manufacturing: The Role of Precision Tube Making Equipment in Modern Industry
Applications Across Industries
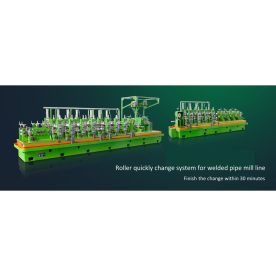
Revolutionizing Manufacturing: The Role of Precision Tube Making Equipment in Modern Industry
Precision tubes find applications in various industries, each with specific requirements that necessitate the use of precision tube making equipment. In the automotive sector, precision tubes are used for fuel lines, exhaust systems, and structural components. These tubes must withstand high pressures and temperatures while maintaining integrity. Precision tube making equipment enables manufacturers to produce tubes that meet the rigorous standards set by automotive regulations.
The aerospace industry is another significant consumer of precision tubes. Aircraft require lightweight yet durable tubing for hydraulic systems, fuel lines, and structural components. The reliability of these components is critical for safety and performance, making precision tube making equipment indispensable.
In the medical field, precision tubes are utilized in various applications, including catheters, syringes, and IV lines. Manufacturing these components requires strict adherence to regulations and cleanliness standards. Precision tube making equipment allows medical device manufacturers to produce high-quality tubes that meet the stringent requirements of this highly regulated industry.
Conclusion
As industries continue to demand higher precision and efficiency, the importance of precision tube making equipment cannot be overlooked. The advancements in technology, particularly in automation, CNC, and IoT integration, have revolutionized how precision tubes are manufactured. This equipment provides vital support across various sectors, from automotive to aerospace and medical devices, ensuring that products meet safety and performance standards.
In a world striving towards sustainability and efficiency, precision tube making equipment not only enhances the manufacturing process but also contributes to reducing waste and lowering production costs. As we look toward the future, it is clear that the role of precision tube making equipment will only grow, further solidifying its essential place in modern manufacturing.Original Spare Parts for Solid State HF Welders